threaded stud – Yumei Precision
China Online High Quality Cnc Machining Titanium for Sale | Yumei Precision
Yumei, your reliable high quality supplier in Dongguan, China, is a factory and manufacturer with a legacy of precision and innovation. Our 15+ years in the industry have seen our products make their mark in over 8 countries, including Brazil and Mexico. We aspire to be a beacon of excellence in the manufacturing world, always pushing the boundaries of what's possible.
CNC Machining Titanium: A Comprehensive Guide to Precision And Innovation in Modern Manufacturing
In the world of advanced manufacturing, few materials have garnered as much attention and respect as titanium. Known for its exceptional strength, lightweight properties, and remarkable resistance to corrosion, titanium has become a go-to material for industries ranging from aerospace to medical devices. However, machining titanium is no small feat; it requires precision, expertise, and state-of-the-art technology. This is where CNC (Computer Numerical Control) machining comes into play.
Yumei, a leading manufacturer based in Dongguan, China, has been at the forefront of this technological revolution. With over 15 years of experience, Yumei has established itself as a reliable high-quality supplier of CNC machined titanium products. Their commitment to precision and innovation has seen their products make a significant impact in over eight countries, including Brazil, Germany, Japan, Italy, France, and Mexico.
This article delves into the world of CNC machining titanium, exploring the intricacies of the process, the benefits of using titanium, and how Yumei has become a global leader in this niche market.
The Importance of Titanium in Modern Manufacturing
Titanium is a transition metal with the chemical symbol Ti and an atomic number of 22. It is known for its high strength-to-weight ratio, making it an ideal material for applications where weight is a critical factor. Here are some of the key properties of titanium that make it so valuable in manufacturing:
High Strength and Low Density: Titanium is approximately 45% lighter than steel but has a comparable strength, making it an excellent choice for applications where weight reduction is crucial.
Corrosion Resistance: Titanium is highly resistant to corrosion, even in harsh environments. This makes it ideal for use in marine applications, chemical processing, and medical implants.
Biocompatibility: Titanium is well-tolerated by the human body, making it a popular choice for medical implants and devices.
High-Temperature Performance: Titanium maintains its strength at high temperatures, making it suitable for use in aerospace and automotive applications.
Non-Magnetic: Unlike many other metals, titanium is non-magnetic, which is beneficial in applications where magnetic interference is a concern.
The Role of CNC Machining in Titanium Production
CNC machining is a process that uses computer-aided design (CAD) and computer-aided manufacturing (CAM) software to control machine tools. This technology allows for the precise cutting, shaping, and drilling of materials, including titanium. Here's why CNC machining is crucial for titanium production:
Precision: CNC machines offer unparalleled precision, ensuring that each part meets the exact specifications required.
Efficiency: Automated processes reduce the time and labor required to produce parts, leading to increased efficiency and cost savings.
Complexity: CNC machines can handle complex geometries and designs that would be difficult or impossible to achieve with manual machining.
Repeatability: The use of computer programs ensures that each part produced is identical to the last, maintaining consistency in quality.
Material Savings: CNC machining allows for minimal material waste, as the machines can be programmed to use the exact amount of material needed for each part.
Yumei: A Leader in CNC Machining Titanium
Yumei's commitment to excellence in CNC machining titanium has been the cornerstone of their success. Here's how they have established themselves as a global leader:
Experience: With over 15 years in the industry, Yumei has honed their skills and knowledge, ensuring that they can meet the most demanding requirements.
Quality: Yumei is dedicated to producing high-quality products that meet or exceed industry standards.
Innovation: They are always at the forefront of technology, investing in the latest CNC machinery and software to stay ahead of the competition.
Global Reach: Yumei's products are trusted and used in over eight countries, showcasing their ability to meet diverse international standards.
Customization: They offer a wide range of customization options, allowing clients to specify the exact specifications and designs they require.
The Process of CNC Machining Titanium
The process of CNC machining titanium involves several steps, each of which is crucial to the final product's quality. Here's a detailed look at the process:
Design and Planning: The first step is to create a detailed design of the part using CAD software. This design is then translated into a set of instructions for the CNC machine using CAM software.
Material Selection: High-quality titanium is selected based on the specific requirements of the project, including its grade, purity, and form (sheet, bar, or plate).
Setup: The CNC machine is set up with the appropriate tools, fixtures, and materials. This step is crucial for ensuring that the machining process runs smoothly and efficiently.
Machining: The CNC machine follows the programmed instructions to cut, shape, and drill the titanium. This process is highly automated, with minimal human intervention required.
Inspection and Quality Control: After machining, the parts are inspected for accuracy and quality. Any defects or deviations from the specifications are corrected before the parts are approved for use.
Finishing: Depending on the application, the machined parts may undergo additional processes such as polishing, coating, or heat treatment to enhance their properties.
Packaging and Shipping: Once the parts have passed all quality checks, they are packaged and shipped to the client.
Benefits of CNC Machining Titanium
The benefits of CNC machining titanium are numerous and contribute to the material's widespread use in various industries:
Enhanced Productivity: The automated nature of CNC machining allows for faster production times, leading to increased productivity.
Reduced Human Error: By relying on computer programs, the risk of human error is minimized, ensuring consistent quality.
Improved Surface Finish: CNC machines can achieve a high-quality surface finish, which is essential for many applications.
Cost-Effective: While the initial investment in CNC machinery may be high, the long-term cost savings in terms of labor, material, and efficiency make it a cost-effective solution.
Customization: The flexibility of CNC machining allows for the production of complex, customized parts that meet the unique needs of each client.
Applications of CNC Machined Titanium
CNC machined titanium finds applications in a wide range of industries due to its unique properties:
Aerospace: Titanium is used in aircraft engines, landing gear, and structural components due to its strength and lightweight properties.
Medical: Titanium is a popular choice for implants and prosthetics due to its biocompatibility and corrosion resistance.
Automotive: Titanium is used in high-performance vehicles for components such as engine parts, suspension systems, and exhaust systems.
Marine: The corrosion resistance of titanium makes it ideal for use in marine applications, such as propellers, hulls, and underwater equipment.
Industrial: Titanium is used in chemical processing and power generation industries for components that must withstand high temperatures and corrosive environments.
Challenges in CNC Machining Titanium
Despite its many benefits, CNC machining titanium also presents some challenges:
High Tool Wear: The hardness of titanium can lead to rapid tool wear, requiring frequent tool changes and maintenance.
Heat Generation: The machining process can generate significant heat, which can cause the titanium to expand and distort if not managed properly.
Galling: Titanium has a tendency to gall or seize up during machining, which can damage both the tool and the workpiece.
Cost: The initial cost of titanium and the specialized machinery required for CNC machining can be high.
CNC machining titanium is a critical process in modern manufacturing, enabling the production of high-strength, lightweight, and corrosion-resistant parts for a variety of industries. Yumei, with its commitment to precision, innovation, and quality, has established itself as a global leader in this field. As technology continues to advance, the capabilities of CNC machining titanium will only grow, opening up new possibilities for innovation and excellence in manufacturing.
Hot Products
Cnc Machining Titanium Products
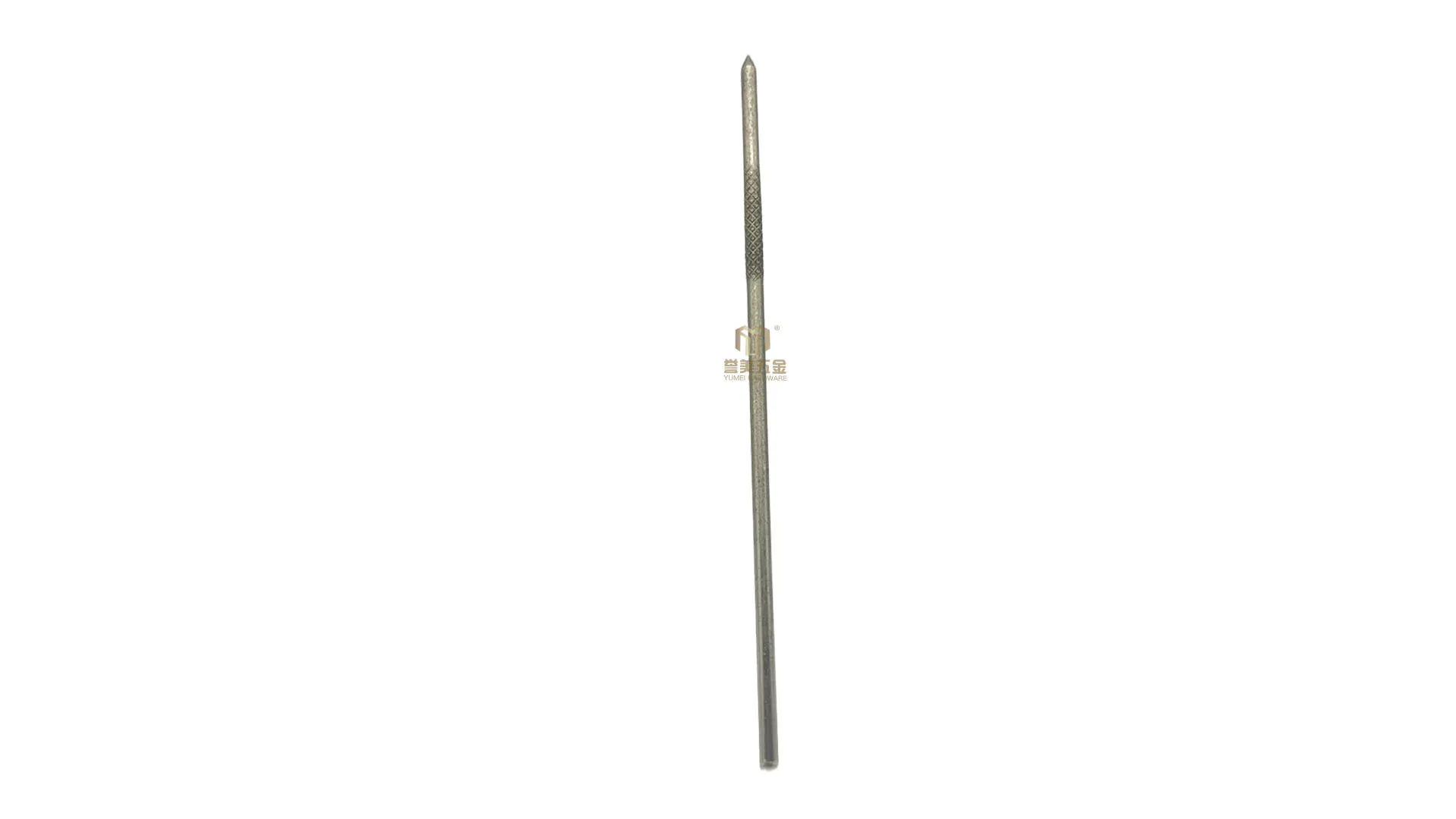
A set of 10 Titanium-Coated Carbide Engraving and Milling Cutters, featuring a size range of 0.8 to 3 millimeters, equipped with a 1/8-inch shank designed specifically for YEEZUGO s Dremel-compatible rotary tools.
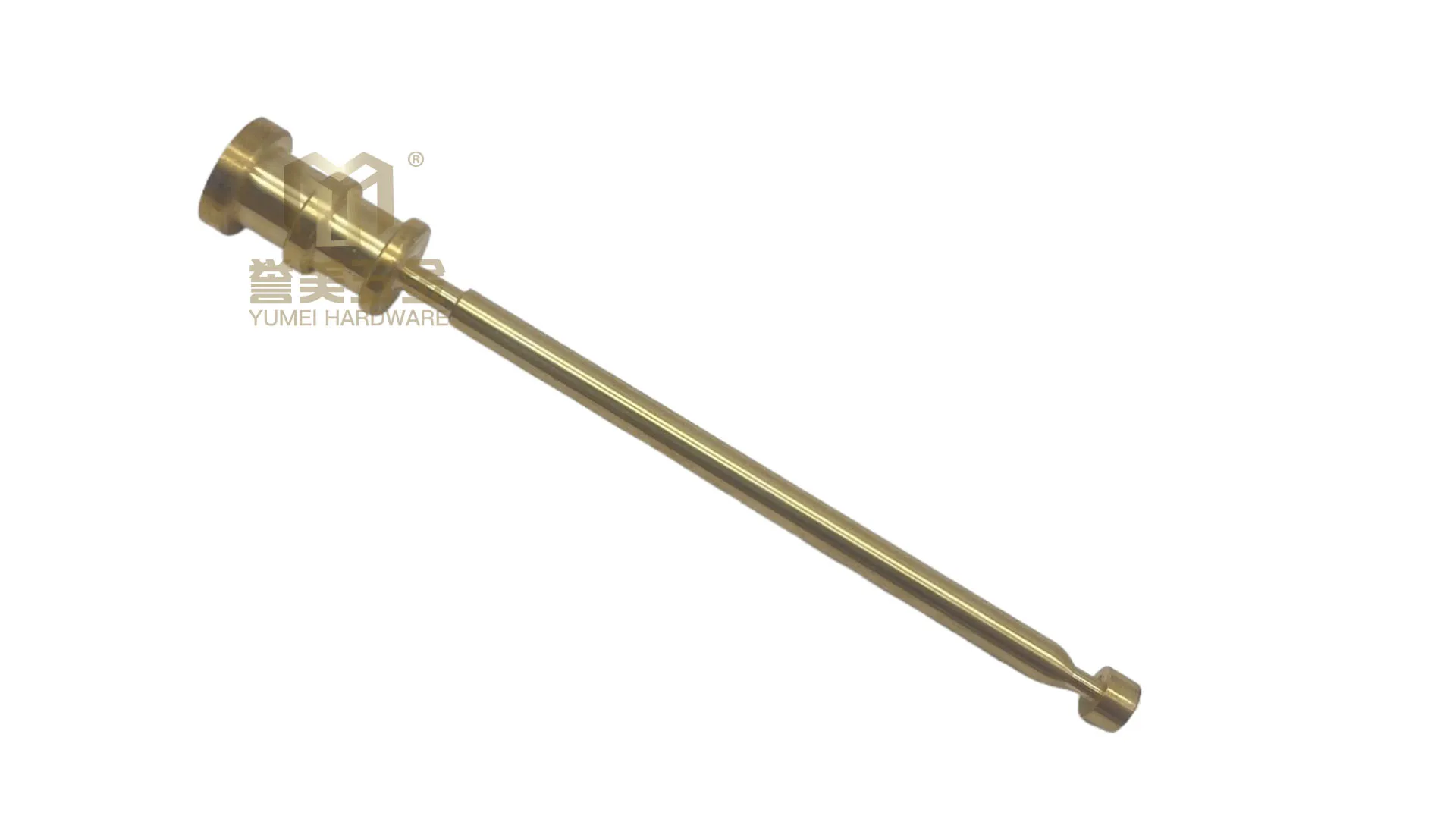
A Comprehensive Set of 5 Premium Hardened Metal Flute End Mills, Each Measuring 2.5x7x4x50mm, Comprising of Carbide Tungsten Construction for Versatile CNC Applications in Steel, Wood, Metal, Plastic, and Beyond.
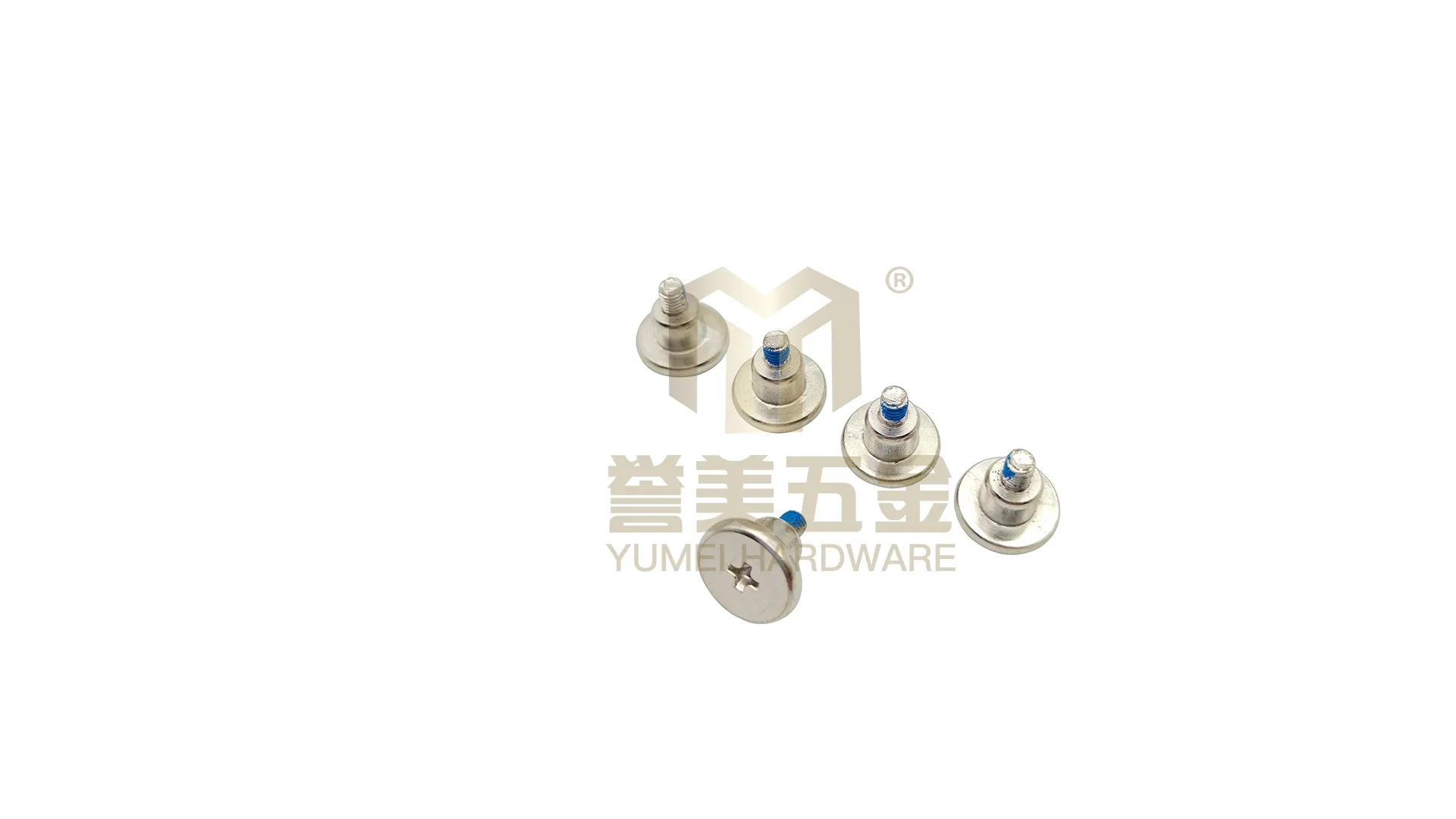
The SpeTool 12411 model presents a 4-Fluted Carbide CNC End Mill designed with a Square Nose profile, boasting a shank diameter of 1/4 inch and an overall length of 3 inches. This Upcut CNC Router Bit comes equipped with a coated surface for enhanced perf
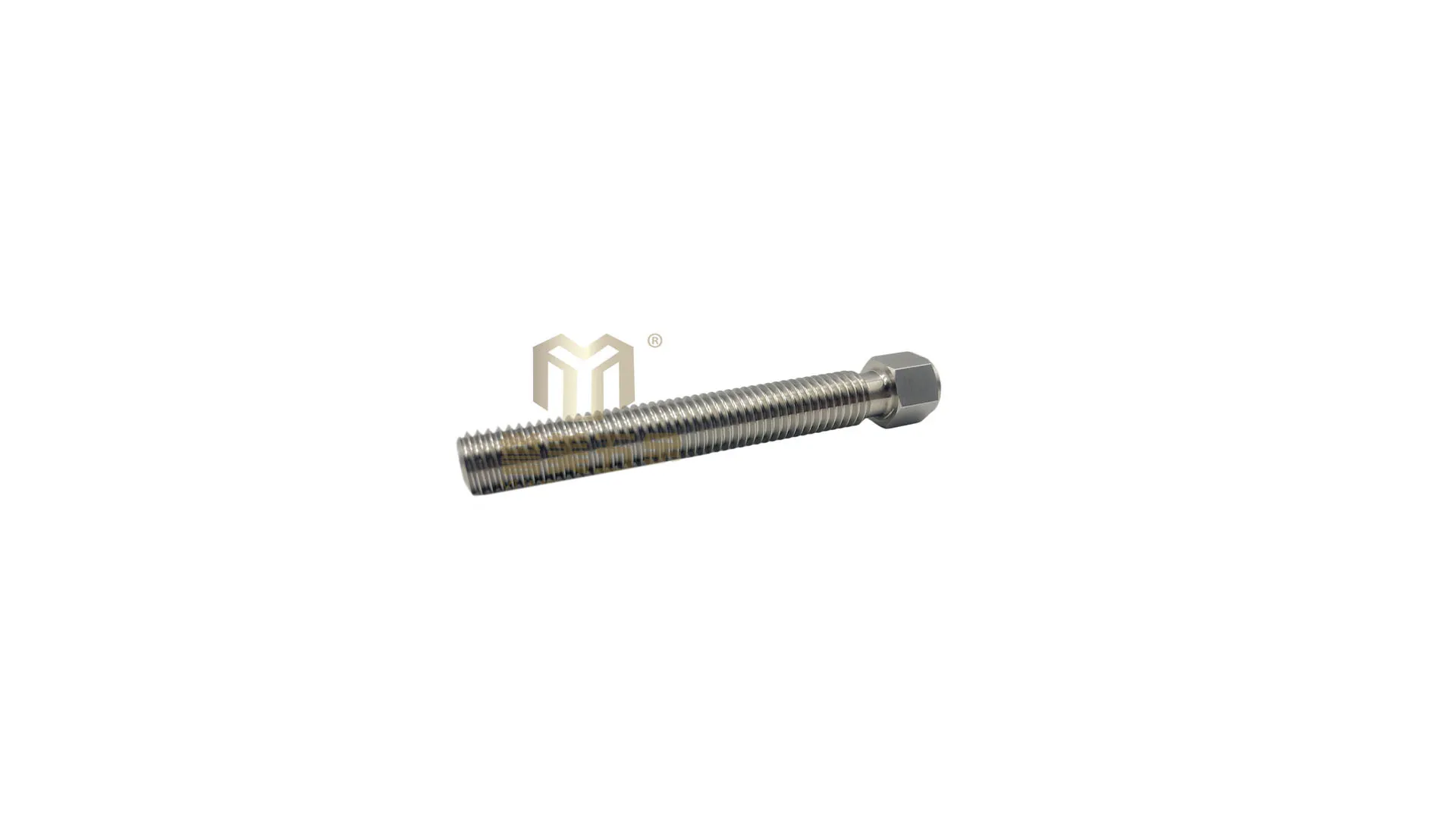
The CNC Router Bit, featuring a 6mm Diameter End Mill, boasts a 42mm Cutting Capability and extends to a Length of 70mm. Crafted from Titanium Plated High Speed Steel, it incorporates a Single Spiral Flute Design for Upcut Milling Operations...
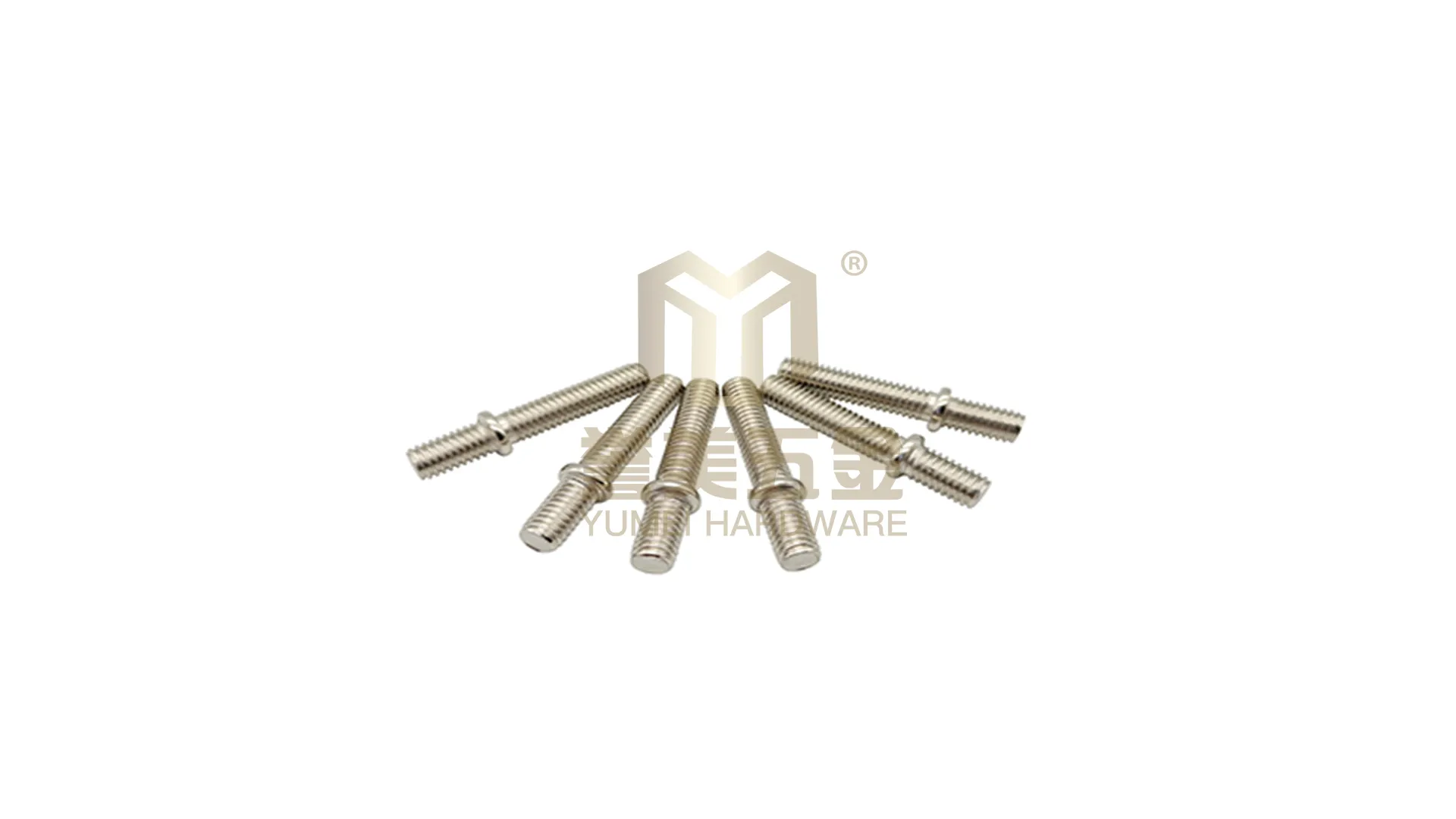
The SpeTool offering comprises a set of 5 premium 2-fluted, flat-nosed carbide end mills, featuring a precise 1/16 cutting diameter. Designed for upcut routing operations, these router bits sport a 1/8 inch shank, making them ideally suited for use in CN
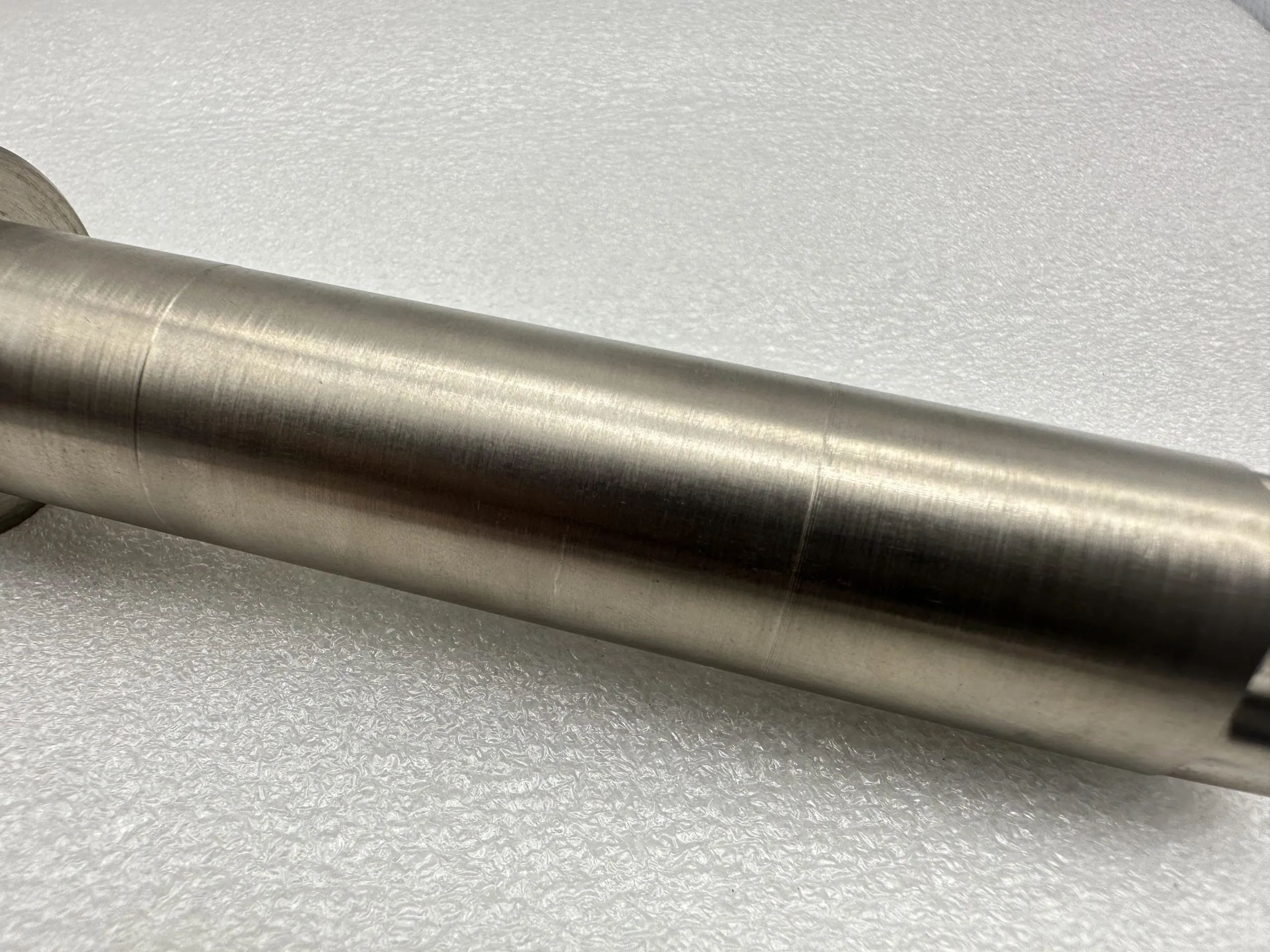
T-Slot Milling Tool, Featuring 4 Flutes, 0.24 Diameter, and a Cutting Depth of 0.04 , Crafted from Solid Carbide with Titanium Coating for CNC Straight Milling Applications - (Suitable For...

The SpeTool assortment of 5 pieces features 4-fluted ball-nosed router bits, designed with a precise 1/8 cutting diameter for milling applications. Crafted to endure rigorous use, they boast a hardness rating of HRC55 and incorporate a 1/8 shank. These
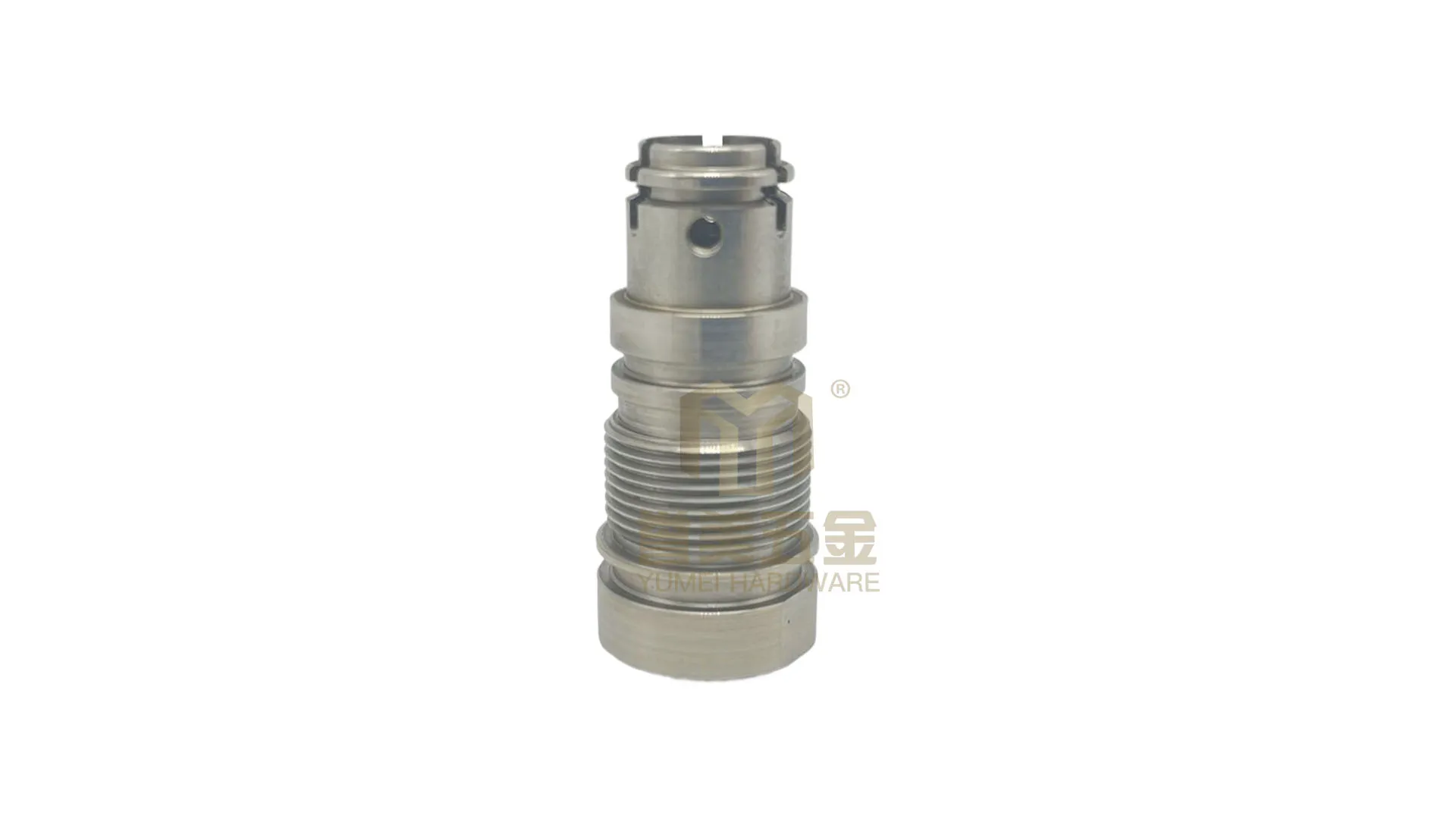
Sophisticated Precision-Crafted Titanium Tweezers, Expertly Engineered via CNC Technology, Boasting Accurate Tips & Endowed with Anti-Static & Anti-Corrosion Properties for Unparalleled Safety in Industrial Applications...
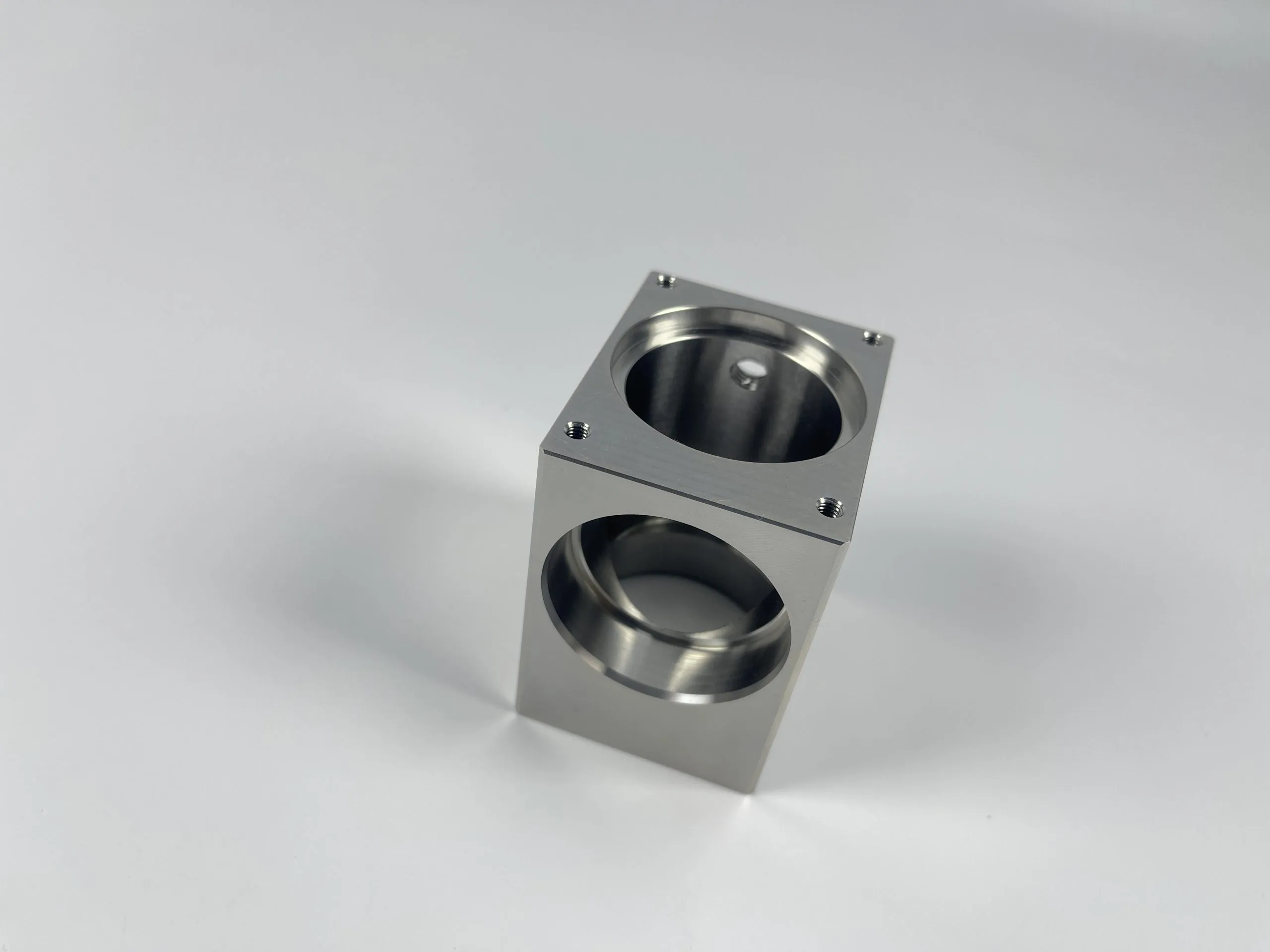
Rectangular-Tipped End Milling Tool featuring a 4mm Shank, 1mm x 6mm Dimensions, Encased in Titanium Coating, Crafted from Solid Carbide with an Extended Reach Neck and Four Flutes, Ideal for CNC Router Milling Operations...
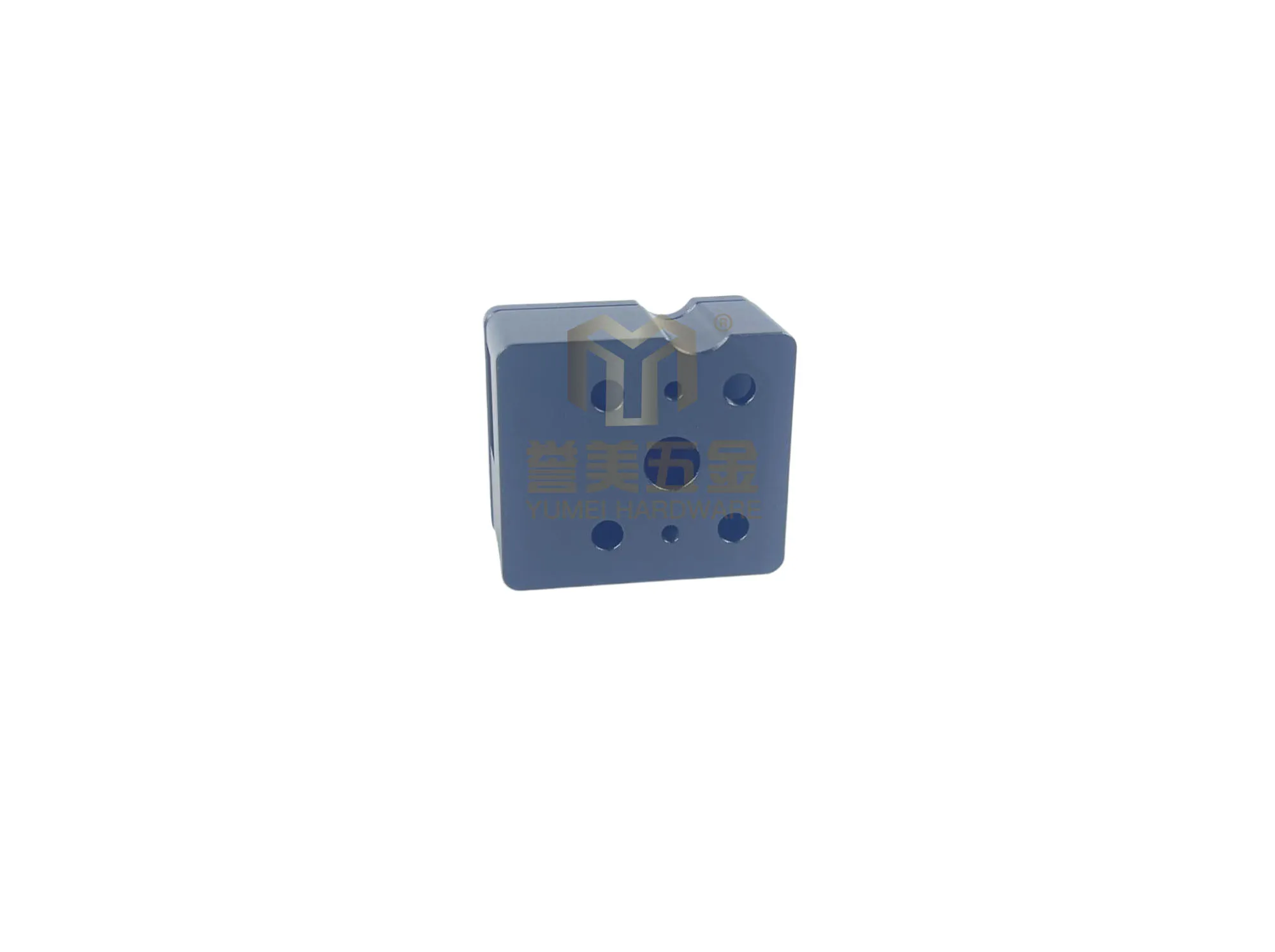
T-slot Profiled End Mill, Featuring 4-Flute Design with 0.12 Diameter and a 0.02 Cut Depth, Constructed from Solid Carbide and Enhanced with Titanium Coating for CNC Straight Milling Applications - (Applicable for...
People May Ask
The conventional threshold for the minimum web or recessed surface depth in precision-machined titanium alloy components, particularly those utilized in aircraft spars, stood at 0.100 inches, barring the utilization of costly supplementary tools that could sustain the typical tolerance range of ±0.010 inches for thinner recessed surfaces. Alternatively, chemical milling methods were often employed to achieve the desired thinness.
Regarding the rigidity and ease of processing in pure titanium variants, we commence with Ti-99.5, categorized as grade 1, which exhibits a firmness level of 100 on the HRC scale and a processability rating of 46%. Progressing to Ti-99.6, designated as grade 2, it demonstrates a reduced hardness of 90 HRC and a marginally lower machinability at 40%. Lastly, Ti-99.7, classified as grade 3, boasts a further diminished hardness of 80 HRC accompanied by a decreased machinability of 35%.
Regarding machinability, aluminum's reduced mass and inherent softer texture facilitate machining processes compared to titanium. Nevertheless, titanium's remarkable resistance to corrosion far surpasses that of aluminum, rendering it a preferable material for applications that encounter severe environmental conditions. 19th October, 2023
Advice on machinery selection for titanium processing
Additionally, maintaining a low RPM range, oftentimes, a setting of 3000 RPM suffices, considering the employment of carbide cutting tools that necessitate a slow cutting velocity, ranging from 45 to 100 meters per minute. The utilization of internal coolant is imperative, and its efficacy enhances with increased levels.
Techniques such as water jetting, band sawing, laser-based slicing, and plasma cutting are all viable options for achieving precise and productive titanium cutting operations.
The prevalent choice for laser cutting titanium sheets typically involves utilizing CO2-based machinery, with nitrogen or oxygen serving as auxiliary gases to facilitate the process.
The processing of titanium alloys poses significant challenges, stemming from their inherently elevated tensile strength, diminished ductile yielding capacity, a modulus of elasticity that is approximately 50% less (at 104 GPa), and a thermal conductivity markedly lower by roughly 80% compared to steel.
When it comes to machining titanium, the optimal choice of tooling lies in carbide-tipped instruments endowed with a PVD coating. Furthermore, advancements in technology have introduced novel, enhanced coating alternatives, notably TiAIN (Titanium Aluminum Nitride), which offer additional benefits. Given titanium's inherent resilience and springiness, the utilization of a keenly sharpened tool becomes paramount to achieving efficient and precise cutting operations.
Titanium Machining Strategies
Maintain Low Temperatures. As titanium exhibits poor heat conductivity, a substantial portion of the energy generated during machining accumulates in the cutting tool. ...
Ensure Surface Stability. ...
Monitor Tool Condition. ...
Allow Adequate Tool Clearance. ...
Minimize Adhesion Issues. ...
Manage Chipping Effectively.
Posted on
This material possesses weldability (under an inert environment) and is amenable to CNC machining, akin to stainless steel. Furthermore, it favorably responds to a wide array of surface finishing techniques: from bead blasting and powder coating to electrophoresis, all these processes yield satisfactory outcomes when executed on titanium. 24th November, 2020