As machined, Smooth machining and Fine machining, each have their unique characteristics and application scenarios. In order to help you make the best choice for different projects, this article will provide a comprehensive comparison of these three processing technologies, exploring their characteristics, application areas, and selection criteria in depth.
All parts machined by CNC leave machining marks along the path of the cutting tool. Surface quality is usually measured by mean surface roughness (Ra). Ra represents the average deviation between the machined surface and the ideal smooth surface.
In the mechanical manufacturing process, the quality of the machined surface directly affects the accuracy and performance of the parts. High-quality surfaces can improve the wear resistance, corrosion resistance and strength of parts, thereby extending the service life of parts. If the surface of the parts is not properly treated, it will cause very serious consequences, such as in the construction industry, when the steel member is used in a humid environment without proper surface treatment, the surface is easy to oxidize and rust, thereby reducing its structural strength, resulting in the fracture or deformation of the member during use. In automobile manufacturing, if the body surface painting is not properly handled, there may be bubbles, flow hanging or color difference, affecting the beauty of the vehicle and market competitiveness. For example, if the surface treatment of the connecting parts of the aircraft wing fails to meet the smoothness requirements, it may cause fatigue cracks in long-term use due to stress concentration, and may lead to structural failure in serious cases.
This article will explore three Surface Finishing techniques: As Machined, Smooth Machining, and Fine Machining. Each process has its own unique application scenarios and processing requirements, from low surface finish to extremely high precision, each technology in different conditions to meet the specific product needs, we will analyze and compare.
As Machined
As machined finish is a machined that come right off the machine, without any other post-finishing involved. The state of a part after CNC machining without additional surface treatment or finishing. The surface of the part remains in its original state after processing. Surface roughness range is generally Ra 3.2μm/Ra 126μin.
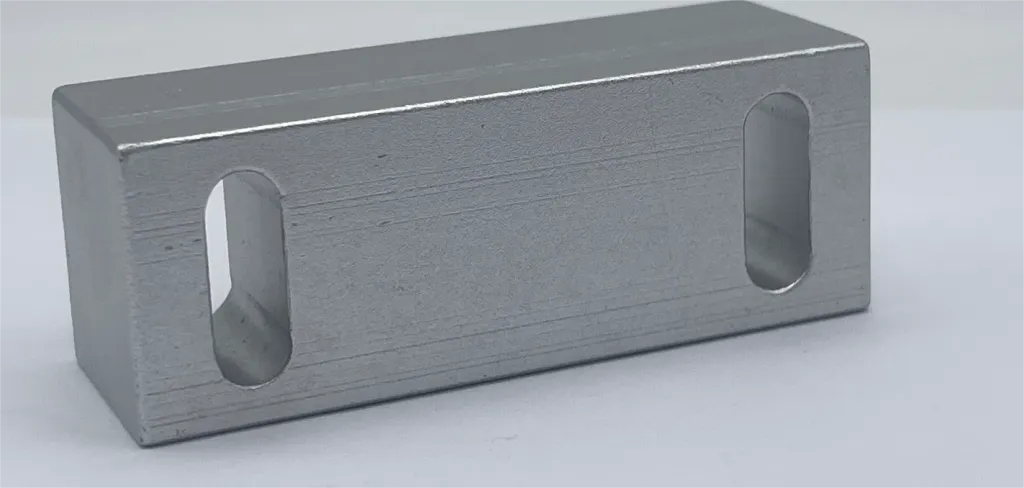
Features
High precision: Because there are no additional surface treatment steps, AS machined parts retain the dimensional accuracy immediately after CNC machining. This means that very precise tolerances can be maintained for parts after production.
Obvious processing marks. Since no further surface treatment has been done, the parts AS machined will retain the obvious lines left by the tools and machine tools during the machining process.
Low cost and fast delivery…
Application
Prototyping: In the early stages of product development, priority is often given to the functionality of parts rather than surface quality. AS a result, many engineering teams use AS machined parts to quickly evaluate designs when prototyping.
Internal assemblies: For internal components that will eventually be covered by other housings, surface treatment is not important, so AS machined is sufficient to meet this need.
Mechanical parts: In the field of industrial equipment, automation devices, mechanical engineering, the appearance of parts is usually not a priority factor, so the As machined parts are widely used.
Advantages
Highly accurate to meet tight tolerances
The processing cost is low. Additional processes such as polishing, sandblasting and electroplating are omitted.
Short delivery time since postprocessing is not required.
Disadvantages
Machine tool cutting marks are visible, The appearance of the parts is not attractive.
No protection for materials with low corrosion resistance, low wear resistance, resulting in reduced performance or shortened life of parts..
Smooth Machining
Smooth Machining is a process in which the surface of a part is subjected to additional finishing treatment after CNC machining to reduce surface roughness and machining marks and make the surface more smooth and flat. The standard smoothing surface roughness is Ra 1.6 μm (63 μin). Light surface scratches are visible.Smooth Machining provides a higher surface finish than rough surfaces AS machined and is usually suitable for parts with higher requirements for appearance, smoothness or surface performance.
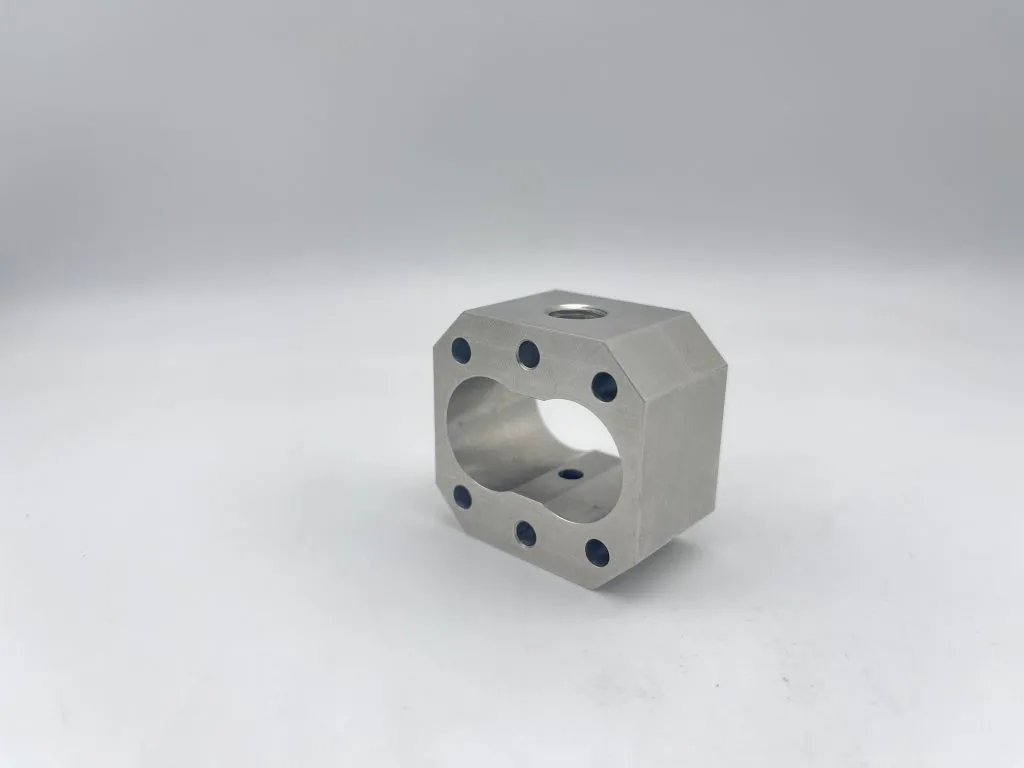
Features
Higher surface finish: Through careful machining or secondary operations, tool marks are reduced and the surface of the part is flatter and smoother.
Reduced friction: Smoother surfaces are better suited for assemblies that require reduced friction or high lubrication requirements.
Enhanced Appearance: Smooth surfaces make parts look better and are suitable for cosmetically exposed parts or consumer products.
Fine Tolerance Control: Although the surface finish is improved, precise tolerances from CNC machining are maintained.
Application
Consumer electronics: e.g. metal cases for smartphones, laptops, where consumers demand the highest level of appearance, making Smooth Machining the ideal choice.
Medical Devices: such as surgical tools, implants, etc. These components require not only precision, but also a smooth surface to ensure safety and hygiene.
Luxury goods: Products such as high-end watches and jewelry often use Smooth Machining to ensure a smooth, sophisticated appearance.
Advantages
Higher surface finish
Reduced friction
High precision
Disadvantages
Increased cost and processing time.
There are certain requirements for materials, some materials are more difficult to achieve extremely smooth surfaces through machining, so specific materials may need to be selected to achieve the desired finish.
Fine Machining
Fine machining is the process of obtaining finer finishes through higher accuracy machines, lower feeds, sharper tools, or a combination of all of the above. Surface roughness range Ra 0.8μm/Ra 32μin. Fine Machining is often used to manufacture parts with very tight tolerances, smooth surfaces and extremely high performance, especially in demanding fields such as aerospace, medical equipment and high-end electronics.
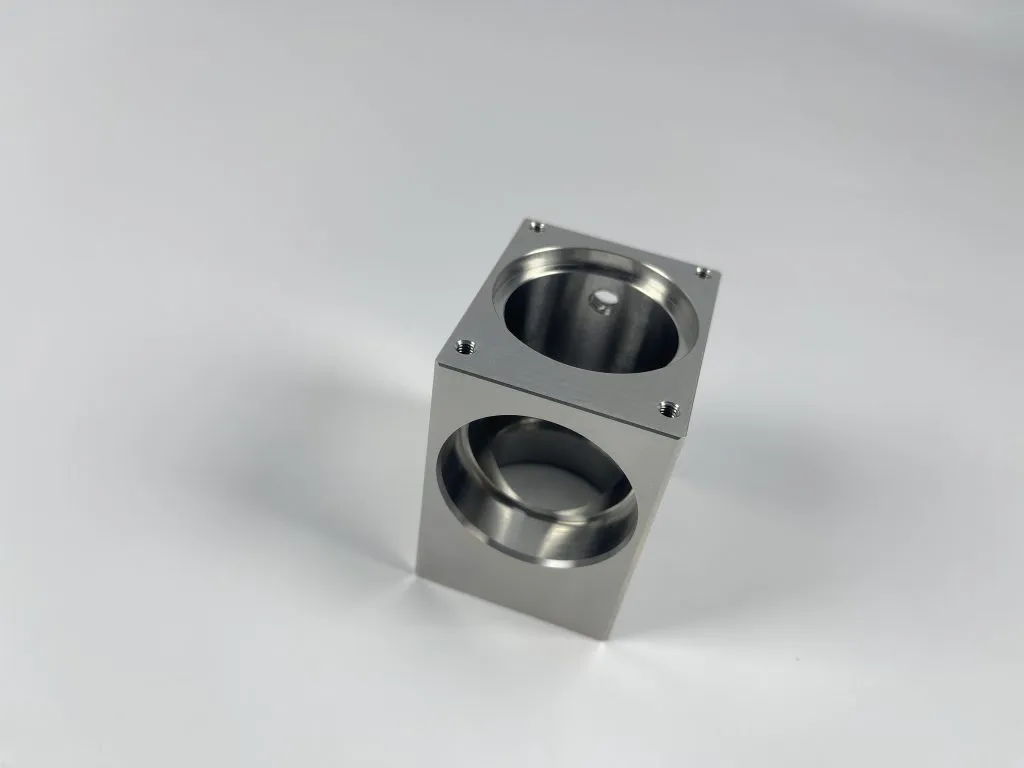
Features
Extremely high dimensional accuracy: Fine Machining allows for very high machining accuracy, often with tolerances down to the micron level (μm).
Smoother surfaces: Fine Machining parts have a very high surface quality with very low roughness Ra values.
Complex Geometry: Fine Machining can be used to machine complex geometries, including small, delicate structures and micro parts that are difficult to manufacture by conventional machining methods.
Suitable for a wide range of materials: Fine Machining can be applied to a wide range of materials, including metals, plastics and composites.
Application
Aerospace: aerospace engine parts, aircraft structural parts, and other components requiring high strength and high precision.
Medical devices: such as surgical instruments, implants, precision medical equipment parts, etc., requiring extremely high surface finish and dimensional accuracy.
Automotive industry: high-precision engine parts, transmission system components and other parts requiring high wear resistance.
Electronics: high-end consumer electronics housings, semiconductor parts, etc., requiring precision machining to ensure assembly accuracy and appearance quality.
Comparison Table
As machined | Smooth Machining | Fine machining | |
surface roughness | Ra 3.2μm / Ra 126μin | Ra 1.6μm / Ra 63μin | Ra 0.8μm / Ra 32μin |
Cost | low | medium | high |
process time | short | medium | long |
Advantages | Cost-effective, quick | Smooth surface, reduced friction | High precision, superior surface quality |
Disadvantages | Rough surface, noticeable tool marks | Relatively higher cost, more complex process | Expensive, time-consuming, high equipment requirements |
How to choose the right surface processing?
Product requirement
If the part has low surface finish requirements and only needs to meet functional requirements (such AS assembly, tolerances, etc.), you can choose AS Machined. This machining method is economical and fast, and is suitable for parts with low surface quality requirements. If the part has very high requirements for surface finish, such as close to the mirror effect, you can choose Fine Machining. This is suitable for high-precision instruments, medical devices and aerospace parts. Other general requirements can be selected Smooth machining, taking into account cost and appearance.
Material type
AS Machined and Smooth Machining suitable for most common metal and plastic materials. For relatively simple or common materials, these processing processes can usually achieve better results. Titanium alloys or other high-strength materials may need to be selected for Fine Machining. This process can handle more difficult materials and ensure surface quality and precision.
Cost budgeting
If the project budget is limited and the requirements for surface treatment are not high, you can choose AS Machined. It has low processing costs, is suitable for mass production and does not require high finish parts. For projects that require extremely high precision and surface quality, Fine Machining is more expensive, but it ensures the best performance and appearance of the part. For the cost requirements are not strict, but also to take into account the cost and surface quality, more suitable for Smooth machining
Machining time
According to the delivery time requirements, the best processing method is selected. Generally speaking, the shortest processing time is AS machined, followed by Smooth machining, and the longest processing time is required by fine machining. If you want to complete the surface quality requirements in one go, especially the high finish requirements, Fine Machining is the best choice.
When selecting the right surface processing process, the function of the part, the accuracy requirements, the surface finish, the cost, the material and the application scenario should be considered comprehensively. According to the needs of parts to choose the right process, not only to meet the technical requirements, but also to control costs and improve production efficiency.