Swiss Turning Services
Swiss turning, also known as Swiss machining or Swiss-style machining, is a precision manufacturing process that is highly effective for producing small, complex, and high-precision cylindrical parts.
-
Size Limit:20mm diameter * 400mm length
-
3-axis,5-axis and 8 axis are available
-
Tolerance as tight as +/- 0.01 mm
Precision Swiss Automatic Turning CNC lathe Machining Service:for Complex Cylindrical Parts | Yumei Precision
Why Us
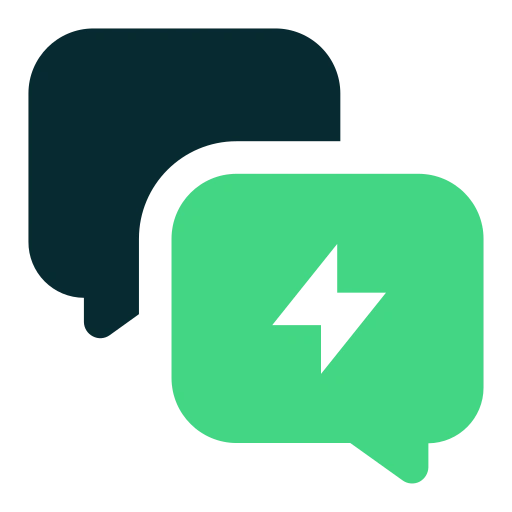
Quick Response
We will response your questions or inquiry within 1 hour during the working days. It's within 2 hours at weekends.
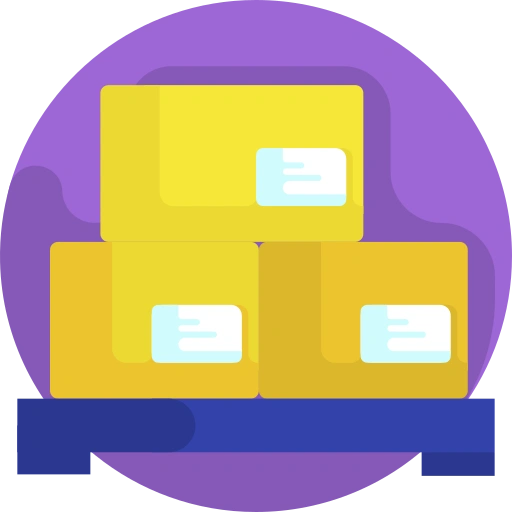
No MOQ
There is no MOQ requirement for most of our machined parts,we can start from 1 piece to 100K+ pieces, the more quantities, the better prices.

After-Sale Service
We are always caring for what you need. Your satisfaction is our motivation to make improvements and move forward.
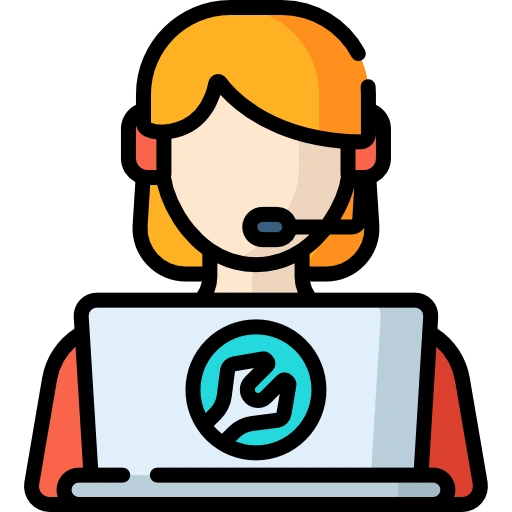
Technical Support
It includes but not limited to product selection, installation guideline and application know-how, etc.
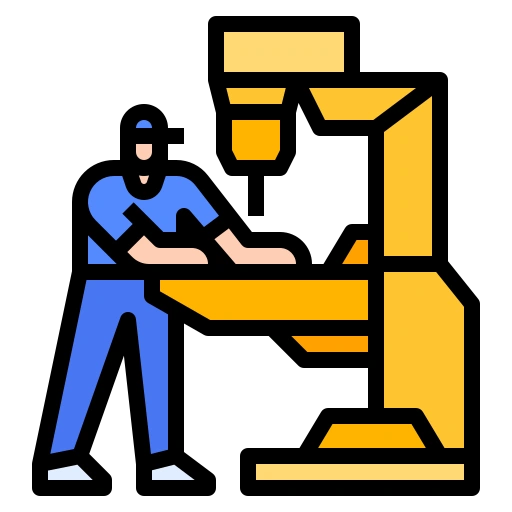
OEM/ODM Service
With 15 years' expertise and know-how, we have more than enough experience to be a qualified supplier. We can help you to reduce your cost.

Fast Delivery
It's within 48 hours for samples. 1-2 weeks for mass production. We have 150+ production devices and 102 workers to make it happen.
What’s Swiss turning ?
Swiss turning is a high-precision machining technology that combines CAD/CAM software with the manufacturing process. It has a wide range of applications, can process more materials, and have the characteristics of high speed and high rigidity, it can ensure high-precision production and adapt to the processing needs of complex parts, the processing method is widely used to improve the intelligence of precision parts production.
Swiss Turn Machining: The Art of Precision in Modern Manufacturing
Swiss turn machining is a specialized form of precision machining that has gained significant popularity in the manufacturing industry due to its ability to produce complex parts with high levels of accuracy and efficiency. This advanced technique, often referred to as Swiss-type turning, is a process that combines both turning and milling operations on a single machine, allowing for the creation of intricate parts with tight tolerances. Swiss automatic turn machining and Swiss CNC lathe machining are terms that are used interchangeably to describe this high-precision process.
History of Swiss Turn Machining
Swiss turn machining has its roots in the watchmaking industry of Switzerland, where precision and fine craftsmanship have been valued for centuries. The first Swiss turn machines were developed in the 19th century, initially to meet the demands of the watch industry, which required components with exacting specifications. Over time, Swiss turn machining evolved and became more sophisticated, with the development of automated tools and computer numerical control (CNC) systems. Today, Swiss turn machining is a staple in industries ranging from aerospace to medical devices, where precision and quality are paramount.
The Swiss Turn Machining Process
Swiss turn machining is performed on a Swiss-type lathe, which is designed with a sliding headstock and a guide bushing that supports the workpiece. The process involves the use of multiple tools that are mounted on a tool post, turret, or a tool belt, allowing for simultaneous operations. This setup enables the machine to perform multiple operations, such as turning, milling, drilling, and threading, in a single setup. The result is a part that is machined to exacting specifications with minimal waste material.
Advantages of Swiss Turn Machining
One of the primary advantages of Swiss turn machining is its ability to produce complex parts with a high degree of precision. The process allows for tight tolerances and fine surface finishes, which are essential in industries where performance and reliability are critical. Swiss automatic turn machining also offers increased efficiency, as multiple operations can be performed in a single setup, reducing the need for secondary operations and minimizing part handling.
Another significant advantage of Swiss turn machining is its ability to machine difficult-to-reach areas within a part. The sliding headstock and the use of live tools enable the machine to access areas that would be challenging or impossible to reach with conventional machining methods. This capability is particularly valuable in the production of intricate components with complex geometries.
Applications of Swiss Turn Machining
Swiss turn machining is widely used across various industries due to its versatility and precision. Some of the key applications include:
Aerospace: In the aerospace industry, Swiss turn machining is used to produce components such as fuel nozzles, turbine parts, and complex fittings that require high precision and strength-to-weight ratios.
Medical Devices: Swiss turn machining is ideal for the production of small, intricate components used in medical devices, such as implants, surgical instruments, and diagnostic equipment.
Automotive: Swiss turn machining is employed in the automotive industry to manufacture parts like fuel injectors, transmission components, and complex fasteners.
Electronics: In the electronics industry, Swiss turn machining is used to produce precision components such as connectors, terminals, and small gears for various electronic devices.
Jewelry: Swiss turn machining is also used in the jewelry industry to create intricate and delicate pieces with a high level of detail.
The Role of Automation in Swiss Turn Machining
Automation plays a crucial role in Swiss turn machining, enhancing both the efficiency and precision of the process. Modern Swiss-type lathes are equipped with CNC systems that allow for the programming of complex machining sequences, ensuring repeatability and consistency in the production of parts. Additionally, automated tool changers and bar feed systems enable uninterrupted operation, further increasing productivity.
Swiss Automatic Turn Machining
Swiss automatic turn machining is a sophisticated manufacturing process that builds upon the traditional Swiss turn machining techniques. This method is highly automated, allowing for a high level of precision and efficiency in the production of small, complex parts. Swiss automatic turn machining utilizes advanced CNC systems to control the movement of the cutting tools and the workpiece with exceptional accuracy. The process is characterized by its ability to perform multiple operations such as turning, milling, drilling, and threading in a single setup, which significantly reduces production time and increases output.
Swiss CNC Lathe Machining
Swiss CNC lathe machining refers to the use of CNC lathes that are specifically designed for Swiss-type turning. These machines are renowned for their precision and ability to produce parts with complex geometries and tight tolerances. Swiss CNC lathes are equipped with a sliding headstock and a guide bushing that supports the workpiece, which allows for the close tolerance machining of intricate parts.
Swiss CNC lathe machining is highly versatile and can handle a wide range of materials, including but not limited to steel, stainless steel, aluminum, brass, and plastics. The process is ideal for manufacturing components that require high precision and have complex features, such as those found in the watchmaking, medical, aerospace, and automotive industries.
One of the main advantages of Swiss CNC lathe machining is its ability to machine difficult-to-reach areas within a part, thanks to the live tools and the sliding headstock design. This capability allows manufacturers to create parts with internal and external features that would be challenging or impossible to achieve with conventional CNC lathes.
Swiss CNC lathe machining also offers excellent surface finishes due to the precise control over the cutting tools and the ability to use high-speed cutting techniques. The machines are designed to maintain the highest level of precision, ensuring that each part meets the stringent requirements of the application it is intended for.
The Future of Swiss Turn Machining
As technology continues to advance, Swiss turn machining is expected to evolve, incorporating new materials, processes, and technologies. The integration of additive manufacturing, for example, could allow for the production of even more complex geometries. Furthermore, the development of more advanced CNC systems and machine learning algorithms will likely lead to greater optimization of machining processes, resulting in improved efficiency and reduced downtime.
Training and Skill Development in Swiss Turn Machining
The demand for skilled operators in Swiss turn machining is on the rise, as the complexity of the machines and the precision required for the work increases. Training and skill development are essential to ensure that machinists are equipped to handle the challenges of this specialized form of machining. This includes understanding the machine's capabilities, programming the CNC systems, and maintaining the equipment to ensure optimal performance.
Swiss Turn Machining and Sustainability
Swiss turn machining also plays a role in sustainability, as the process is designed to minimize material waste. The ability to machine complex parts in a single setup reduces the need for secondary operations, which can be both time-consuming and wasteful. Additionally, the use of high-quality materials and precision machining techniques can lead to the production of parts that are more durable and have a longer service life, reducing the need for replacement and disposal.
Challenges in Swiss Turn Machining
Despite its many advantages, Swiss turn machining does present some challenges. The initial investment in Swiss-type lathes can be significant, and the machines require skilled operators to achieve the best results. Additionally, the process can be limited by the size of the workpiece, as Swiss-type lathes are typically designed for small to medium-sized components.
Swiss turn machining, including Swiss automatic turn machining and Swiss CNC lathe machining, is a precision machining technique that has proven its worth in various industries. Its ability to produce complex parts with tight tolerances and fine surface finishes makes it an invaluable tool in modern manufacturing. As technology continues to advance, Swiss turn machining is expected to evolve, offering even greater precision and efficiency. The demand for skilled operators in this field is on the rise, highlighting the importance of training and skill development. Swiss turn machining not only contributes to the production of high-quality components but also plays a role in sustainability by minimizing material waste. Despite the challenges it faces, Swiss turn machining remains a key technology in the pursuit of precision and excellence in manufacturing.
Materials of Swiss turning
Swiss turning processing materials are metals, plastics, the following is the commonly used processing materials:
Material | |
---|---|
Carbon Steel | Low-carbon steel, High-carbon steel |
Stainless Steel | Stainless Steels303, Stainless Steels304, Stainless Steels316, Stainless Steel 440c |
Alloy Steel | Alloy Steels 4140, Alloy Steels 4340 |
Brass | Brass c37700, Brass c36000, Brass c26000, Brass c27000, Brass c28000 |
Aluminum | Aluminum 6061-T6, Aluminum 6061-T651, Aluminum 7075-T6, Aluminum 7075-T7351, Aluminum 2024-T3, Aluminum 5052, Aluminum 6063-T5, Aluminum 7050-T7451 |
Plastics | PEEK, Nylon, Acetal [Delrin] |
Bronze | Phosphor Bronze |
Surface Treatment of Swiss turning
-
Polishing
Polishing is the use of polishing tools and abrasive particles to reduce the surface roughness of the workpiece, become bright and flat processing method, but it can not improve the accuracy of dimension and shape.
-
Heat Treatment
Heat treatment is to change the internal organization of the material in the solid state under heating - insulation - cooling to obtain new properties, which it can not only improve the heat resistance and corrosion resistance of the material, but also improve the hardness of the material to ensure practicality.
-
Sand Blasting
Sand Blasting is the high-speed spraying of sand or other media on the surface of the material, through the impact of the surface to clean up impurities such as stains and rust stains and improve the surface roughness and adhesion.
-
Zinc Plated
Zinc plated can make the surface of the material is not corroded by chemical substances such as oxygen and water, extend the service life of the product, and has the characteristics of strong corrosion resistance, high surface gloss and low maintenance cost.
-
Anodization
Anodization can enhance the corrosion resistance, abrasion resistance, electrical conductivity and insulation properties of the parts, and beautify of the appearance. It is widely used in automotive, aerospace and electronic products and other fields, can improve product performance and quality.
-
Chemical Film
The surface treatment method of chemical film is more environmentally friendly, easy to handle, can also simplify the process, reduce investment costs, and save energy.
Tolerances of Swiss turning
Swiss turning is characterized by high precision and miniaturized design.
As per standard ASME | Y14.5 or ISO2768,±0.01mm min |
---|---|
Size Limit | 20mm diameter * 400mm length |
Advantages Of Swiss turning
-
High precision
Swiss turning can process very fine parts due to high precision, which makes it very popular in the processing and manufacturing of high-precision parts which can reduce errors, production costs, and maximize benefits.
-
Low costs
Swiss turning have superior durability and can produce high-volume parts, reduce errors and time costs, and maximize benefits.
-
Stability
Swiss turning has superior stability, high precision operation over a long period of time, mass production, precision production and continuous production, it can improve production efficiency and save costs.
Conclusions
Swiss turning can ensure high-precision production, have a variety of materials and a wide range of applications. Not only it can save production costs, but also improve production efficiency. The above is a brief introduction to show our the method of Swiss turning, including materials, precision machining, accuracy and benefits, so that you can tell us your manufacturing goals when you realize them.