threaded stud – Yumei Precision
China Top Supply: Aluminum CNC Machining And Aluminum Prototype Machining Services | Yumei Hardware
China Top Supply: Aluminum CNC Machining and Aluminum Prototype Machining Services
At the forefront of China's manufacturing excellence, "China Top Supply" stands as a leading provider of Aluminum CNC Machining and Aluminum Prototype Machining Services. Our commitment to precision and innovation has established us as a top supplier, offering services that are second to none in the realm of aluminum machining.
Understanding Aluminum Machining Service
Aluminum Machining Service is a specialized field that requires a deep understanding of material properties and cutting-edge technology. Aluminum, known for its lightweight and high strength-to-weight ratio, is a material of choice in various industries.we offer comprehensive aluminum machining services that encompass milling, turning, drilling, and tapping, among others. Our expertise lies in working with a range of aluminum alloys, each with unique characteristics that we leverage to deliver components with optimal performance.
The process of aluminum machining service involves several critical steps, including material selection, design consultation, and the application of appropriate cutting tools and techniques. Our state-of-the-art CNC machines are programmed to execute complex toolpaths with precision, ensuring that each aluminum component is produced to the exacting specifications of our clients.
The Precision of Aluminum CNC Machining
Aluminum CNC Machining is a subset of our aluminum machining service that specifically utilizes computer numerical control (CNC) technology. This advanced method of manufacturing allows for the automation of complex machining processes, resulting in increased efficiency and accuracy. In aluminum CNC machining, we program our machines to follow detailed instructions that dictate the movement of cutting tools, enabling us to create parts with complex geometries and high dimensional accuracy.
The precision of aluminum CNC machining is crucial in applications where components must fit together seamlessly or operate under strict tolerances. Our aluminum CNC machining service is capable of producing parts with surface finishes that are smooth and free from defects, which is essential for applications in the aerospace, automotive, and medical industries.
The Versatility of Aluminum Prototype Machining
Aluminum Prototype Machining is a vital service in the product development cycle. It allows designers and engineers to create functional models that can be tested for performance, fit, and form. our aluminum prototype machining service is designed to provide rapid turnaround times, enabling clients to iterate their designs quickly and cost-effectively.
The versatility of aluminum prototype machining is evident in its ability to produce prototypes that closely resemble the final product in terms of material properties and performance. This is particularly important for testing the durability and functionality of components under real-world conditions.
Professional Insights into Aluminum Machining Services
Material Properties: Understanding the thermal conductivity, machinability, and strength of different aluminum alloys is crucial for optimizing the aluminum machining service process.
Cutting Tools: The selection of cutting tools for aluminum machining service is based on the alloy's hardness and the desired surface finish. High-speed steel, carbide, and diamond tools are commonly used.
Coolant Use: In aluminum CNC machining, the use of coolants is essential to dissipate heat, prevent tool wear, and extend tool life.
Surface Finish: The surface finish in aluminum machining service is often specified by the client and can range from rough to mirror-like, depending on the application.
Tolerance Control: Achieving tight tolerances in aluminum CNC machining requires precise machine setup, high-quality cutting tools, and meticulous quality control.
Post-Machining Processes: After aluminum prototype machining, components may undergo additional processes such as anodizing, painting, or heat treatment to achieve the desired properties.
The Benefits of Choosing China Top Supply for Aluminum Machining Services
When it comes to aluminum CNC machining and aluminum prototype machining, there are several benefits to choosing China Top Supply as your partner:
Precision and Quality: Our aluminum CNC machining service is known for its precision and quality, ensuring that each component meets the highest standards.
Rapid Prototyping: Our aluminum prototype machining service allows for quick turnaround times, getting your designs from concept to reality faster.
Cost-Effectiveness: By leveraging our expertise and efficient processes, we can offer competitive pricing without sacrificing quality.
Versatility: We cater to a wide range of industries, from aerospace to consumer electronics, providing tailored aluminum CNC machining and aluminum prototype machining solutions.
Customer Satisfaction: Our commitment to customer satisfaction is unwavering, ensuring that your needs are met and your expectations are exceeded.
Frequently Asked Questions about Aluminum Prototype Machining
Q: What makes aluminum prototype machining so important in product development?
A: Aluminum prototype machining is crucial as it allows designers and engineers to create tangible models of their designs. These prototypes can be used for testing, market research, and refinement, leading to better final products.
Q: How does China Top Supply ensure the quality of aluminum prototype machining?
A: We ensure quality through rigorous quality control measures, skilled operators, and the use of advanced CNC machinery. This combination guarantees that each aluminum prototype is machined to the highest standards.
Q: What are the advantages of using aluminum for prototype machining?
A: Aluminum is lightweight, strong, and easy to machine, making it an ideal material for prototypes. Its versatility also allows for a wide range of applications and design possibilities.
Q: How does China Top Supply handle complex aluminum prototype machining projects?
A: We tackle complex projects by leveraging our experienced team and advanced technology. Our ability to handle intricate designs and tight tolerances sets us apart in the aluminum prototype machining field.
Q: What kind of support does China Top Supply offer during the aluminum prototype machining process?
A: We offer comprehensive support, from design consultation to post-machining services. Our goal is to be a collaborative partner throughout the entire process, ensuring that your aluminum prototype meets your vision and requirements.
is committed to delivering the highest standards in aluminum machining service and aluminum CNC machining. Our expertise in aluminum prototype machining further solidifies our position as a one-stop solution for all aluminum machining needs. We pride ourselves on our ability to meet the unique challenges posed by each project, ensuring that our clients receive components and prototypes that exceed their expectations. Trust China Top Supply for your aluminum machining requirements, and experience the difference that precision, quality, and professionalism can make.
Established in 2010, Yumei, a China-based manufacturer, has grown to become a prominent supplier of high quality CNC machining services. Our factory in Dongguan is equipped with state-of-the-art machinery, enabling us to produce a diverse range of metal cnc machining parts. with a global reach extending to countries like Germany and France, we aim to be the go-to manufacturer for all precision fabrication needs, striving to exceed customer expectations worldwide.
Hot Products
Aluminum Cnc Machining Products
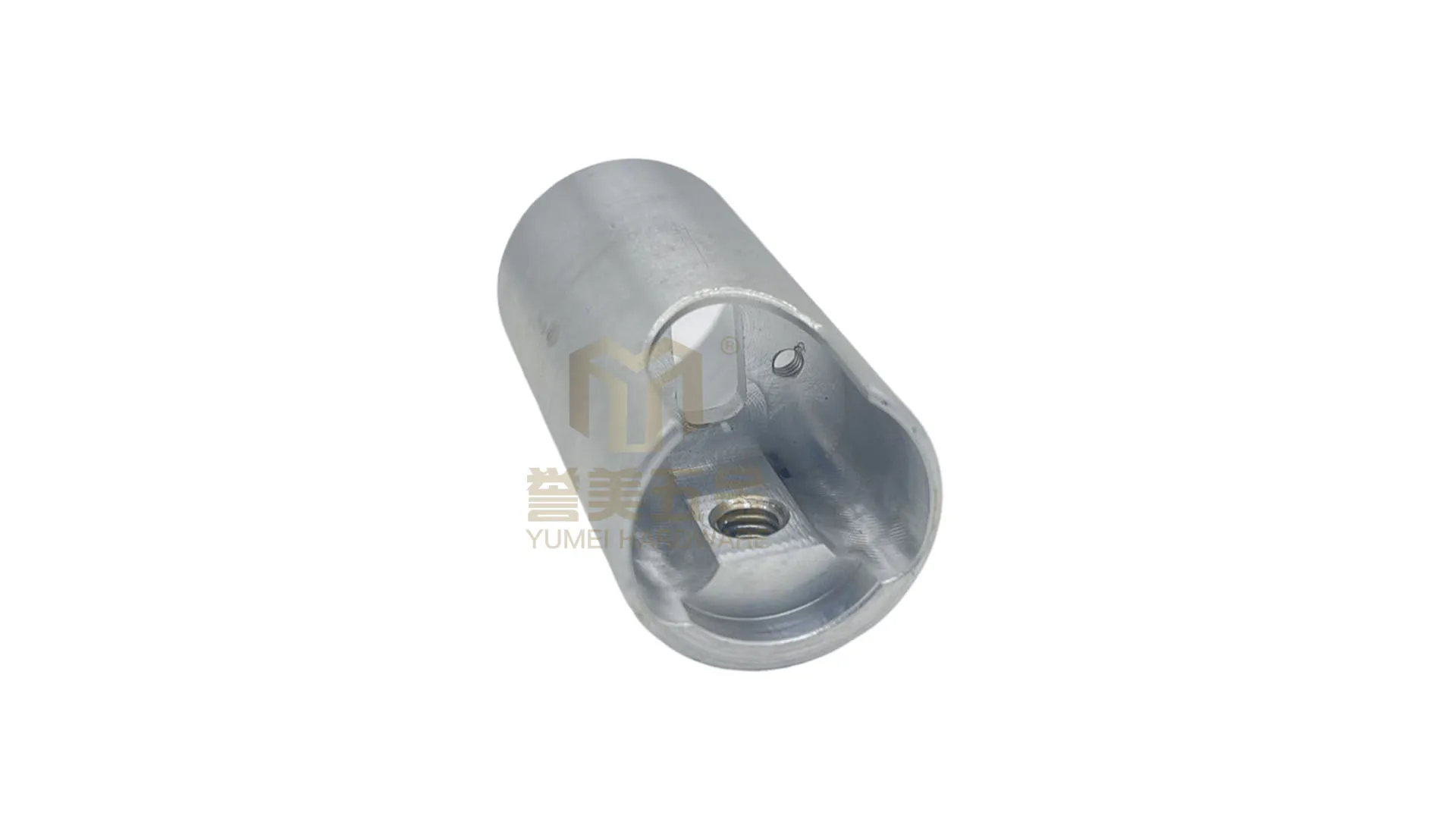
Drill Bits Sets for Professionals: SPEED TIGER Solid Carbide CNC Spiral O Single Flute End Mill - IAP1/4 Diameter 1/4 Shank 2 OVL(1 Piece, 1/4 ) - for Aluminum, Wood, Plastic, Brass, Copper Cutting
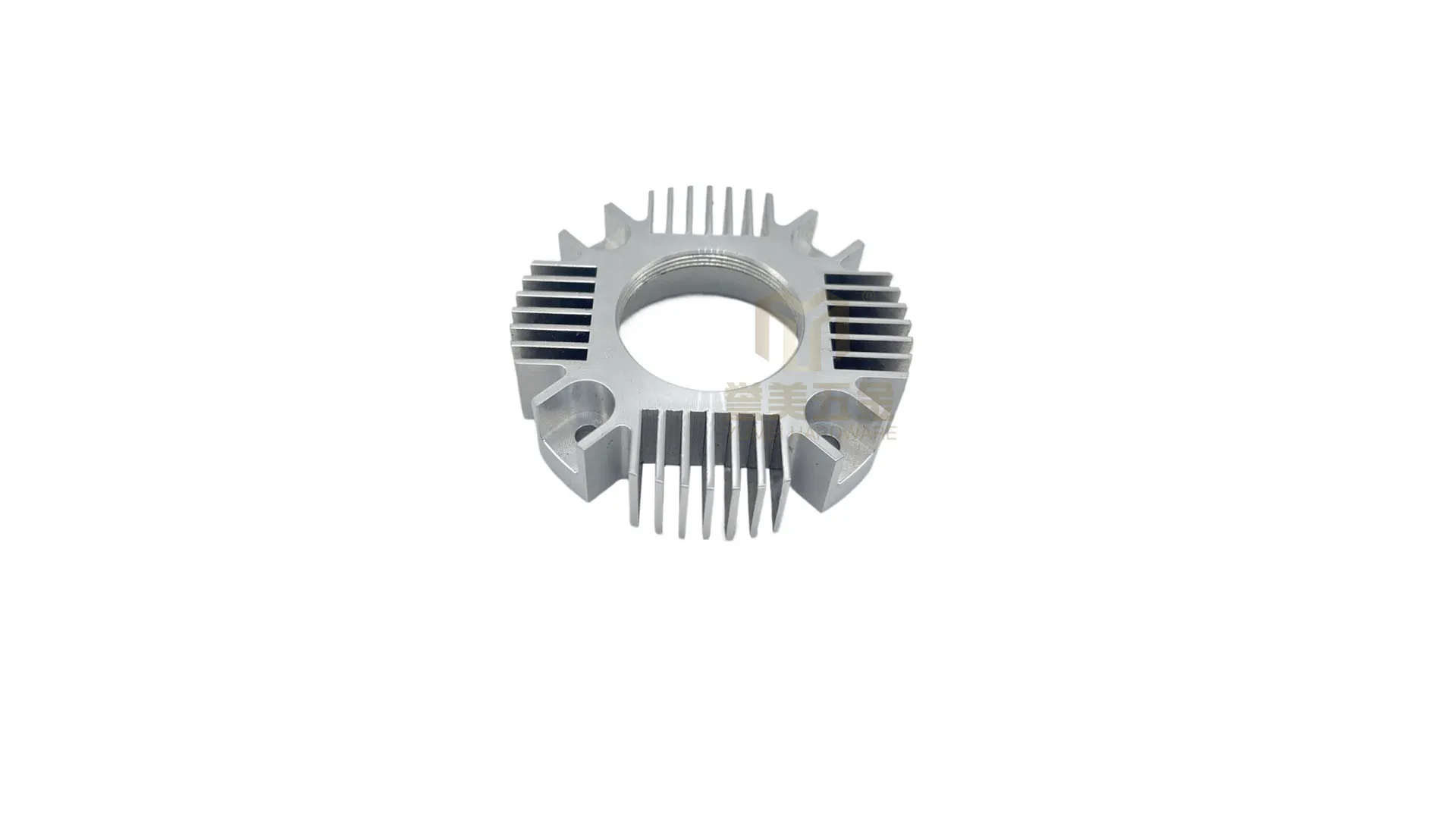
SpeTool 1.5-inch-long 1/8-inch End Mills for Aluminum with 3 Flutes CNC Spiral Router Bits for Non-Ferrous Metal Upcut
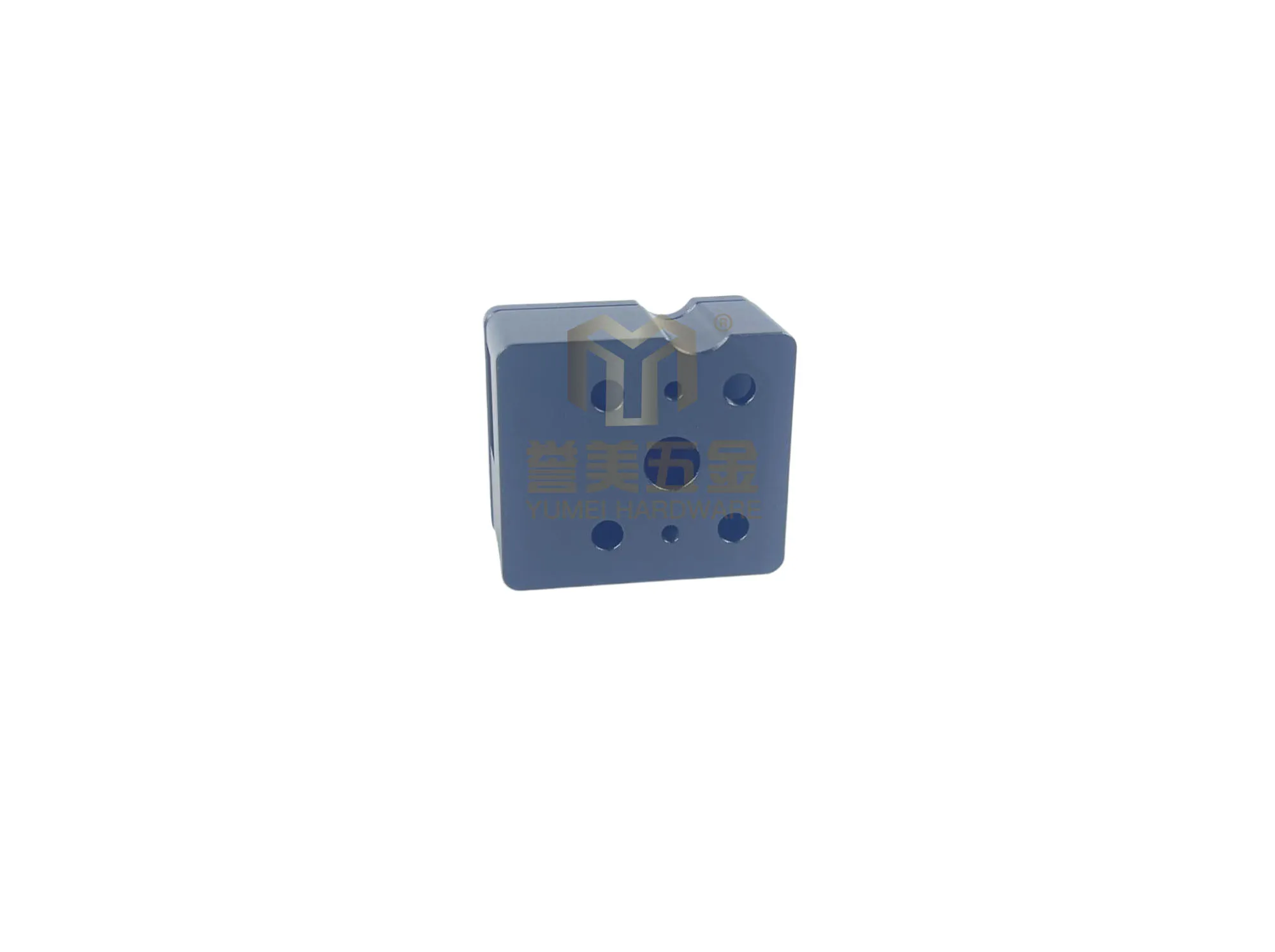
Inch Shank, 1/8 CD x 1/2 CL x 1/4 SD x 2 OL, DashHound BRO02 Carbide O Single Flute Plastic Cutting Spiral Bit CNC Router Bit End Mill Aluminum Milling Cutter
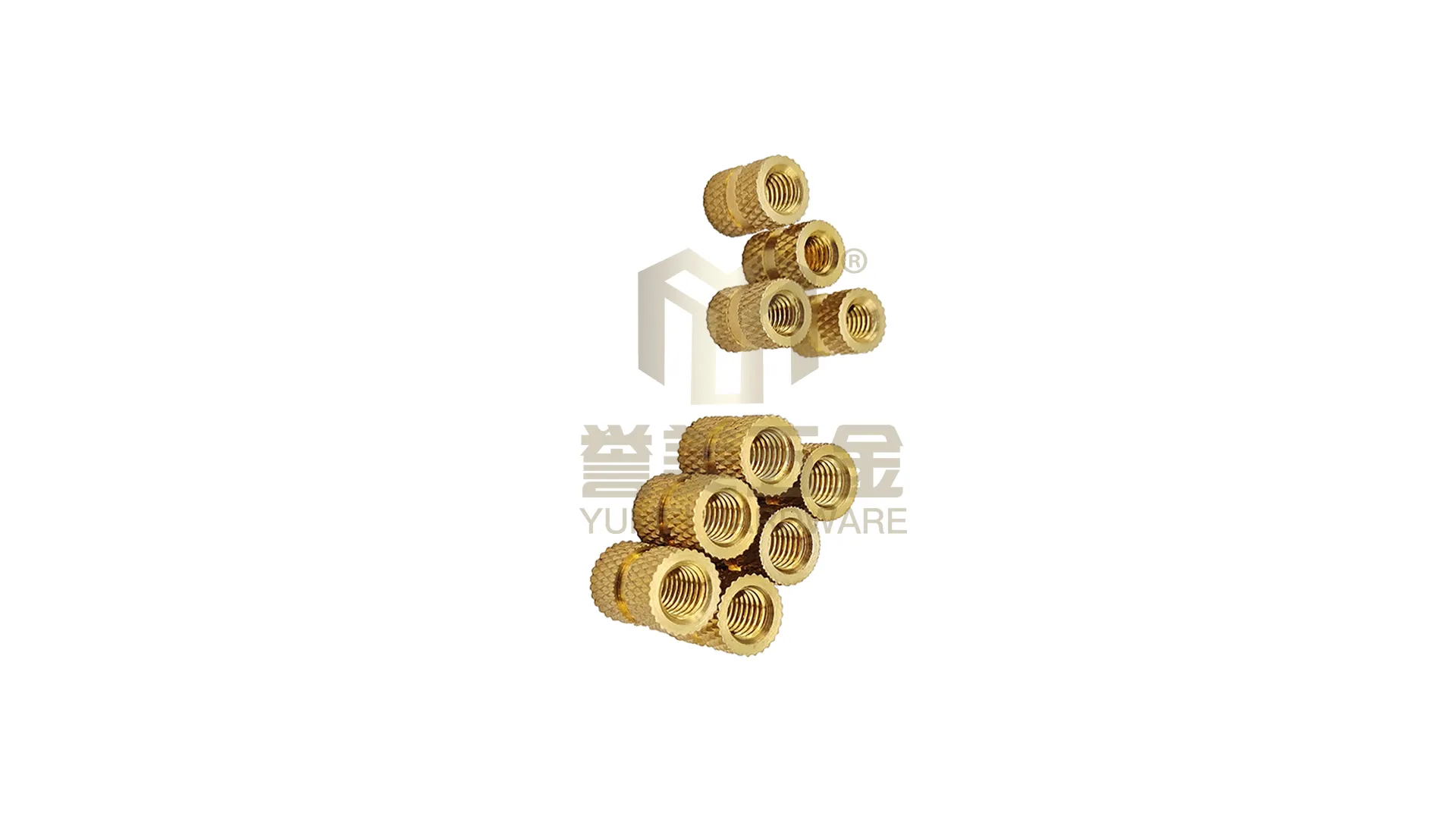
SpeTool 3 Flutes CNC Spiral Router Bit for Aluminum Cut Non-Ferrous Metal Upcut, 1/4 End Mill Size: 2.5 inches
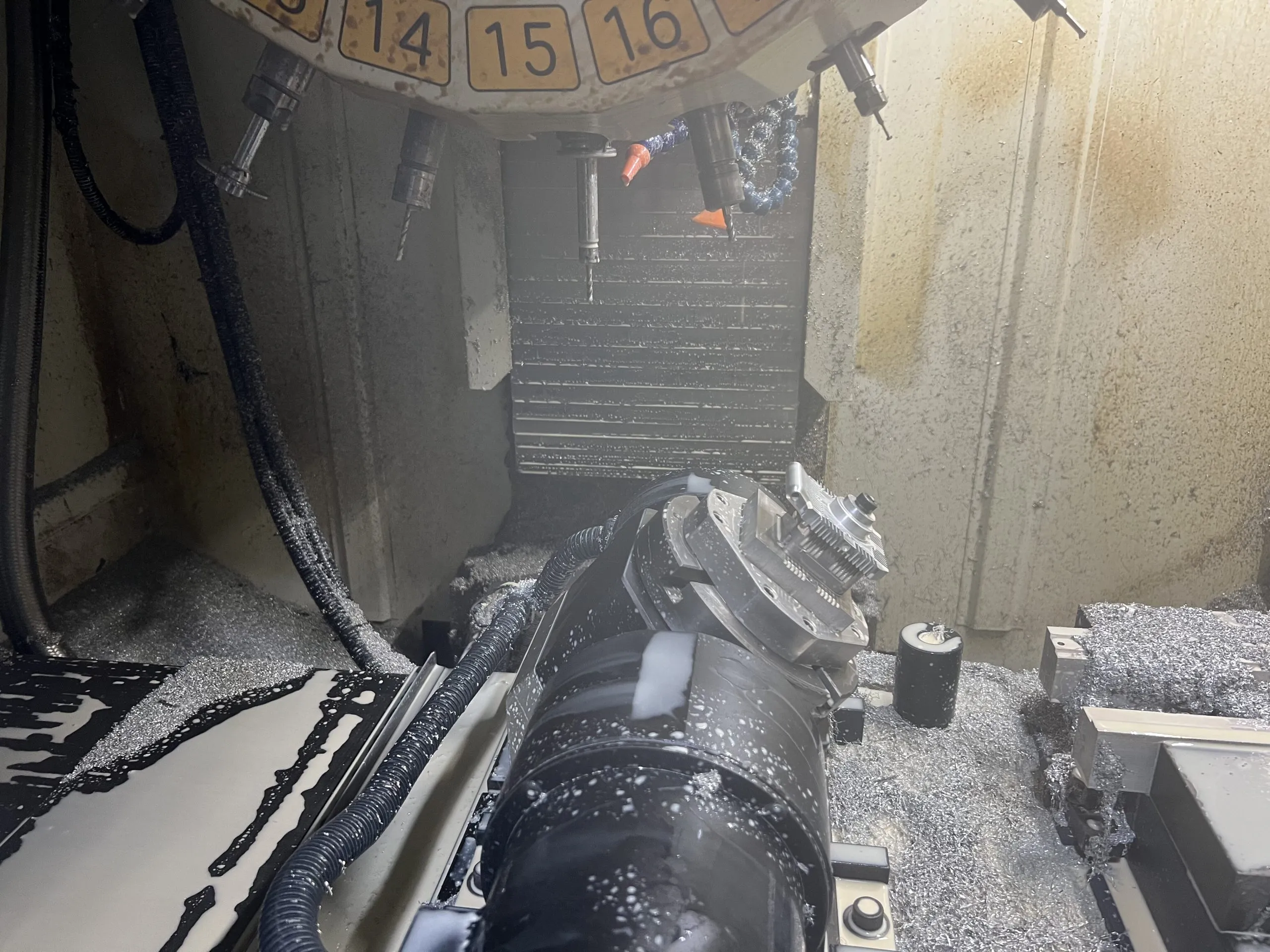
SpeTool 3 Flutes CNC Spiral Router Bit for Aluminum Cut Non-Ferrous Metal Upcut, 1/4 End Mill 5 Pieces, 2.5 inches Long
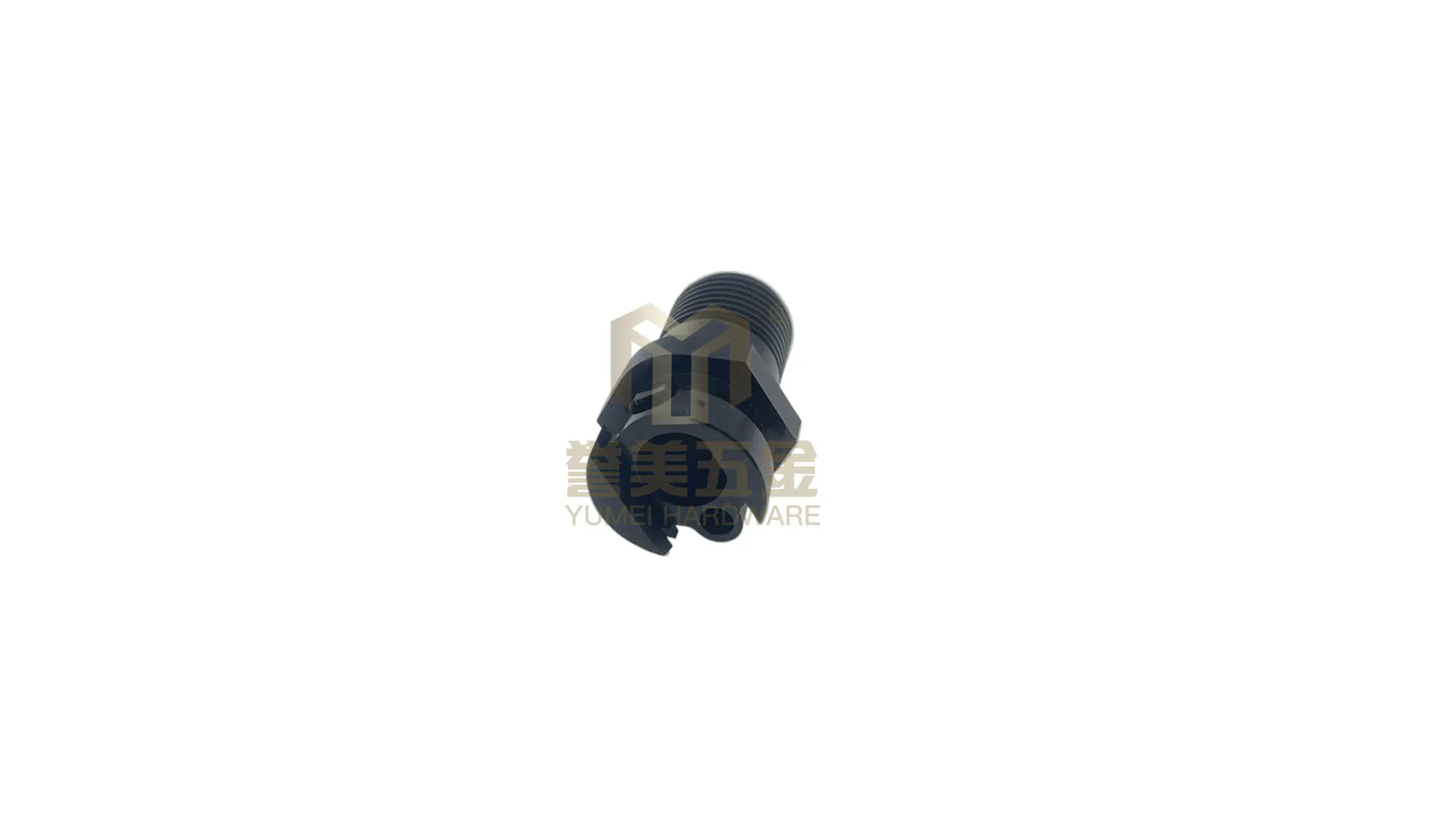
5 Spetools Aluminum End Mills 1/8 inch CNC Spiral Router Bits with 2 Flutes Non-Ferrous Metal Upcut for Woodworking Cutting, 1-1/2 inches long
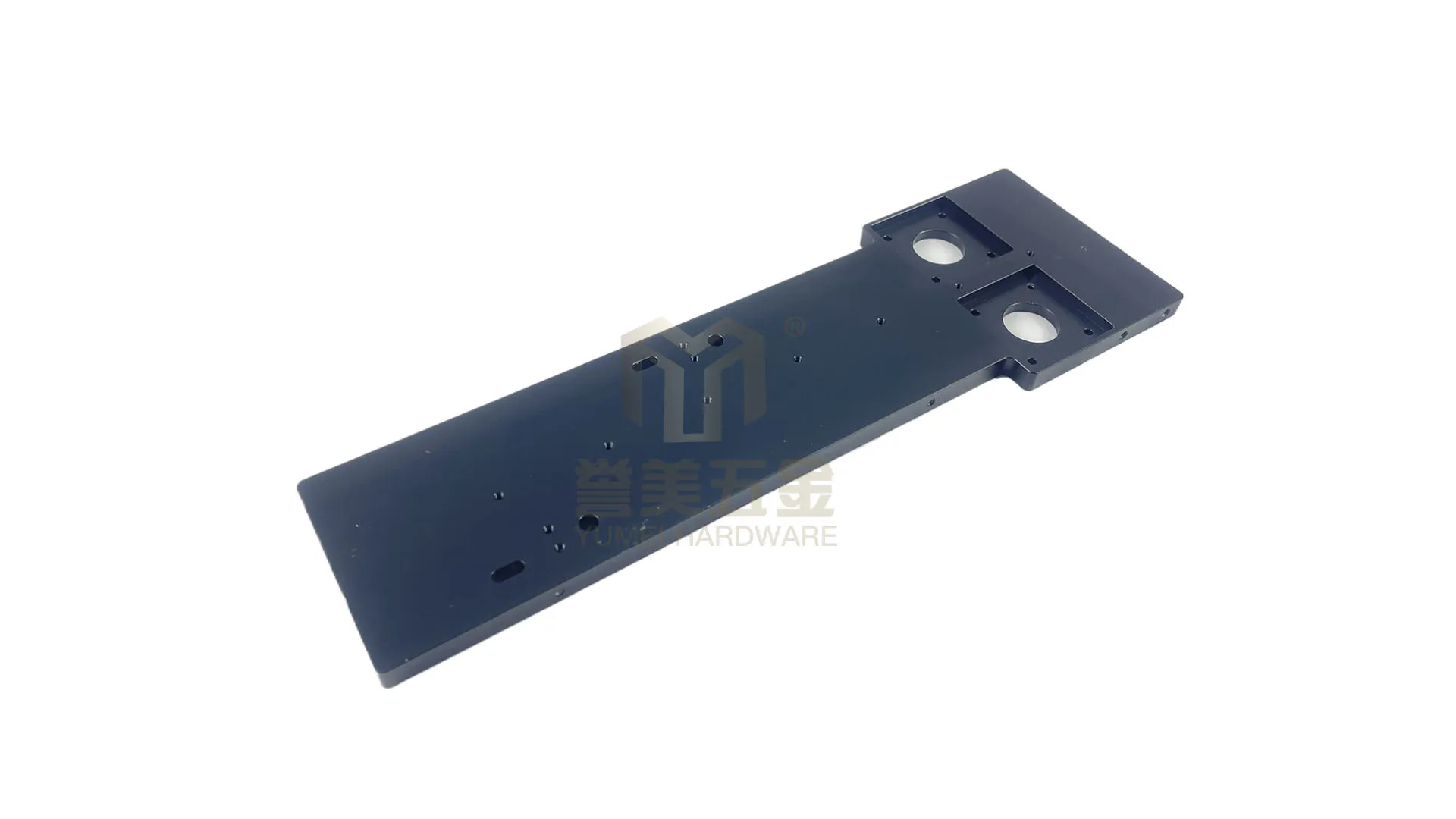
3/8-inch shank, extra-long 3.5-inch SpeTool 3 Flute Carbide End Mill for Aluminum Cut Non-Ferrous Metal Upcut CNC Spiral Router Bit
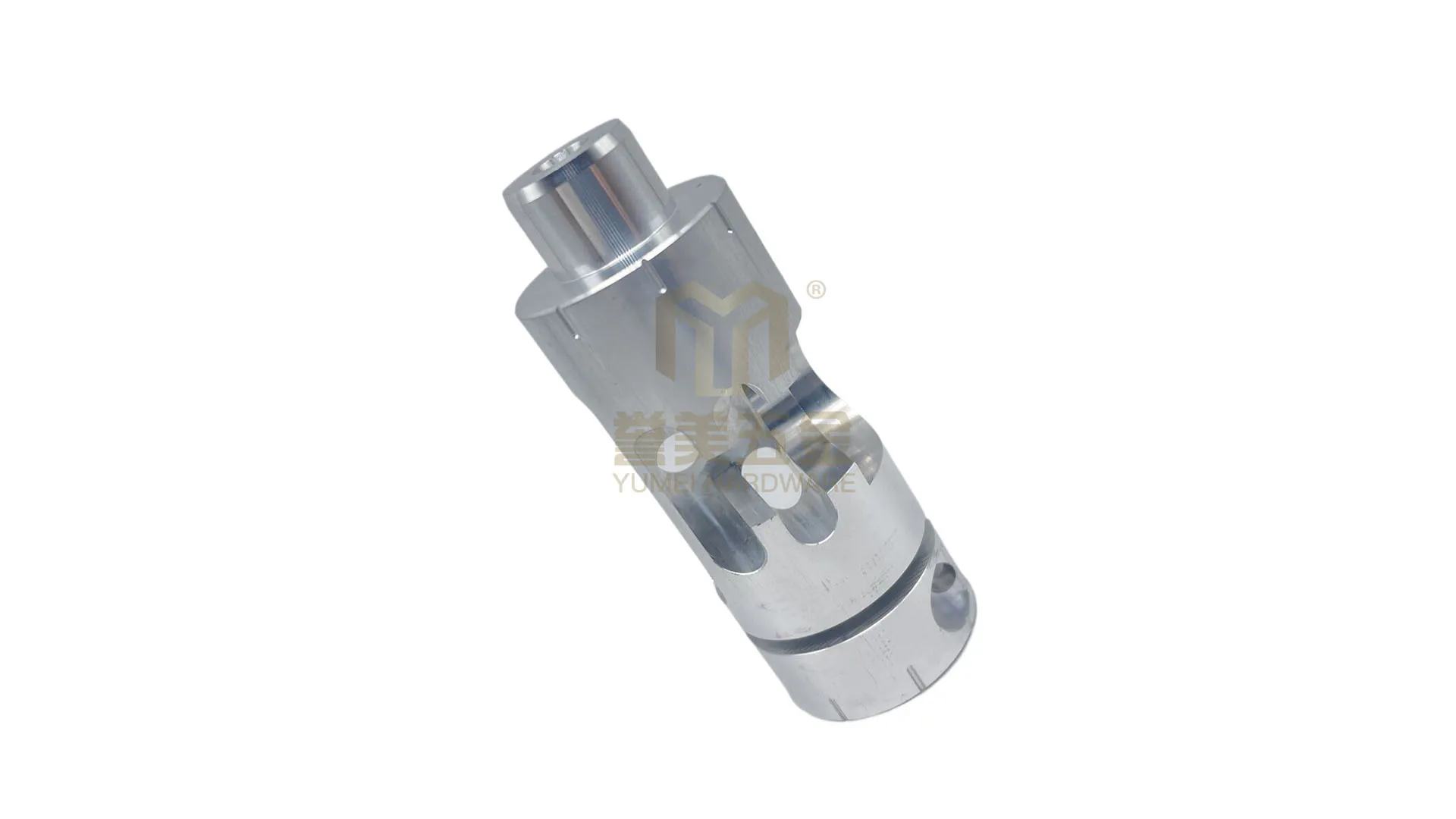
Steel gauge block set, 81 pieces, grade B, Accusize Industrial Tools P900-S581
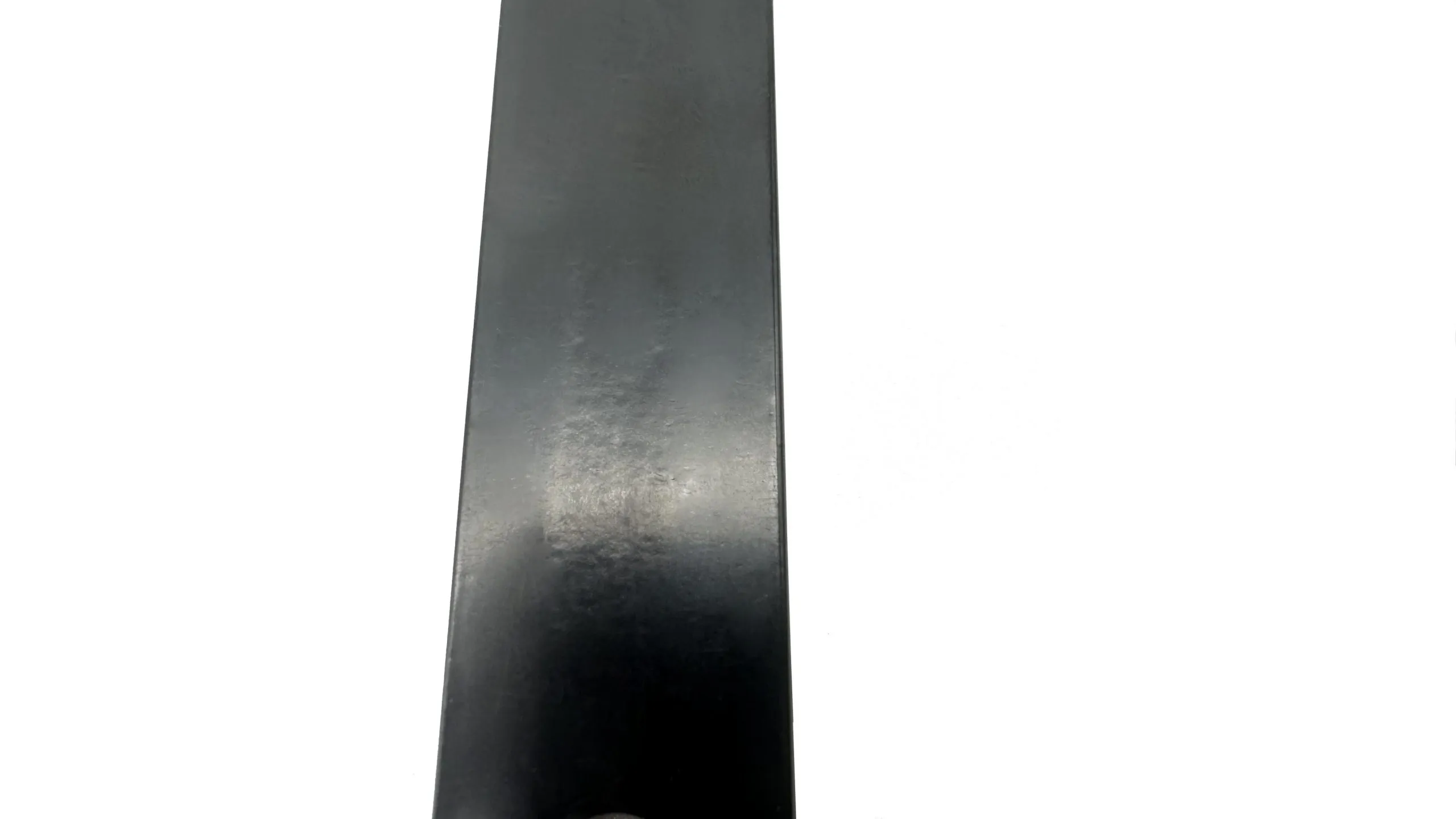
Set of 10 Double Cut Carbide Rotary Burrs Tungsten Steel for Woodworking, Drilling, Metal Carving, Engraving, and Polishing, 1/8 Shank, 1/4 Head Length
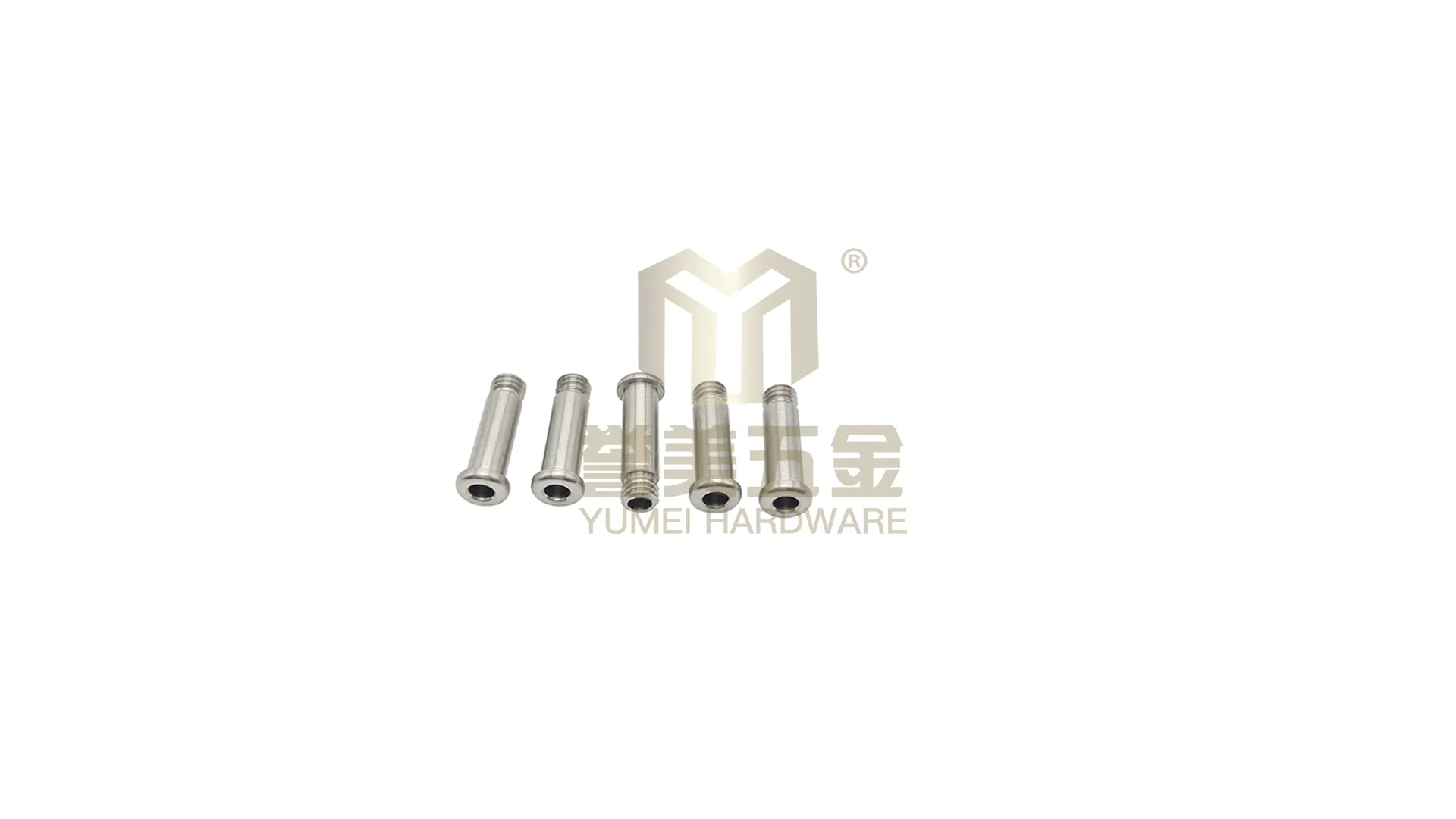
Wood Aluminum Steel Titanium 10 Pieces 4-Flute End Mill Bits, AFUNTA 0.08 - 0.47 HSS CNC Straight Shank Drill Bits Cutter Tool Set
Top Reviews
Whoa. This book was fantastic. Simple to read and comprehend, it includes everything from choosing a solar power installation to designing and planning a suitable installation, locating the necessary parts and equipment, knowing where to locate expert assistance if necessary, and much more. I looked into solar power for a while since I wanted to live in an RV full-time, but the information was so complicated. This book is a great resource because it clarifies everything. This book is essential reading even if you want to hire professionals to complete the installation for you. It will help you make the proper choice and ensure that they are completing the job correctly.
Using my X-carve CNC router, I use this bit to cut aluminum (dry cutting; no coolant or lubricant). I have not found anything that cuts as quickly or lasts as long for cutting pieces out dry, so I heartily suggest it. It performs admirably on plexiglass and acrylic as well. The only thing I have to complain about is how poorly the single flute cuts tiny holes for fastening. Their typical shape is somewhat oblong. Despite this, I rate the product five stars for cutting quality. I use a two-fluid Kodiak end mill when I need nice holes, but it cuts considerably more slowly and jams up more easily.
I purchased these burrs with the expectation that they would last me no more than a few uses—I mean, just look at the price! I've used the burr set on wood, aluminum, brass, copper, mild steel, spring steel, and 1095 high carbon knife steel since I received it back in 2020, and to my surprise, all but two of them still function. I vacuumed up one that was never seen again and bent one the first week due to overuse of force. I frequently see people whining about being bent. There are several reasons for this. The bit was too far out from the rotary tool. - using the instrument too firmly. (Don't force the tool; let it do the work) – the bit made contact with the hard substance on both sides, binding it. - The rotary tool vibrates because it is unbalanced and is junk. A few things to remember: always wear proper eye protection when using these parts. I was wearing some inexpensive spectacles when I was careless and caught a bit of metal that had gotten under them. Not to mention, the chips these burrs shoot skyward are extremely hot and sharp. So use caution.
People May Ask
Negative aspects of ECMThe biggest drawback is expense; compared to more traditional machining methods, ECM requires expensive equipment and specialized training, both of which add up quickly.
While both ECG and ECM use electrochemistry to dissolve metal, the key distinction between them is in the tools they use. Whereas ECG uses a revolving abrasive wheel, ECM uses a tool that is fashioned as the opposite of the required geometry.
Both EDM and ECM are non-traditional machining techniques, yet there are significant distinctions between the two. While ECM, or electrochemical machining, uses electrolysis to dissolve the metal locally, EDM, or electrical discharge machining, depends on localized spark erosion to remove material.
. One metal that is incredibly simple to work with is aluminum. It is very strong, recyclable, and simple to cut through. One metal that many owners of CNC machines choose to work with is aluminum.
Which Materials Are Acceptable for a CNC Machine?
Metals: These include steel, brass, and aluminum.
Plastics: These include polycarbonate (PC), acrylic (PMMA), acetal (POM), and polypropylene (PP).Wood: Including softwood, plywood, and hardwood.
Foam: Such as stiff foam and carving foam, which tend to be more pliable but strong.
The majority of wrought aluminum alloys are very machinable. Even though machining cast alloys with copper, magnesium, or zinc as the primary alloying elements can be challenging, using short tool rake angles can increase machinability.
As a general guideline, CNC-machined walls should be at least 1/32" (0.794mm) wide. However, depending on a few important factors, the exact number and cost may differ: Wall Height:Thickness Ratio (H:T).
Because it chips easily and may be relatively simple to shape, aluminum is more machinable than certain other metals. "Chipping easily" implies that the material is more "free machining" and that the cutting tool expends more time and effort on the workpiece rather than the chip that it has already produced.
Carbide Tipped Band Saw Blades are also a fantastic option for cutting aluminum since they work well on a variety of abrasive building materials, including cast iron, concrete, graphite, and fiberglass.
An 8 to 10 TPI blade is ideal for aluminum. We believe that MK Mor e and Diablo are by far the best brands of metal-cutting blades. Look for a carbide-tipped blade with at least an 8 TPI if you are cutting cast iron, stainless steel, and high-tensile alloys, as well as for jobs like auto dismantling and fire & re cue.