threaded stud – Yumei Precision
Explore Sheet Metal Fabrication Manufacturing near Me | Yumei Hardware
Yumei is a high quality China supplier with a state-of-the-art factory in Dongguan. Our 15+ years of experience in CNC machining and sheet metal fabrication have made us a preferred choice in over 8 countries, including Japan and the US. We are committed to our vision of being a leading global manufacturer, driven by innovation and customer satisfaction.
Discovering Local Metal Sheet Fabrication: from Manufacturing to Customization
When seeking "sheet metal fabrication near me," we're not just looking for convenience in terms of location; we're searching for a high-quality service that meets our specific needs. Metal sheet fabrication, as a precise manufacturing process, has become integral to every aspect of our daily lives.
"Sheet metal manufacturing" is a field that encompasses a broad range of technologies, including cutting, stamping, bending, and welding. These processes allow metal sheets to be shaped into various complex forms and structures, meeting the needs of industries from construction to aerospace. As technology continues to advance, the "sheet metal manufacturing" industry is also constantly improving its production efficiency and product quality.
For clients requiring customized metal sheet solutions, "metal sheet fabrication near me" becomes particularly important. This service not only offers rapid response times but also produces items tailored to specific client needs. Whether it's metal sheets of custom dimensions or products with special coatings or surface treatments, "metal sheet fabrication near me" provides a one-stop solution.
In "sheet metal fabrication near me" services, clients can expect not only quick delivery times but also professional technical support. These service providers typically have advanced equipment and experienced technicians to ensure every project meets the highest industry standards. Whether it's mass production or one-off customization, "sheet metal fabrication near me" offers flexible production options.
Another advantage of "sheet metal manufacturing" is its sustainability. With growing environmental awareness, many metal sheet fabrication service providers are adopting greener materials and processes. This not only helps reduce energy consumption during production but also minimizes environmental impact. Choosing "sheet metal manufacturing" is choosing a production method that is responsible to the environment.
When selecting "metal sheet fabrication near me" services, clients should consider the service provider's experience and reputation. A good service provider can offer not only high-quality products but also timely customer service and technical support. By choosing a reliable "metal sheet fabrication near me" service, clients can ensure their projects are completed on time and within budget.
whether it's "sheet metal fabrication near me," "sheet metal manufacturing," or "metal sheet fabrication near me," these services are an indispensable part of modern manufacturing. They not only provide high-quality metal sheet products but also offer customized and eco-friendly production solutions. As technology continues to advance, we can expect these services to continue driving industry innovation and development.
Hot Products
Sheet Metal Manufacturing Products
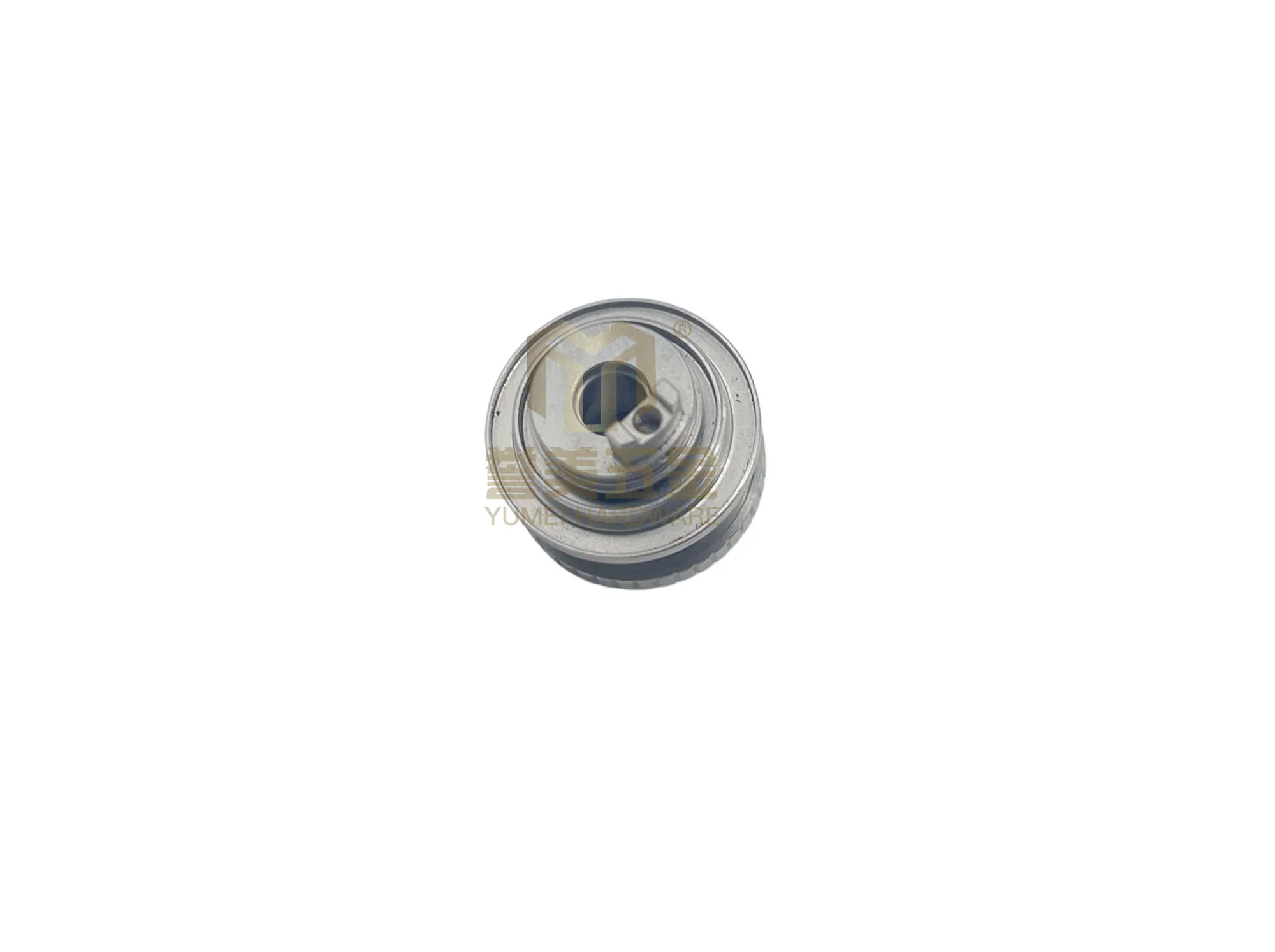
Blulu s Assortment of 24 Units - 304 Grade Stainless Steel Strips, Each Measuring 1 Wide by 12 Long, Comprising an Array of 8 Distinct Thicknesses, Ideal Thin Metal Sheets for Versatile Applications in Kitchenware...
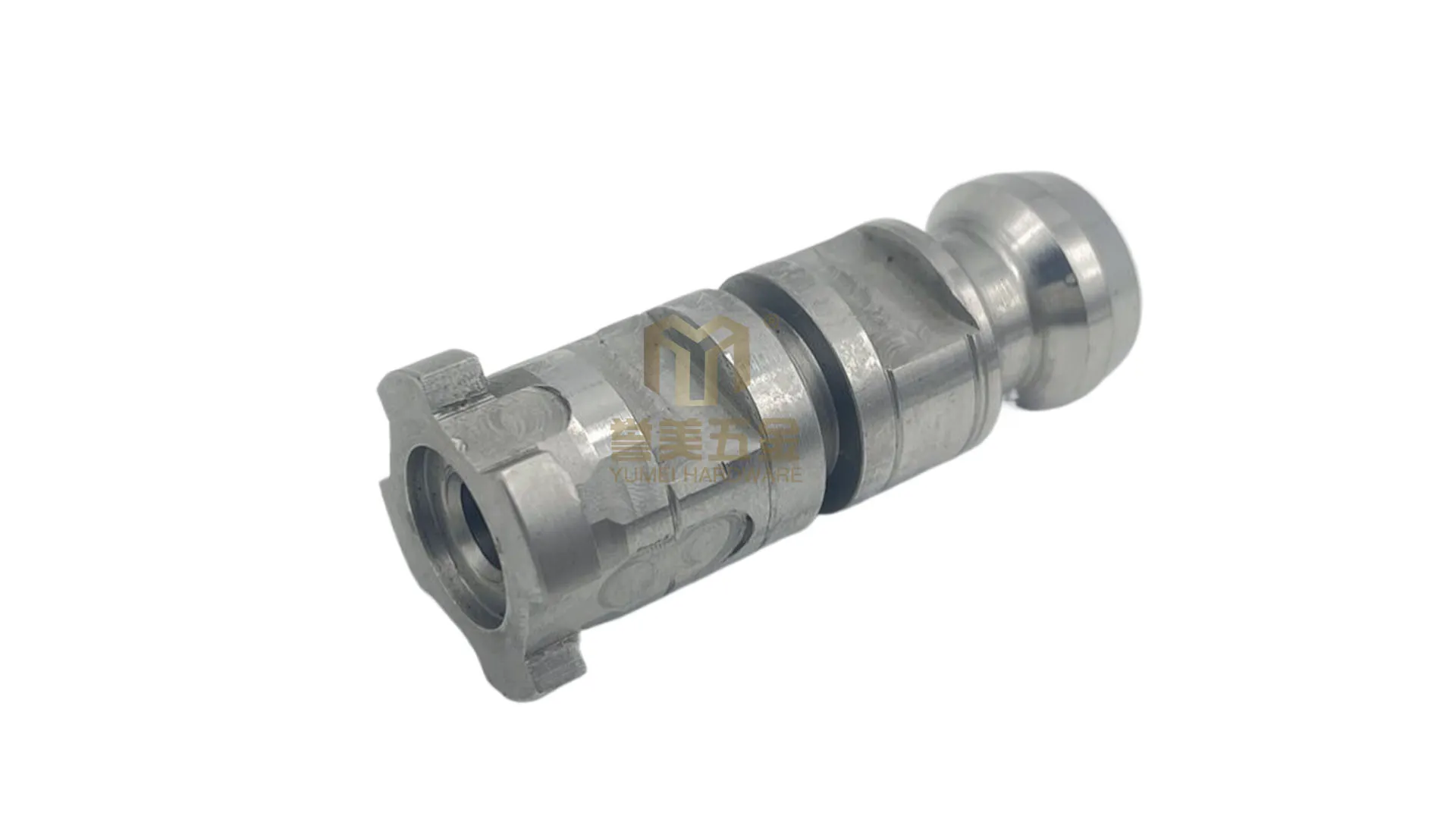
A set of 6 PCS, featuring 4 dimensions, comprises Heavy-Duty Steel Sheet Base Plates, each crafted with a Flat Straight Backing Plate design. These plates boast a Flat Square Sheet configuration and possess a robust 4 Gauge Steel Thickness, measuring pre
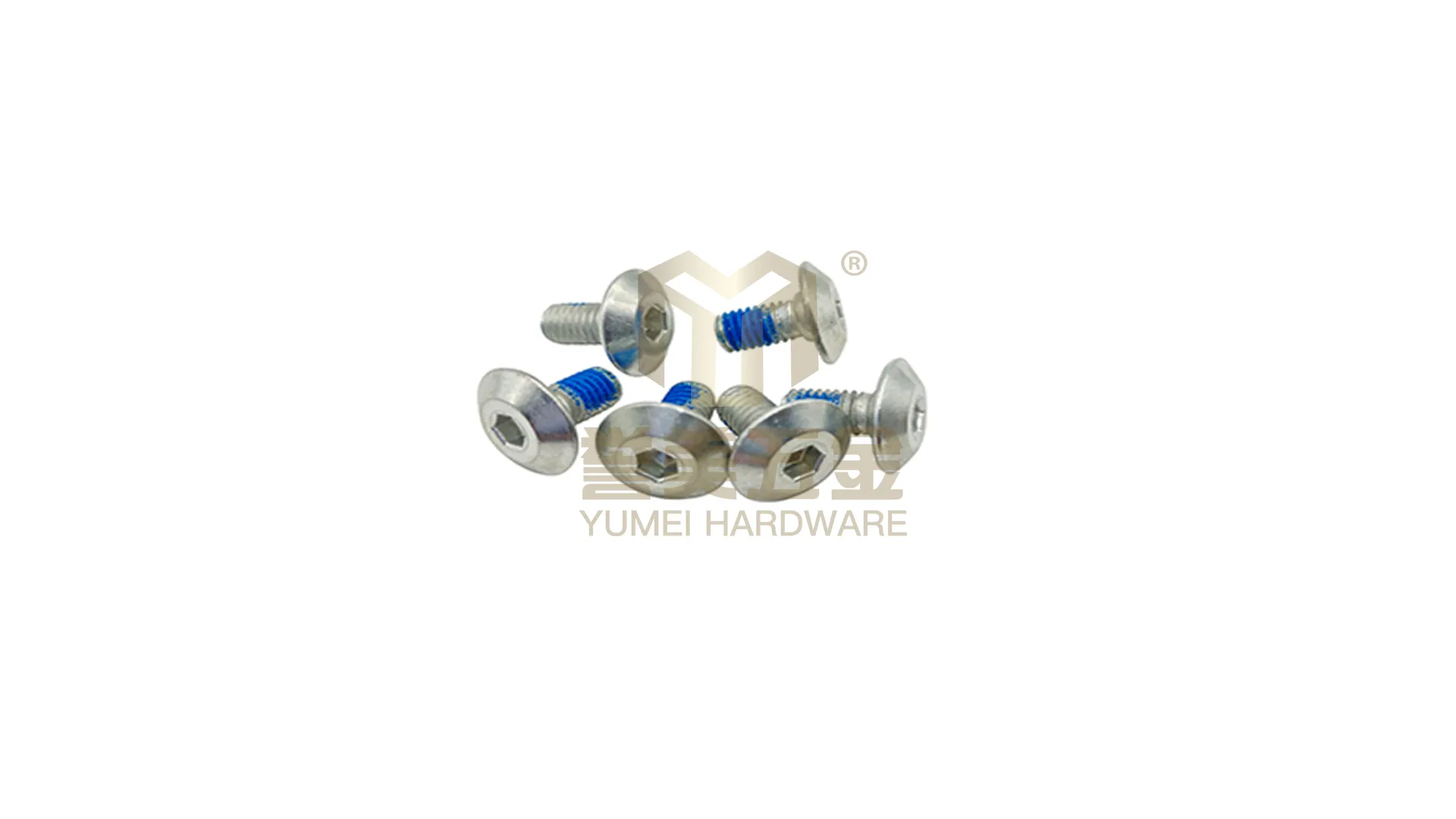
Six units of Brass Sheets, each measuring 6 inches by 6 inches, crafted from 20 Gauge material, equivalent to a thickness of 0.8mm. These brass plates are uniquely designed with a double-sided film attachment, providing versatility and protection. They se
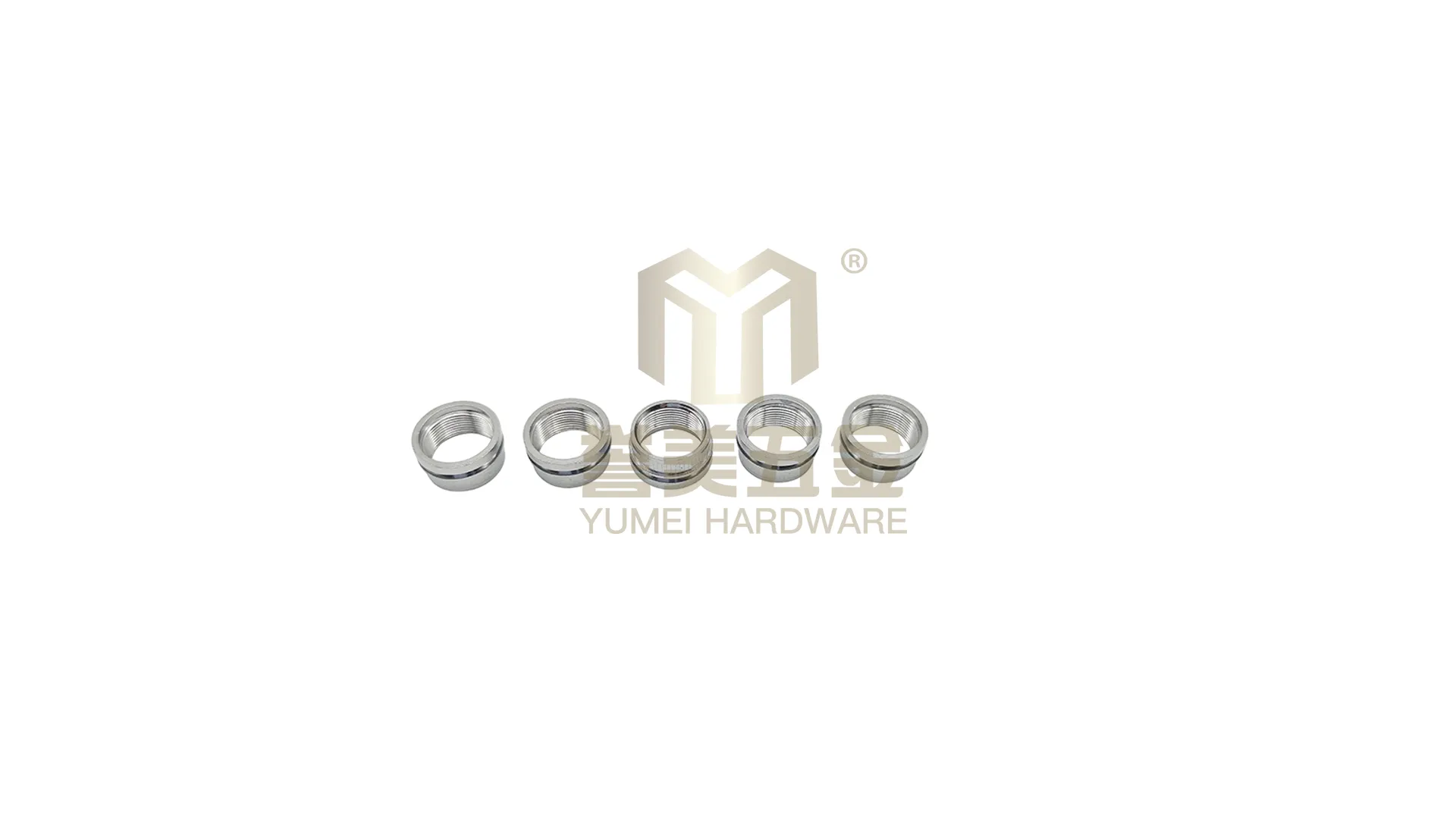
Advanced Electric Drill Accessory for Plate Cutting - Metal Nibbling Attachment, Including Adapter for Versatile Sheet Metal Cutting, DIY Compatible Metal Drill Enhancement...
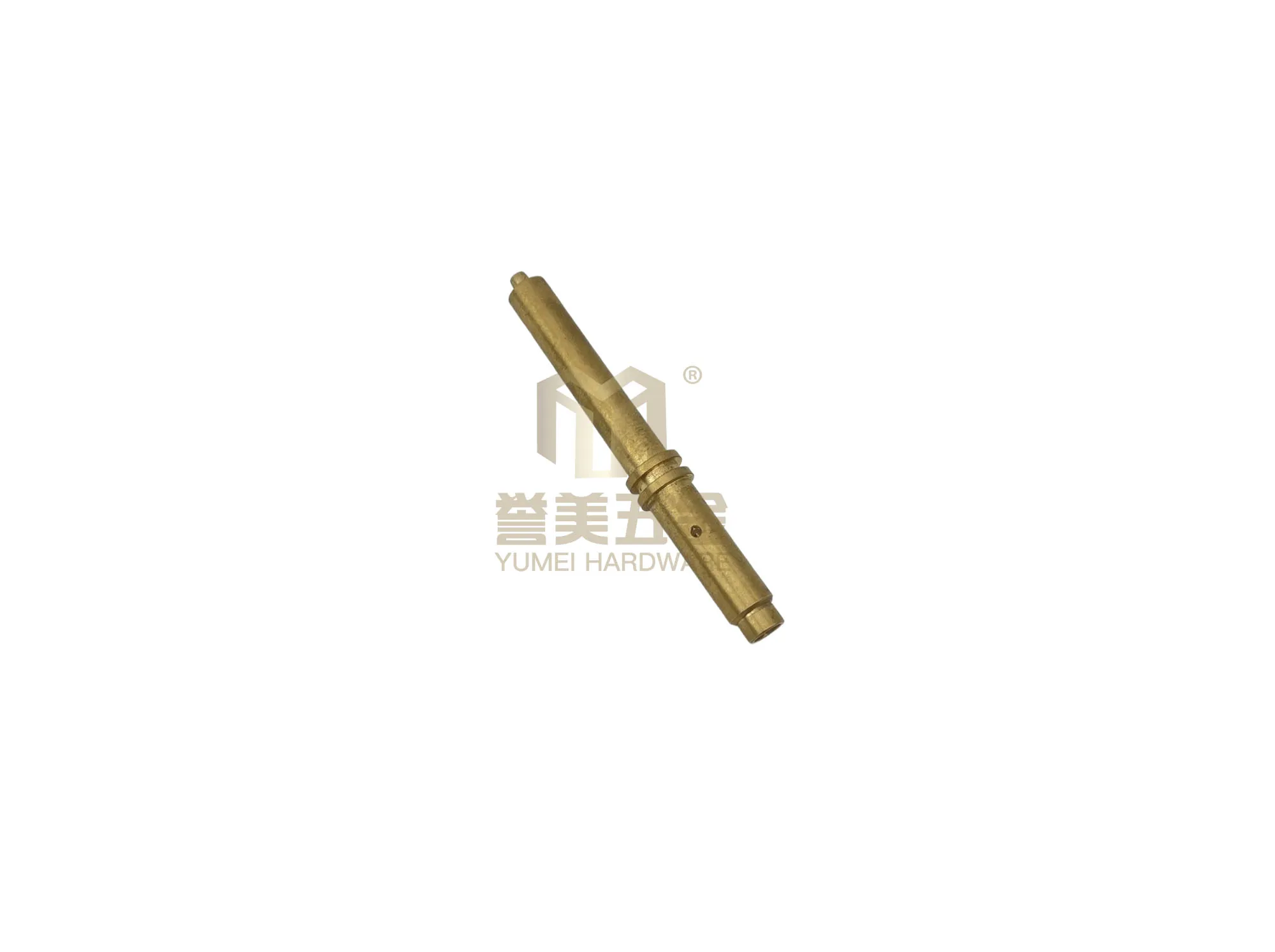
A roll of galvanized wire mesh, featuring a 1/8 inch hardware cloth configuration, measures 24 inches wide by 10 feet in length.
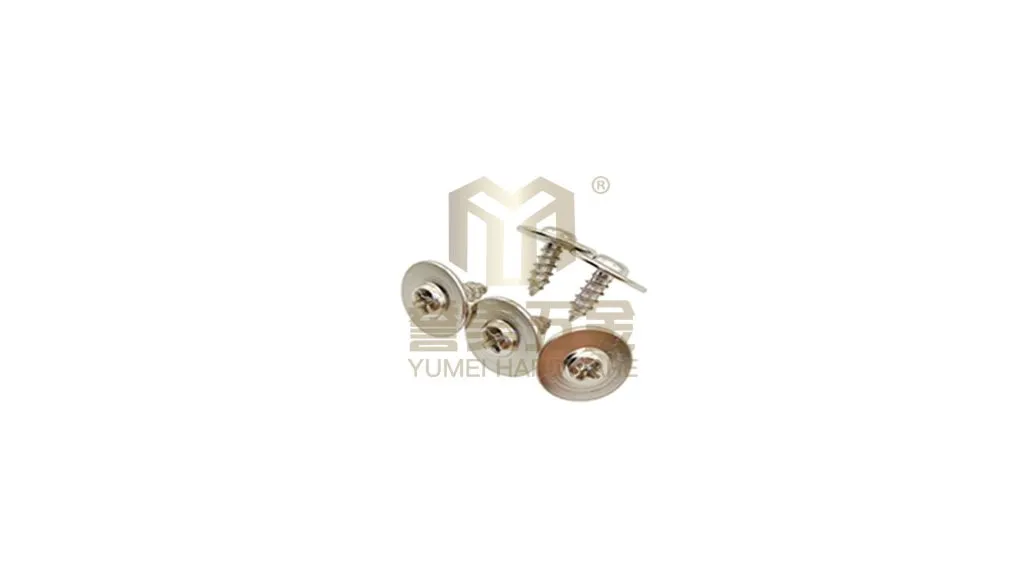
The eoere product comprises of 4 individual pieces of robust, 12-inch by 4-inch, hot-rolled flat steel plates, featuring a straight and sturdy backing design. These square-shaped, weldable steel plate sheets exhibit a thickness dimension of 7/32 , ensurin
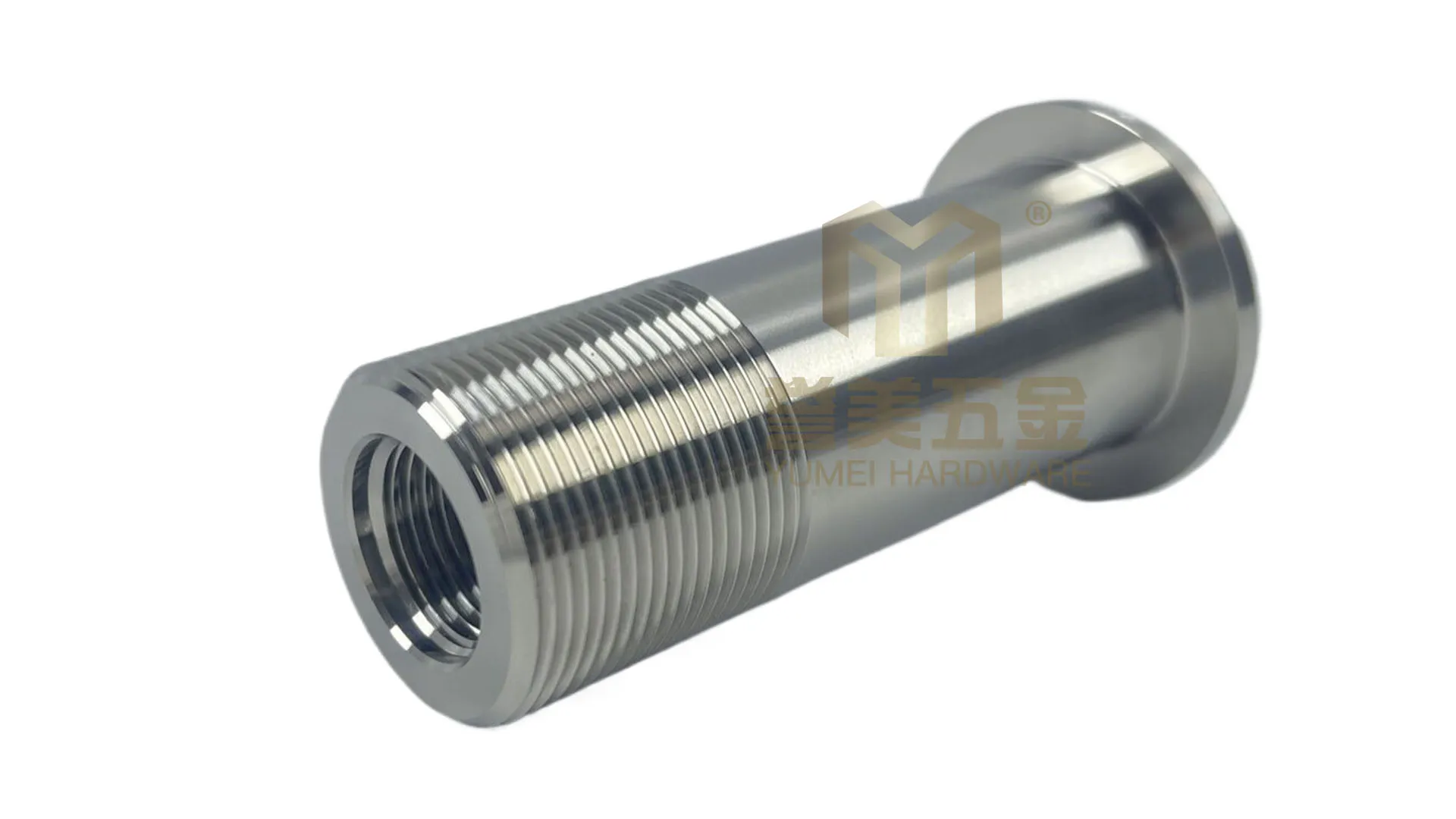
#10 in diameter by 3 in length, Flat Head Sheet Metal Fasteners, Phillips-Style Self-Tapping Screws for Wood Applications, Crafted from 18-8 (304) Grade Stainless Steel, Featuring a Natural, Uncoated Finish...
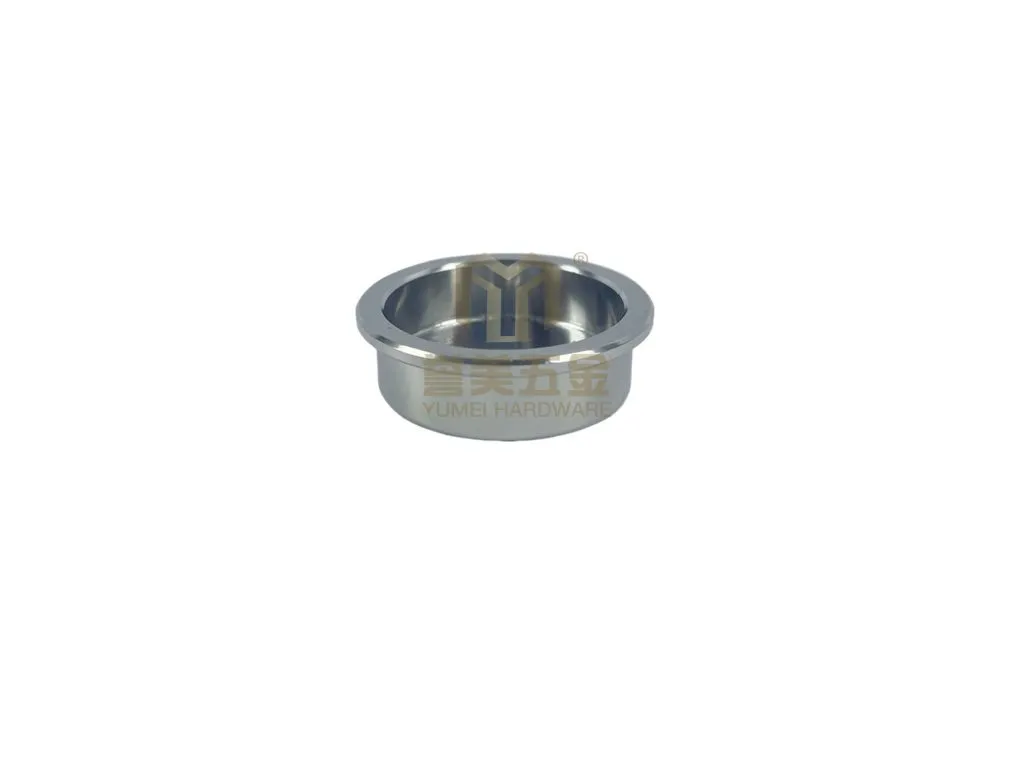
Two Units of 12 x 12 x 1/8 Thick 6061 Aluminum Alloy Sheet, Precisely Finished 300mm x 300mm x 6mm Aluminum Tooling Plate, Aluminum Panel...
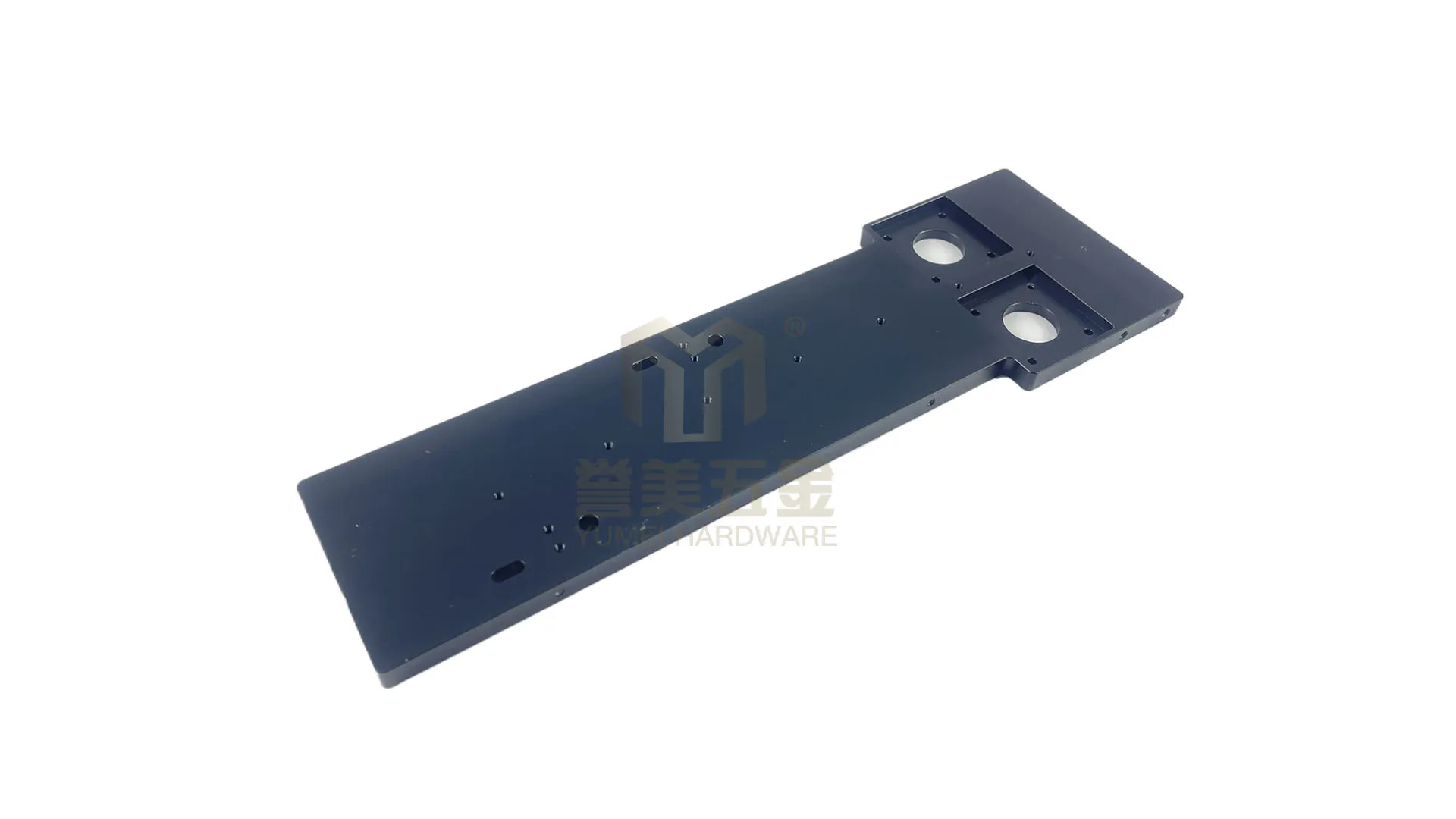
Tornado 10-Inch Aviation-Grade Tin Snippers, Ideal for Metal Sheet Trimming, Durable Sheet Metal Shears with High-Performance Cr-Mo Alloy, Straight Pattern...
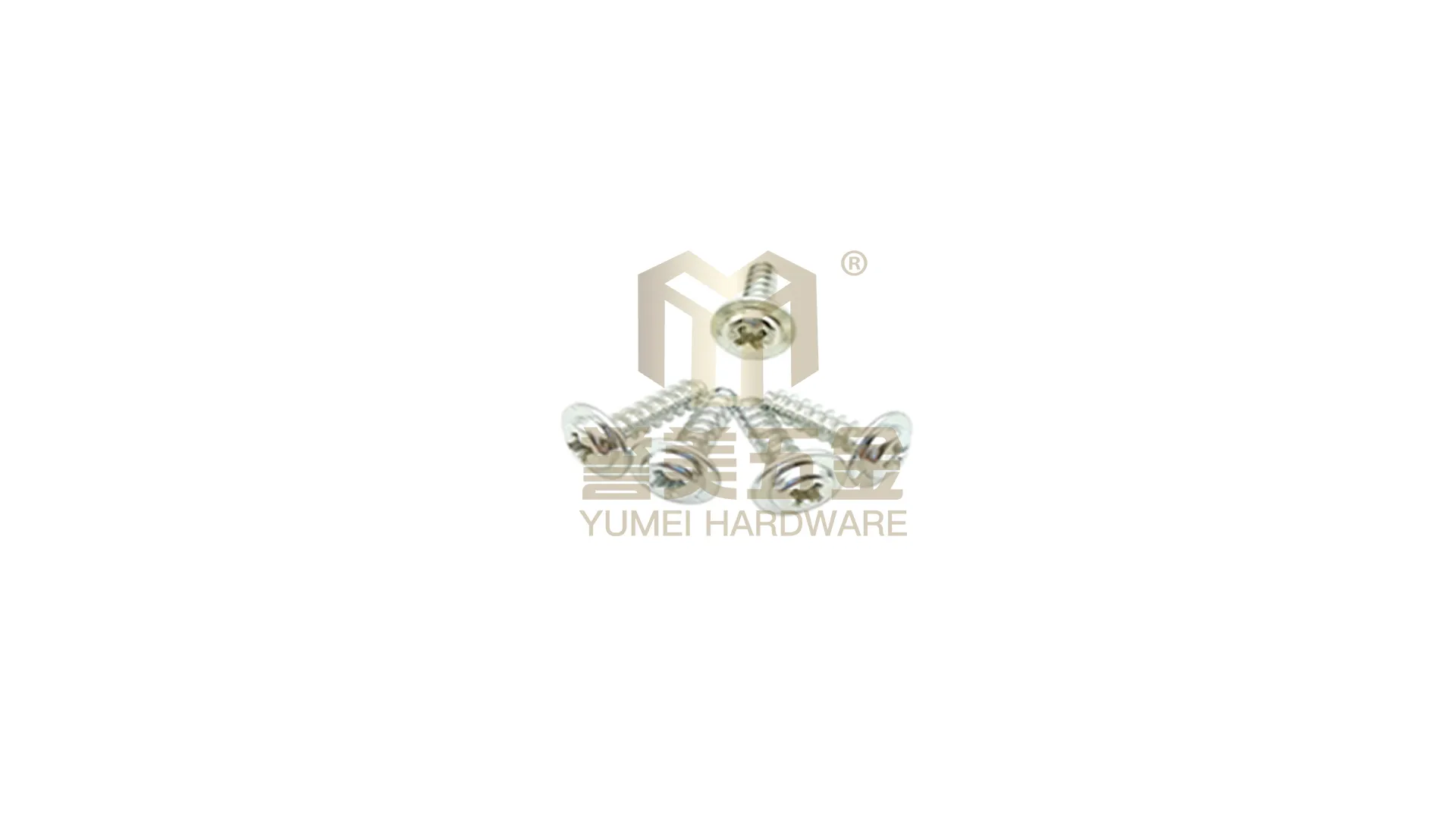
Six-Piece Set of 6-by-6-Inch Premium Pure Copper Sheets, 22 Gauge Thick (0.03 Approximate), Ideal Copper Plate Material for Artistic Crafts, Restoration Work, Enameling Techniques, Electrical Applications, and More...
People May Ask
Numerous diverse metallic materials possess the capability to be transformed into sheet metal formats, encompassing aluminum, brass, copper, steel, tin, nickel, and titanium among others. When it comes to aesthetic applications, several crucial sheet metal varieties include silver, gold, and platinum, with platinum sheet metal additionally serving as a valuable catalyst in various industrial processes.
The most expensive and highest-quality arc welding method is gas tungsten arc welding (TIG). Although most of the time it is done manually, there are some automatic apps. A skilled welder can deposit half a pound of weld metal every hour at a speed of one to three inches per minute.
Fabrication welding, in a nutshell, is the process of creating metal structures. Numerous techniques, including as welding, cutting, assembling, slicing, and binding, are used to accomplish this. Aluminum, steel, and other ferrous and non-ferrous metals are utilized during the production process.
Fabricators are those who create a variety of goods with different raw materials, equipment, and their own hands. Reading and comprehending assembly instructions, making sure all necessary parts are present, and adhering to quality control requirements are their main duties.
Rough sketches, paper models, straightforward storyboards, or rough paper prototypes of digital interfaces are examples of low-fidelity prototypes. Depending on the kind of solution you want to develop, you would base your prototype selection on that.
Metals can be divided into three categories: ferrous metals, non-ferrous metals, and alloys.