What Are Stainless Steel CNC Turned Parts?
Stainless steel CNC turned parts are precision components manufactured using computer numerical control (CNC) turning machines. These machines rotate a stainless steel workpiece while a cutting tool removes material to achieve the desired shape and dimensions. CNC turning is ideal for creating cylindrical or round parts, such as shafts, bolts, fittings, and connectors. Stainless steel is a popular material choice due to its durability, corrosion resistance, and ability to withstand high temperatures. Industries like automotive, aerospace, medical, and food processing rely on stainless steel CNC turned parts for their strength, reliability, and aesthetic appeal.
How Does CNC Turning Work for Stainless Steel Parts?
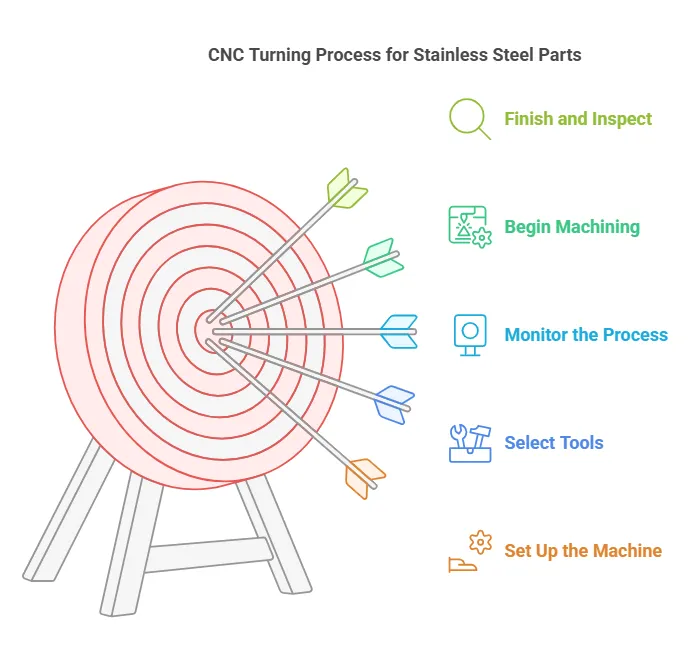
CNC turning for stainless steel parts involves a precise and automated process. Here’s a step-by-step breakdown:
- Design the Part: Create a detailed CAD model of the part, specifying dimensions, tolerances, and surface finishes.
- Convert to CNC Code: Use CAM software to generate G-code, which instructs the CNC machine on toolpaths and operations.
- Set Up the Machine: Secure the stainless steel workpiece in the chuck of the CNC lathe, ensuring it is properly aligned.
- Select Tools: Choose appropriate cutting tools made from materials like carbide or ceramic, designed to handle stainless steel’s hardness.
- Begin Machining: Start the CNC program, allowing the machine to rotate the workpiece while the cutting tool shapes it.
- Monitor the Process: Continuously check for accuracy and make adjustments as needed to maintain precision.
- Finish and Inspect: Once machining is complete, remove the part and inspect it for quality and adherence to specifications.
This process ensures high precision and repeatability, making CNC turning ideal for stainless steel parts.
What Are the Advantages of Using Stainless Steel for CNC Turned Parts?
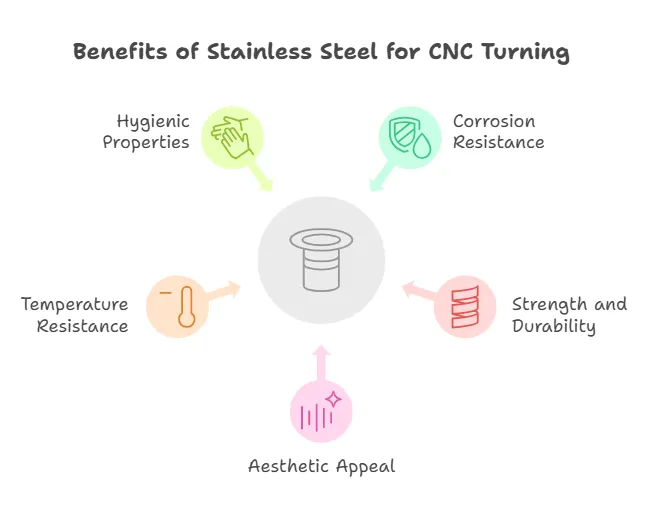
Stainless steel offers several benefits for CNC turned parts, making it a preferred material in many industries:
- Corrosion Resistance: Stainless steel’s chromium content forms a protective oxide layer, making it resistant to rust and corrosion.
- Strength and Durability: It can withstand high stress, pressure, and wear, ensuring long-lasting performance.
- Aesthetic Appeal: Stainless steel has a sleek, polished finish, ideal for visible components.
- Temperature Resistance: It maintains its properties at high and low temperatures, suitable for extreme environments.
- Hygienic Properties: Its non-porous surface makes it easy to clean and ideal for medical and food processing applications.
These advantages make stainless steel CNC turned parts a reliable choice for demanding applications.
What Are the Applications of Stainless Steel CNC Turned Parts in Various Industries?
Stainless steel CNC turned parts are widely used across industries due to their versatility and performance. Key applications include:
- Automotive: Engine components, fuel injectors, and hydraulic fittings.
- Aerospace: Precision fasteners, landing gear parts, and turbine components.
- Medical: Surgical instruments, implants, and diagnostic equipment.
- Food Processing: Valves, pumps, and fittings that meet hygiene standards.
- Electronics: Connectors, housings, and heat sinks for electronic devices.
These industries benefit from the material’s strength, corrosion resistance, and ability to meet tight tolerances.
How to Select the Right Stainless Steel for CNC Turning
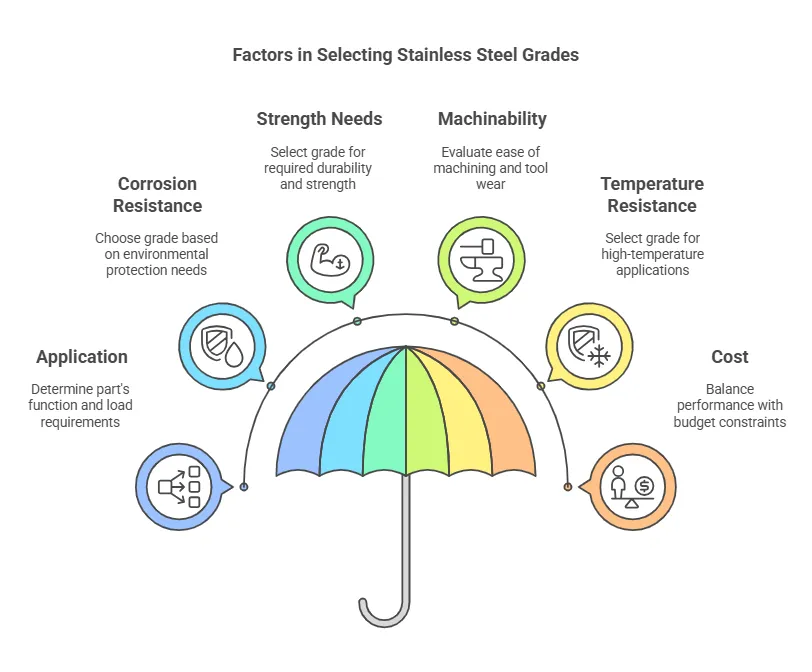
Choosing the right stainless steel grade for CNC turning depends on the part’s application and requirements. Here’s a guide:
- Identify the Application: Determine the part’s function, environmental conditions, and load requirements.
- Consider Corrosion Resistance: For harsh environments, choose grades like 316 or 304, which offer excellent corrosion resistance.
- Evaluate Strength Needs: For high-strength applications, consider martensitic grades like 410 or 420.
- Check Machinability: Grades like 303 are easier to machine due to added sulfur, reducing tool wear.
- Assess Temperature Resistance: For high-temperature applications, select grades like 310 or 321.
- Factor in Cost: Balance performance requirements with budget constraints to choose the most cost-effective option.
By following these steps, you can select the ideal stainless steel grade for your CNC turned parts.
What Is the Process Flow of Manufacturing Stainless Steel CNC Turned Parts?
The manufacturing process for stainless steel CNC turned parts involves several critical steps to ensure precision and quality:
-
Design and Planning:
- Create a detailed CAD model of the part, specifying dimensions, tolerances, and surface finishes.
- Use CAM software to generate G-code for the CNC machine.
-
Material Selection:
- Choose the appropriate stainless steel grade based on the part’s application and requirements.
-
Machine Setup:
- Secure the stainless steel workpiece in the CNC lathe’s chuck, ensuring proper alignment.
- Install the necessary cutting tools and calibrate the machine.
-
CNC Turning:
- Execute the CNC program, allowing the machine to rotate the workpiece while the cutting tool shapes it.
- Monitor the process to ensure accuracy and make adjustments as needed.
-
Deburring and Finishing:
- Remove any sharp edges or burrs from the machined part.
- Apply surface treatments like polishing or passivation to enhance corrosion resistance.
-
Inspection and Testing:
- Use precision measuring tools like calipers, micrometers, and CMMs to verify dimensions and tolerances.
- Conduct additional tests, such as hardness or corrosion resistance checks, if required.
-
Packaging and Delivery:
- Clean and package the finished parts to prevent damage during transportation.
This streamlined process ensures high-quality stainless steel CNC turned parts that meet industry standards.
What Are the Key Factors in Stainless Steel CNC Turning?
Several factors influence the success of stainless steel CNC turning:
-
Tool Selection:
- Use cutting tools made from carbide or ceramic to handle stainless steel’s hardness and reduce wear.
-
Cutting Parameters:
- Optimize spindle speed, feed rate, and depth of cut to balance efficiency and tool life.
-
Coolant and Lubrication:
- Apply appropriate coolants to dissipate heat and prevent workpiece deformation or tool damage.
-
Workpiece Fixturing:
- Ensure the workpiece is securely clamped to minimize vibrations and maintain accuracy.
-
Machine Rigidity:
- Use a robust CNC lathe to reduce vibrations and improve surface finish.
-
Operator Skill:
- Employ experienced operators who can troubleshoot issues and optimize machining parameters.
By addressing these factors, manufacturers can achieve high precision and efficiency in stainless steel CNC turning.
How Does Product Testing and Quality Control Work for Stainless Steel CNC Turned Parts?
Quality control is essential to ensure stainless steel CNC turned parts meet specifications and performance standards. Here’s how it’s done:
-
Dimensional Inspection:
- Use tools like calipers, micrometers, and coordinate measuring machines (CMMs) to verify part dimensions.
-
Surface Finish Analysis:
- Measure surface roughness using profilometers to ensure it meets design requirements.
-
Material Testing:
- Conduct hardness tests to verify the material’s mechanical properties.
- Perform corrosion resistance tests for applications in harsh environments.
-
Visual Inspection:
- Check for surface defects, such as scratches, cracks, or burrs.
-
Functional Testing:
- Test the part’s performance in real-world conditions, if applicable.
-
Documentation:
- Maintain detailed records of inspections and tests for traceability and compliance.
These steps ensure that every stainless steel CNC turned part meets the highest quality standards.
What Are the Common Challenges in CNC Turning of Stainless Steel Parts?
CNC turning of stainless steel parts presents several challenges:
-
Tool Wear:
- Stainless steel’s hardness and abrasiveness can cause rapid tool wear, requiring frequent replacements.
-
Heat Generation:
- High cutting speeds can generate excessive heat, leading to workpiece deformation or tool failure.
-
Work Hardening:
- Stainless steel tends to harden during machining, making it difficult to achieve smooth finishes.
-
Chip Control:
- Long, stringy chips can interfere with the machining process and damage the workpiece.
-
Surface Finish:
- Achieving a high-quality surface finish requires precise control of cutting parameters and tool geometry.
-
Cost:
- The need for specialized tools and coolants can increase production costs.
Overcoming these challenges requires careful planning, advanced tooling, and skilled operators.
How Can You Optimize Efficiency in the Production of Stainless Steel CNC Turned Parts?
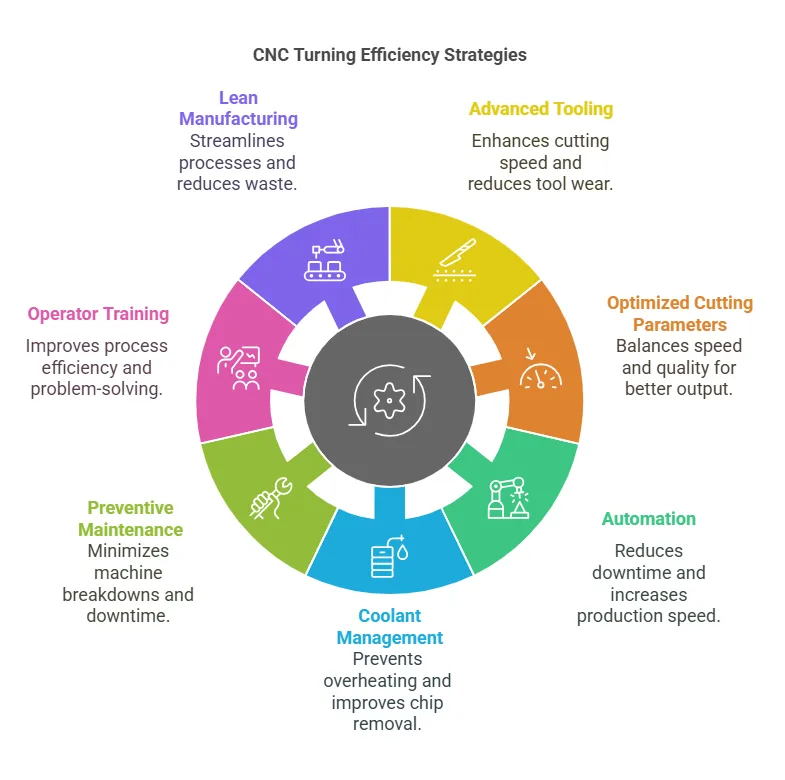
Optimizing efficiency in stainless steel CNC turning involves several strategies:
-
Advanced Tooling:
- Use high-performance cutting tools with coatings like TiN or TiAlN to reduce wear and improve cutting speeds.
-
Optimized Cutting Parameters:
- Adjust spindle speed, feed rate, and depth of cut to maximize material removal rates while maintaining quality.
-
Automation:
- Implement automated loading and unloading systems to reduce downtime and increase throughput.
-
Coolant Management:
- Use high-pressure coolant systems to improve chip evacuation and reduce heat buildup.
-
Preventive Maintenance:
- Regularly inspect and maintain CNC machines to prevent unexpected breakdowns.
-
Operator Training:
- Train operators to optimize machining processes and troubleshoot issues effectively.
-
Lean Manufacturing:
- Implement lean principles to minimize waste and streamline production workflows.
By adopting these strategies, manufacturers can enhance productivity and reduce costs in the production of stainless steel CNC turned parts.