What is CNC Machining?
CNC machining is a subtractive manufacturing process that uses computerized controls to operate machine tools such as lathes, mills, routers, and grinders. It transforms raw materials like metal, plastic, or wood into finished parts by removing material layer by layer. The process is guided by pre-programmed software, which dictates the movement of tools and machinery with extreme precision.
A Brief History of CNC Machining
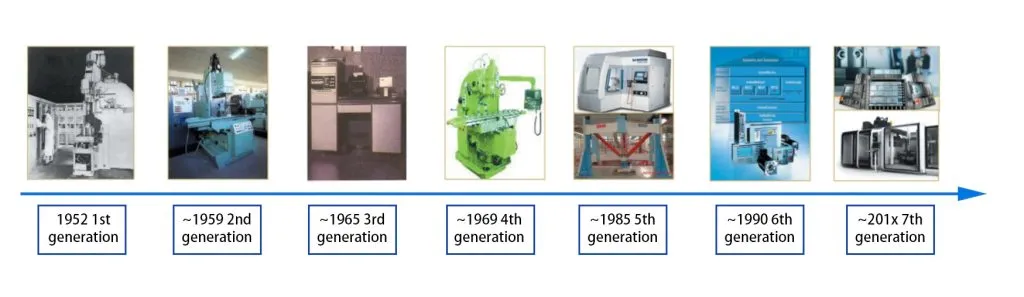
CNC machining traces its roots back to the 1940s and 1950s when the first numerical control (NC) machines were developed. These early machines used punched tape to control their operations. With the advent of computers in the 1960s, NC evolved into CNC, offering greater flexibility, accuracy, and efficiency. Today, CNC machining is a vital part of industries ranging from aerospace to healthcare.
Why is CNC Machining Important?
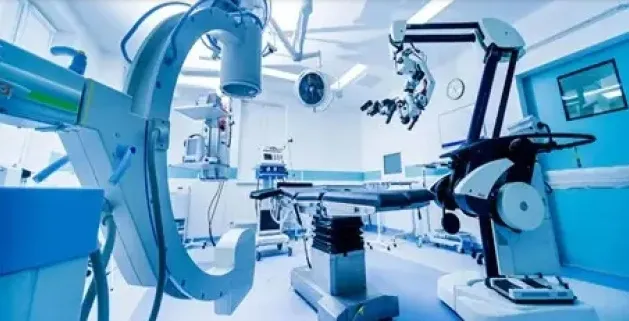
- Precision and Accuracy: CNC machines can produce parts with tolerances as tight as ±0.001 inches, ensuring consistency and quality.
- Efficiency: Automation reduces human error and speeds up production, making it ideal for high-volume manufacturing.
- Versatility: CNC machines can work with a wide range of materials, including metals, plastics, ceramics, and composites.
- Complexity: They can create intricate geometries that would be impossible or impractical with manual machining.
- Scalability: CNC machining is suitable for both prototyping and mass production.
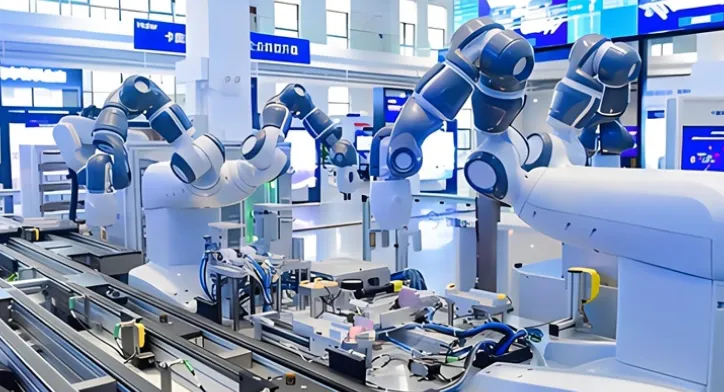
How Does CNC Machining Work? A Step-by-Step Breakdown
Understanding the CNC machining process involves breaking it down into key stages:
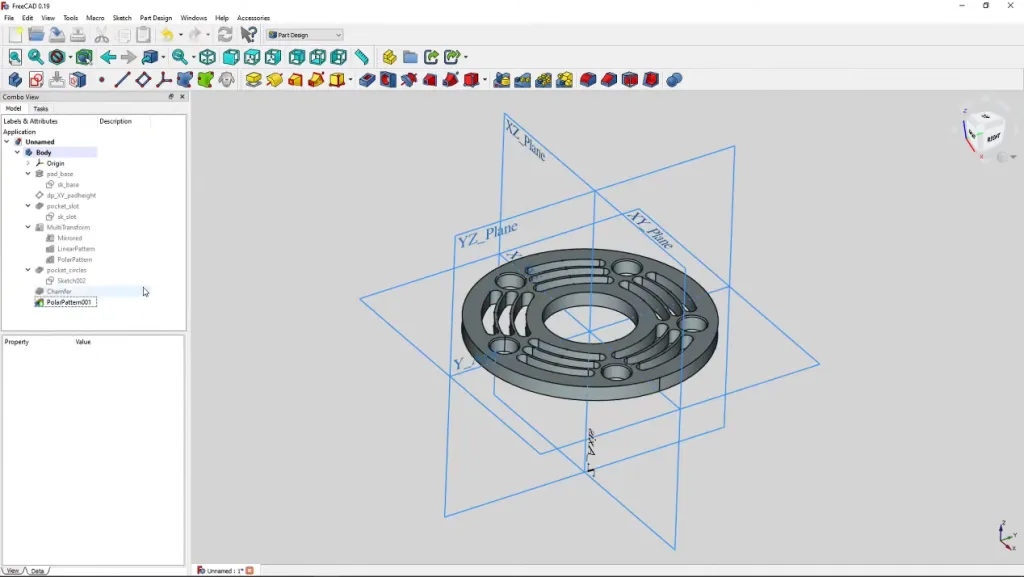
Step 1: Designing the Part (CAD)
The process begins with Computer-Aided Design (CAD) software, where engineers create a 3D model of the part. This digital blueprint defines the part’s dimensions, geometry, and features.
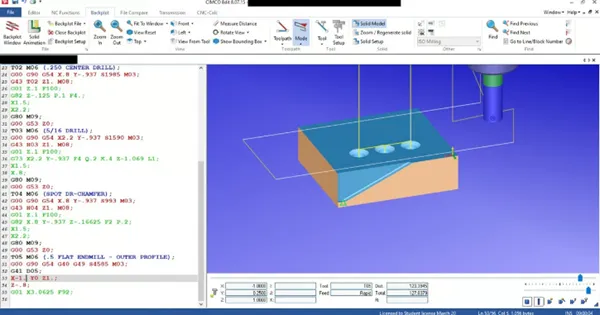
Step 2: Preparing the Program (CAM)
The CAD file is then imported into Computer-Aided Manufacturing (CAM) software. Here, the model is translated into a set of instructions, known as G-code, which the CNC machine can understand. The G-code controls the machine’s movements, toolpaths, and operations.
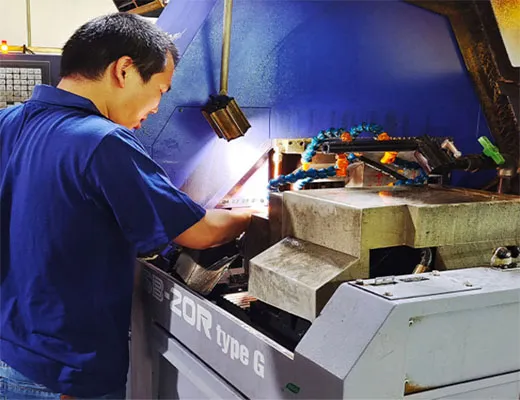
Step 3: Setting Up the Machine
Before machining begins, the operator sets up the CNC machine by selecting the appropriate tools, securing the raw material, and loading the G-code program.
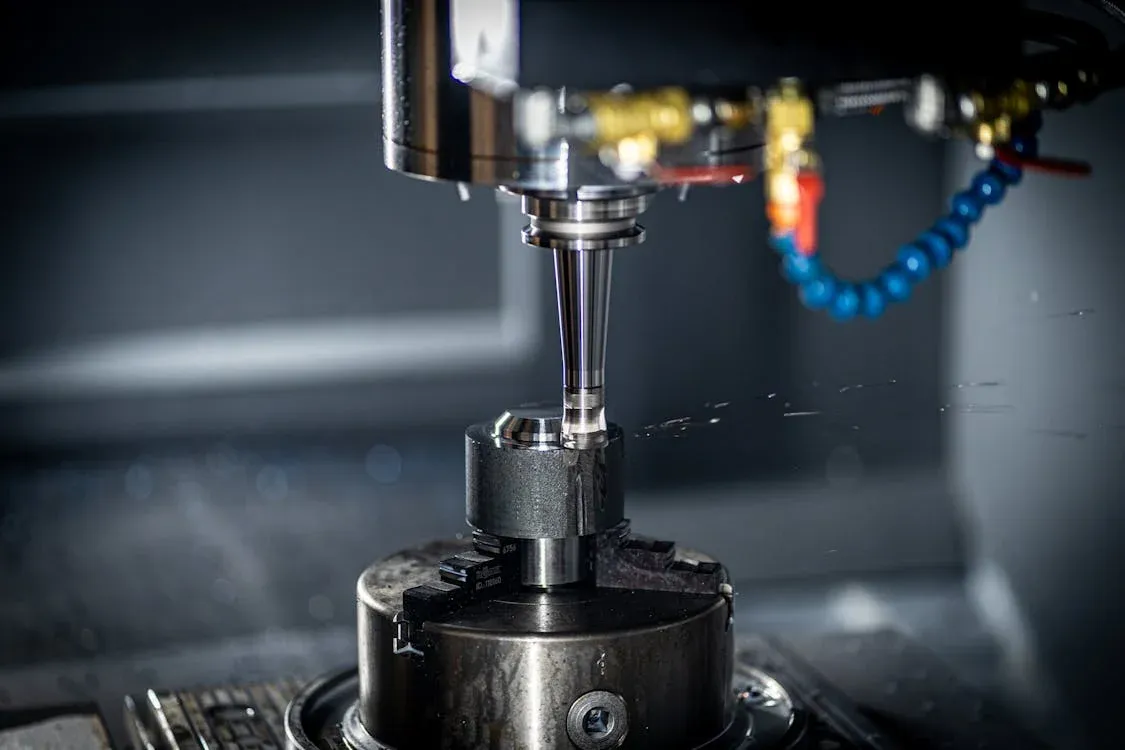
Step 4: Machining the Part
The CNC machine follows the G-code instructions to cut, drill, mill, or turn the raw material into the desired shape. This process may involve multiple tools and operations, depending on the part’s complexity.
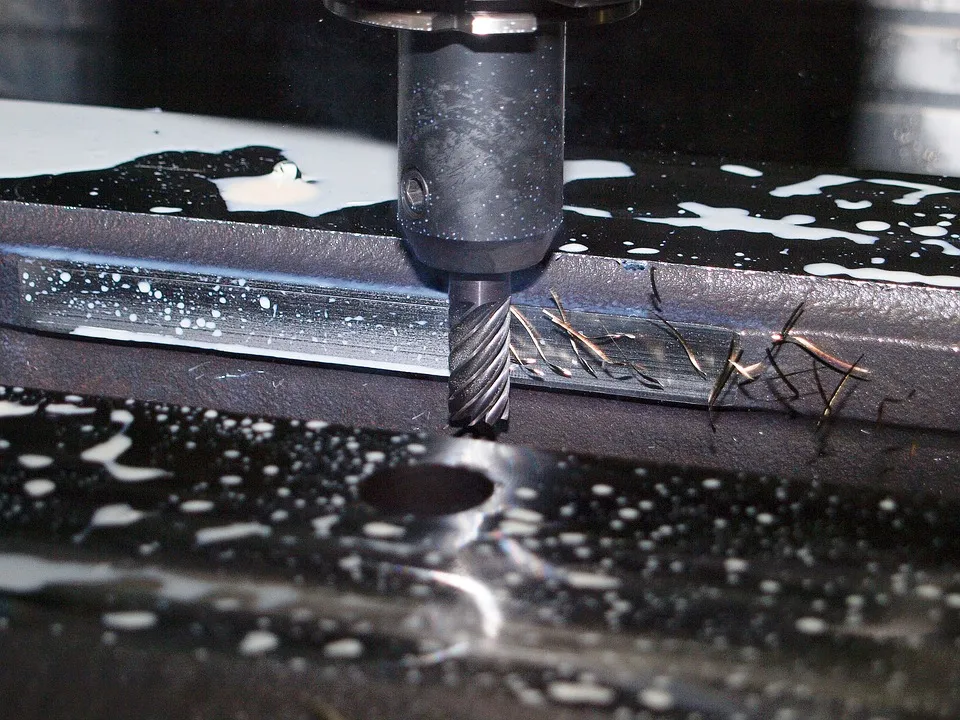
Step 5: Post-Processing
After machining, the part may undergo additional processes such as deburring, polishing, or surface treatment to achieve the desired finish.
What Are the Different Types of CNC Machines?
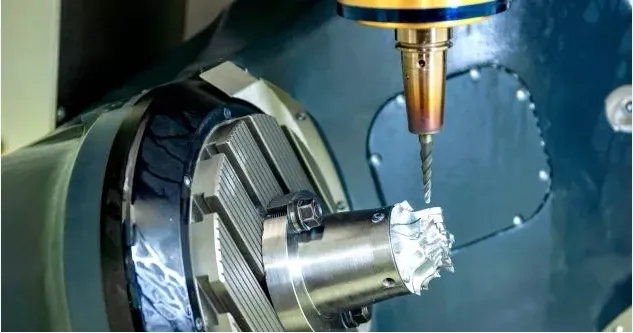
CNC machining encompasses a variety of machine types, each suited for specific tasks:
- CNC Mills: Used for cutting and drilling, these machines are highly versatile and can handle complex geometries.
- CNC Lathes: Ideal for cylindrical parts, lathes rotate the workpiece while a cutting tool shapes it.
- CNC Routers: Commonly used for woodworking and plastic fabrication, routers are excellent for cutting large sheets of material.
- CNC Plasma Cutters: Designed for cutting metal, plasma cutters use a high-velocity jet of ionized gas.
- CNC Laser Cutters: These machines use focused laser beams to cut or engrave materials with high precision.
- CNC Grinders: Used for finishing operations, grinders achieve tight tolerances and smooth surfaces.
What Materials Can Be Used in CNC Machining?
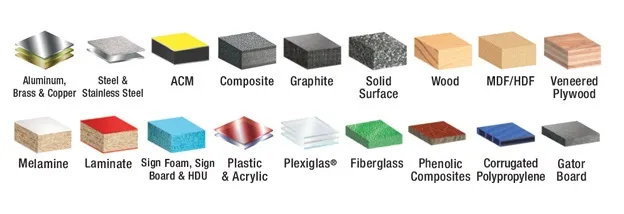
CNC machining is compatible with a wide range of materials, each offering unique properties:
- Metals: Aluminum, steel, titanium, brass, and copper are commonly used for their strength and durability.
- Plastics: ABS, polycarbonate, and PEEK are popular for their lightweight and corrosion-resistant properties.
- Composites: Materials like carbon fiber and fiberglass are used in high-performance applications.
- Wood: CNC routers are often used for woodworking projects, from furniture to decorative items.
- Ceramics: Advanced ceramics are machined for applications requiring high thermal and electrical resistance.
What Are the Applications of CNC Machining?
CNC machining is used across a wide range of industries:
- Aerospace: Precision components like turbine blades and engine parts are manufactured using CNC machines.
- Automotive: From engine blocks to custom car parts, CNC machining plays a critical role in vehicle production.
- Medical: Surgical instruments, implants, and prosthetics are made with CNC technology for their precision and biocompatibility.
- Electronics: CNC machines produce circuit boards, enclosures, and connectors with high accuracy.
- Consumer Goods: Everyday items like smartphone cases, jewelry, and kitchenware are often CNC-machined.
What Are the Latest Trends in CNC Machining?
The CNC machining industry is constantly evolving, with several emerging trends shaping its future:
- Multi-Axis Machining: 5-axis and 6-axis CNC machines enable the production of highly complex parts in a single setup.
- Automation and IoT: Smart factories are integrating CNC machines with IoT sensors for real-time monitoring and predictive maintenance.
- AI-Driven Optimization: Artificial intelligence is being used to optimize toolpaths, reduce waste, and improve efficiency.
- Hybrid Manufacturing: Combining CNC machining with additive manufacturing (3D printing) allows for greater design flexibility and faster prototyping.
- Sustainable Practices: Manufacturers are adopting eco-friendly techniques, such as using recyclable materials and reducing energy consumption.
Step-by-Step Guide to Optimizing CNC Machining Costs
CNC machining can be expensive, but there are ways to optimize costs without compromising quality:
- Design for Manufacturability (DFM): Simplify part designs to reduce machining time and material waste.
- Material Selection: Choose cost-effective materials that meet the part’s performance requirements.
- Batch Production: Group similar parts together to minimize setup times and tool changes.
- Tool Management: Use high-quality tools and maintain them regularly to extend their lifespan.
- Process Automation: Implement automated systems to reduce labor costs and improve efficiency.
What Does the Future Hold for CNC Machining?
As technology advances, CNC machining will continue to play a pivotal role in manufacturing. Key developments to watch include:
- Integration with AI and Machine Learning: Enhanced algorithms will optimize machining processes and reduce downtime.
- Increased Adoption of Robotics: Collaborative robots (cobots) will work alongside CNC machines to improve productivity.
- Expansion of Digital Twins: Virtual replicas of CNC machines will enable real-time simulation and troubleshooting.
- Growth in Customization: CNC machining will enable mass customization, allowing manufacturers to produce personalized products at scale.
Why Should You Consider a Career in CNC Machining?
CNC machining offers exciting career opportunities for skilled professionals. Key roles include CNC operators, programmers, and engineers. With the growing demand for precision manufacturing, these careers offer competitive salaries, job stability, and opportunities for advancement. Many technical schools and training programs provide specialized education in CNC machining, making it accessible to aspiring professionals.
Conclusion
CNC machining is a transformative technology that has reshaped the manufacturing landscape. From its precise and efficient processes to its wide-ranging applications, CNC machining is indispensable in today’s industries. As the field continues to evolve with advancements in automation, AI, and sustainable practices, its importance will only grow. Whether you’re a seasoned professional or a curious beginner, understanding CNC machining is essential for staying ahead in the world of modern manufacturing.
By exploring the what, why, and how of CNC machining, we’ve uncovered its significance, processes, and future potential. As industries continue to innovate, CNC machining will remain at the forefront, driving progress and enabling the creation of tomorrow’s technologies.