What plastic is machinable?
There are various plastics can be machined,the following are some common plastic materials suitable for CNC machining.
For example,ABS,PC,PMMA,POM,PA,PTFE,PEEK,PVC,HDPE,UHMWPE,etc.
Advantages of Precision Machined Plastic Parts
1.Lightweight:plastics are significantly lighter compare with metals, they will be ideal for applications where weight reduction is crucial.
2.Corrosion Resistance:many plastics are naturally resistant to corrosion and can withstand exposure to chemicals, moisture, and harsh environments, on the contrary,metals may get rust or corrosion.
3.Electrical Insulation:plastics are excellent electrical insulators, which makes them suitable for use in electrical and electronic components.
4.Lower Cost:machined plastic parts often have lower material and production costs compared to metal parts, especially for short production runs or prototypes.
5.Ease of Customization:cnc machining allows for the easy customization of plastic parts to meet specific design requirements, including the ability to produce small, intricate features.
Commonly Machined Plastic Materials
Plastic materials | Key Characteristics | Typical Applications | Machining Considerations |
ABS | Machining Considerations | structural parts and prototypes | easy to decompose at high temperature and needs to be pre-dried |
PC | excellent impact strength and transparency | protective and transparent parts | Need to dry well |
PMMA | high transparency | optical applications such as lenses, light covers, and displays | Prevent high temperature decomposition |
POM | good chemical stability and high-temperature resistance | gears, bearings, and sliding parts | Prevent high temperature decomposition,Avoid contact with acidic substances. |
PA | high strength, good toughness and wear resistance | gears, pulleys, and other mechanical parts | Need to dry well,Prevent high temperature decomposition |
PTFE | good chemical stability and high-temperature resistance | seals, insulating materials, and corrosion-resistant parts | need to prevent high temperature from producing toxic gases |
PEEK | High strength,high-temperature resistance and chemical corrosion-resistant | high-performance mechanical parts | Pay attention to tool wear |
PVC | good chemical resistance | pipes, valves, and other chemical equipment | need to prevent high temperature from producing toxic gases |
HDPE | good chemical resistance and low friction coefficient | pipes and mechanical parts. | Thermal expansion rate is large, and warping deformation should be prevented during cooling. |
UHMWPE | low friction coefficient | sliding parts and guide rails | Difficulty in cutting |
Applications for Precision Machined Plastic Parts
1.Medical Devices:Surgical instruments, implantable devices, diagnostic equipment, and prosthetics often use precision-machined plastic parts due to their biocompatibility and sterilization capabilities.
2.Automotive Industry:Lightweight and durable plastic components are used in engine parts, interior trim, gears, and other mechanical systems to reduce weight and improve fuel efficiency.
3.Aerospace Industry:Precision-machined plastic parts are used in aircraft interiors, electrical connectors, and insulation components due to their lightweight nature and resistance to corrosion.
4.Electronics:Plastic parts are used in circuit boards, housings, connectors, insulators, and other electronic components, benefiting from their electrical insulating properties.
5.Industrial Machinery:plastic components such as bearings, bushings, gears, and seals are used in machinery for their low friction and wear resistance.
6.Motorcycle:precision machined plastic parts are widely used in the motorcycle industry due to their versatility, weight-saving properties, and cost-effectiveness.
Considerations for Plastic Machining
- Material properties
Thermal sensitivity: Many plastic materials tend to soften or deform at high temperatures. Processing temperatures are controlled to avoid deformation or melting of the material.
Chemical stability: Some plastics are sensitive to specific chemicals that may affect their final quality.
Mechanical Properties: Understand the strength, rigidity and impact toughness of plastics in order to select appropriate machining parameters and tooling. - Tool selection
Tool material: Use sharp high-speed steel (HSS) or carbide tools. Carbide tools are more wear-resistant and suitable for high-precision machining.
Tool shape: Choose a tool with a positive cutting angle to minimize cutting forces and heat generation. Keep the tool sharp to obtain good surface quality.
Tool wear: Inspect and replace tools regularly to maintain machining performance and avoid defects during machining. - Cutting parameters
Cutting speed: Adjust the cutting speed according to the type of plastic. Lower cutting speeds usually prevent overheating and melting.
Feed rate: A moderate feed rate helps to balance cutting efficiency and surface quality. Too high a feed rate can lead to chipping and surface roughness.
Depth of Cut: Take light cuts to avoid overheating and material distortion. - Cooling and lubrication
Cooling: Use compressed air or lightweight coolant to keep material cool and remove chips. Avoid overusing coolant to prevent smearing or surface defects.
Lubrication: Most plastics are machined with only a small amount of lubrication, but in some cases the use of cutting fluids or lubricants can improve surface quality. - Workpiece Clamping
Clamping: Ensure that plastic workpieces are securely clamped to prevent movement during machining. Use soft clamps or shims to avoid damaging the material.
Vibration: Minimize vibration to ensure accurate cuts and smooth surfaces. Ensure that the workpiece is properly supported. - Machining Techniques
Drilling: Drill holes using low speeds and steady feed rates to avoid cracking or melting the material. Select a drill design suitable for plastics.
Milling: During milling operations, use appropriate speeds and feeds to obtain a smooth cutting surface and avoid overheating. Avoid excessive depth of cut at one time.
Turning: When turning plastics, use sharp tools and moderate speeds to avoid melting and to ensure a smooth surface. - Surface Preparation
Deburring: After machining, remove edge burrs and any sharp or rough areas. This can be done by manual deburring or by using specialized tools. - Safety
Dust control: The processing of plastics generates fine dust, which can be harmful to the respiratory tract. Use dust extraction systems and personal protective equipment (PPE).
Ventilation: Ensure good ventilation to avoid the build-up of harmful gases, especially when processing plastics that may emit harmful gases. - Material Specific Considerations
Thermoplastics vs. thermosets: Thermoplastics (e.g., ABS, PC) can be reheated and reshaped, while thermosets (e.g., epoxy) cannot. Different types of plastics may require different machining parameters and tooling.
Precision Machined Plastic Parts from Yumei Hardware
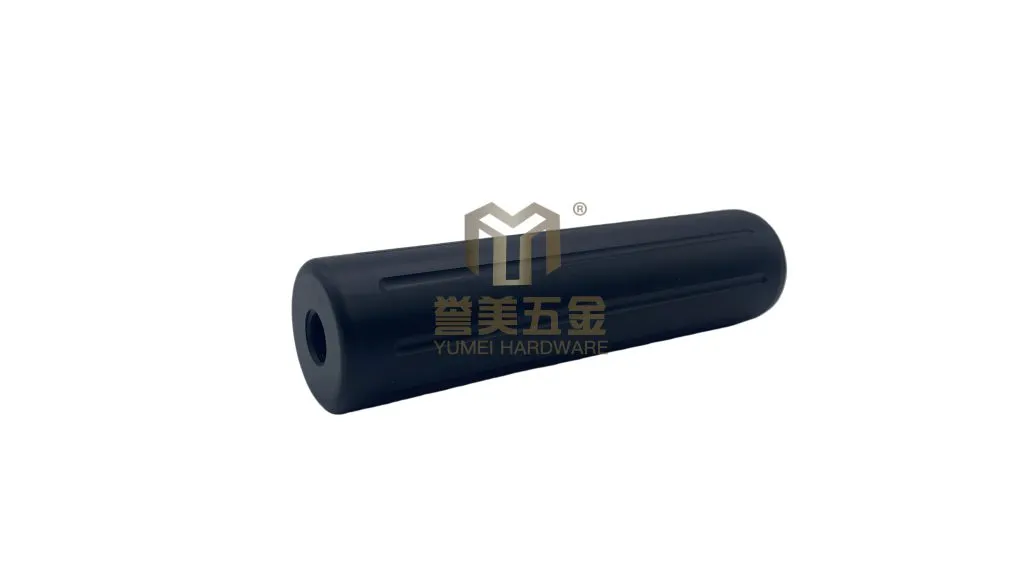
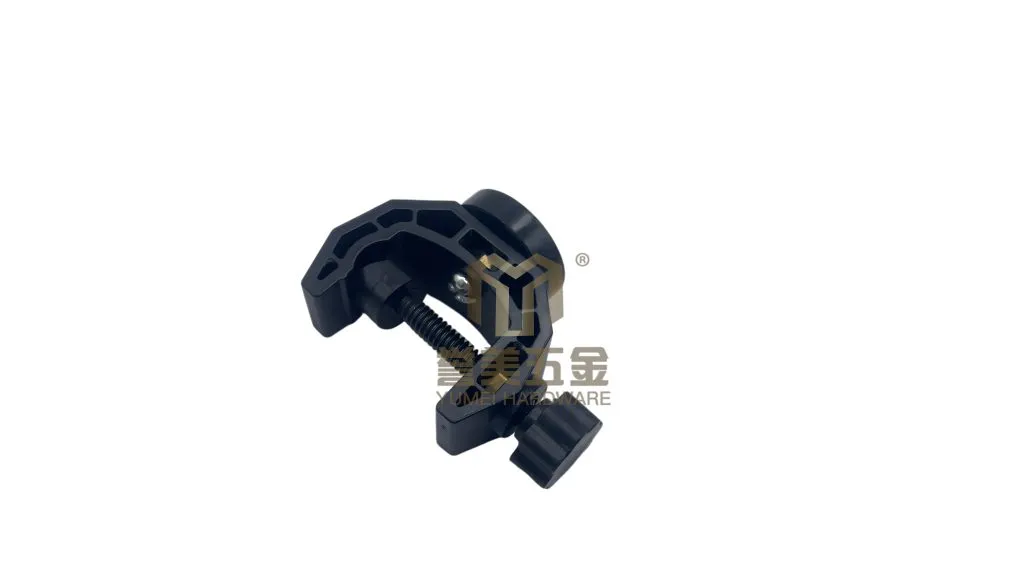
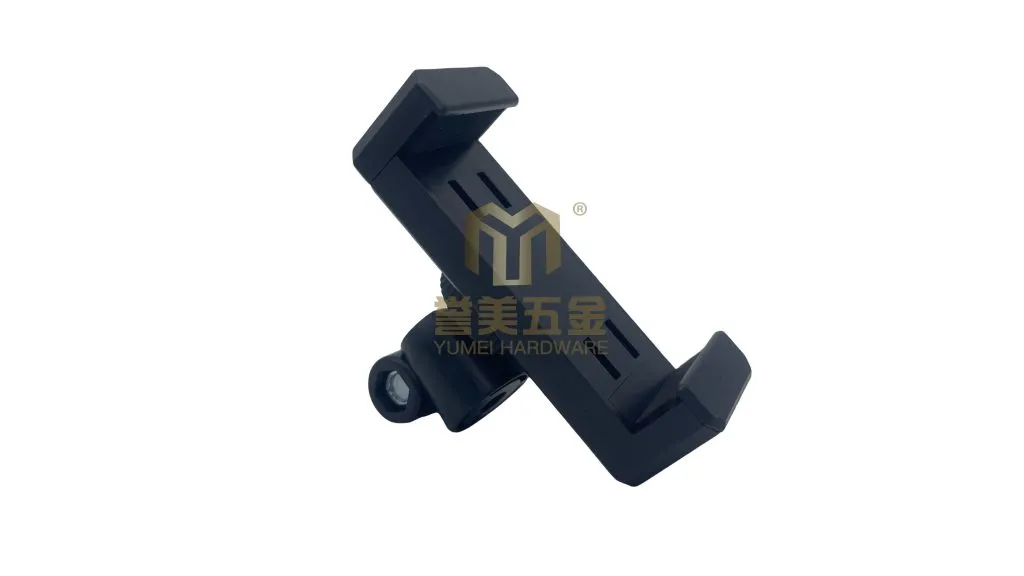