What is a CNC Machine?
A CNC (Computer Numerical Control) machine is an automated manufacturing tool that uses pre-programmed computer software to control the movement of machinery and tools. These machines are capable of cutting, shaping, and fabricating materials such as metal, plastic, wood, and composites with high precision. CNC machines are widely used in industries like aerospace, automotive, and electronics due to their ability to produce complex parts efficiently and consistently. Unlike manual machining, CNC machines operate with minimal human intervention, reducing errors and increasing productivity.
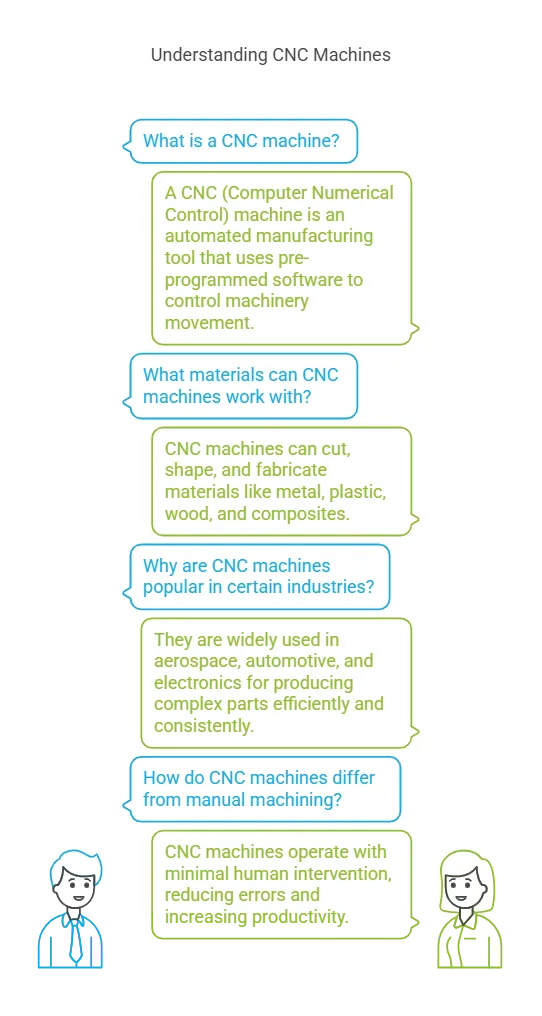
How Does the CNC Machine Structure and Workflow Operate?
The structure of a CNC machine typically includes the following components
Control Unit: The brain of the machine, where the CNC program is loaded and executed.
Drive System: Motors and gears that move the machine’s axes (X, Y, Z) and spindle.
Spindle: The rotating component that holds and drives the cutting tool.
Worktable: The surface where the material is secured for machining.
Tool Changer: Automatically swaps tools during the machining process for multi-operation tasks.
The workflow of a CNC machine involves these steps
Design: Create a CAD (Computer-Aided Design) model of the part.
Programming: Convert the CAD model into CNC code using CAM (Computer-Aided Manufacturing) software.
Setup: Load the material onto the worktable and install the required tools.
Machining: The machine follows the programmed instructions to cut and shape the material.
Inspection: Verify the finished part for accuracy and quality.
What is the Working Principle of CNC Machines?
CNC machines operate based on the following principles:
Input: The operator uploads a CNC program containing instructions for the machining process.
Interpretation: The machine’s control unit interprets the program and converts it into electrical signals.
Movement: Servo motors drive the machine’s axes to position the cutting tool accurately.
Cutting: The spindle rotates at high speeds, and the cutting tool removes material according to the programmed design.
Feedback: Sensors monitor the process and provide real-time feedback to ensure precision.
This automated process ensures consistent quality and reduces human error, making CNC machines ideal for high-volume production.
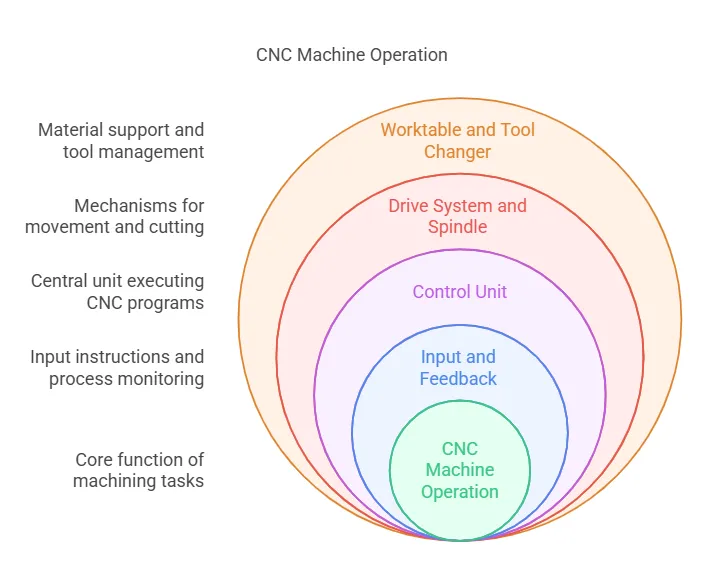
What Are the Applications of CNC Machines?
CNC machines are versatile and used across various industries for different applications, including:
Aerospace: Manufacturing precision components like turbine blades and engine parts.
Automotive: Producing engine blocks, transmission parts, and custom fittings.
Medical: Creating surgical instruments, implants, and prosthetics with high accuracy.
Electronics: Machining enclosures, heat sinks, and connectors.
Prototyping: Developing prototypes for new products quickly and cost-effectively.
Their ability to handle complex geometries and tight tolerances makes CNC machines indispensable in modern manufacturing.
How to Optimize the Work Environment for CNC Machines?
To ensure optimal performance and longevity of CNC machines, the work environment should be carefully managed. Here’s how:
Temperature Control: Maintain a stable temperature to prevent thermal expansion and contraction of machine components.
Cleanliness: Regularly clean the machine and work area to avoid debris buildup, which can affect precision.
Vibration Reduction: Install the machine on a stable surface to minimize vibrations during operation.
Proper Ventilation: Ensure adequate airflow to prevent overheating of the machine and coolant system.
Regular Maintenance: Follow a maintenance schedule to inspect and replace worn-out parts.
By optimizing the work environment, you can enhance the efficiency and lifespan of your CNC machine.
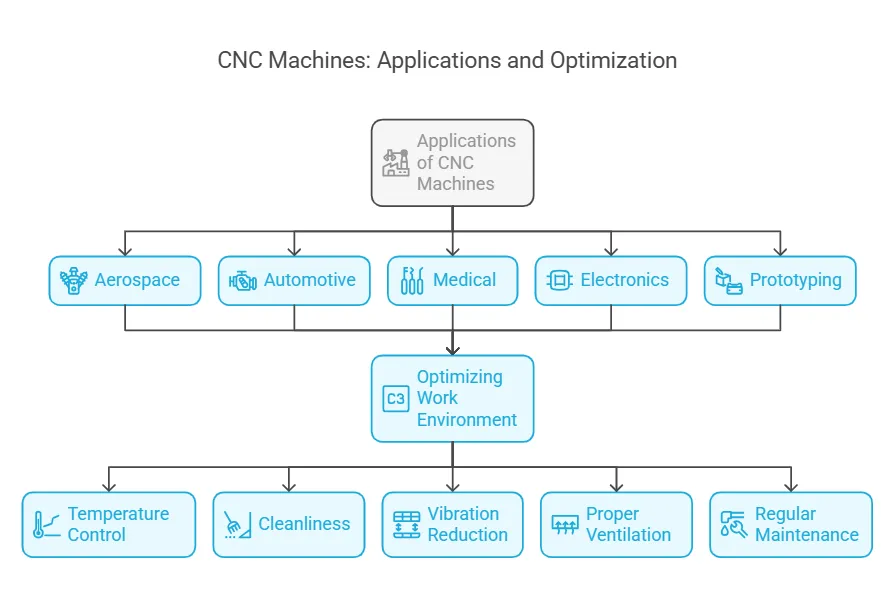
How Does Product Testing and Quality Control Work in CNC Machining?
Product testing and quality control are essential in CNC machining to ensure precision and reliability. Here’s how these processes are implemented:
Dimensional Inspection: Use tools like calipers, micrometers, and coordinate measuring machines (CMM) to verify part dimensions against design specifications.
Surface Finish Check: Inspect the surface quality of machined parts using profilometers or visual inspection.
Material Testing: Conduct hardness tests or chemical analysis to ensure the material meets required standards.
Functional Testing: Assemble and test parts to ensure they function as intended in their final application.
Documentation: Maintain detailed records of inspections and tests for traceability and compliance.
By integrating rigorous testing and quality control, manufacturers can deliver high-quality CNC-machined products consistently.
What Are the Usage Precautions and Best Practices for CNC Machines?
To ensure safety and efficiency when using CNC machines, follow these precautions and best practices:
Training: Ensure operators are fully trained in CNC machine operation and safety protocols.
Personal Protective Equipment (PPE): Wear safety glasses, gloves, and ear protection to prevent injuries.
Machine Inspection: Check the machine for damage or issues before starting.
Secure Workpieces: Properly clamp materials to the worktable to prevent movement during machining.
Emergency Stop: Familiarize yourself with the location and operation of the emergency stop button.
Avoid Loose Clothing: Ensure clothing and accessories do not get caught in moving parts.
Regular Maintenance: Keep the machine in good condition to avoid malfunctions that could lead to accidents.
Adhering to these precautions reduces the risk of accidents and ensures a safe working environment.
How to Maintain and Care for CNC Machines?
Proper maintenance and care are essential to keep CNC machines running efficiently and extend their lifespan. Follow these steps for effective maintenance:
Daily Maintenance
Clean the machine and remove debris from the worktable and tool changer.
Check coolant levels and top up if necessary.
Inspect tools for wear and replace them as needed.
Weekly Maintenance
Lubricate moving parts to reduce friction and prevent wear.
Inspect the spindle and belts for signs of damage or looseness.
Test the machine’s calibration using a dial indicator.
Monthly Maintenance
Clean or replace filters in the coolant and lubrication systems.
Check electrical connections and ensure they are secure.
Perform a full system diagnostic to identify potential issues.
Annual Maintenance
Schedule a professional inspection to assess the machine’s overall condition.
Replace worn-out components, such as seals and bearings.
Update the CNC software to the latest version for improved performance.
By following this maintenance routine, you can minimize downtime and ensure your CNC machine operates at peak efficiency.
What Are the Basics of CNC Machine Programming?
CNC machine programming involves creating instructions that guide the machine’s movements and operations. Here’s a step-by-step guide to the basics:
Understand G-Code and M-Code: G-codes control the machine’s movements, while M-codes manage auxiliary functions like tool changes.
Create a CAD Model: Design the part using CAD software.
Generate CNC Code: Use CAM software to convert the CAD model into CNC instructions.
Set Up the Machine: Load the material, install tools, and input the CNC program.
Run a Simulation: Test the program virtually to identify errors or collisions.
Execute the Program: Start the machining process and monitor for accuracy.
Mastering these basics is crucial for efficient and accurate CNC machining.
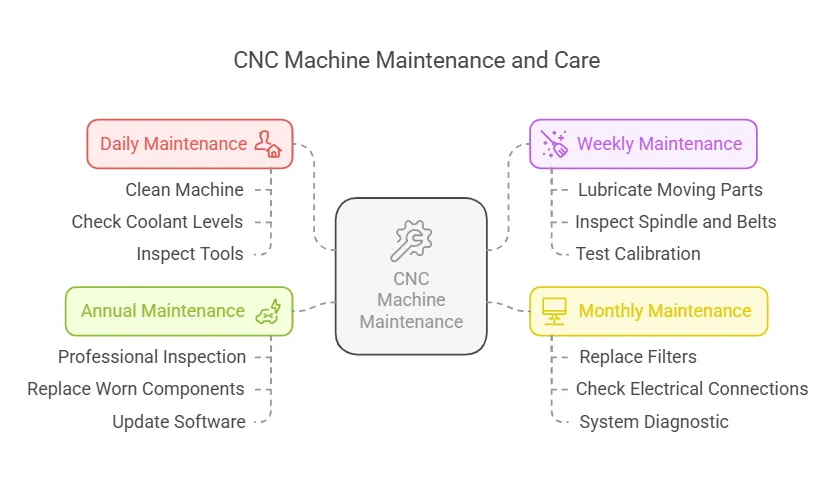
What Are Advanced CNC Machining Techniques?
Advanced CNC machining techniques enhance precision, efficiency, and capabilities. Some key techniques include:
High-Speed Machining (HSM): Uses higher spindle speeds and feed rates to reduce machining time and improve surface finish.
5-Axis Machining: Allows the cutting tool to move along five axes simultaneously, enabling complex geometries.
Micromachining: Produces extremely small parts with tight tolerances, often used in medical and electronics industries.
Adaptive Machining: Adjusts cutting parameters in real-time based on sensor feedback to optimize performance.
Additive and Subtractive Hybrid Machining: Combines 3D printing (additive) with traditional CNC machining (subtractive) for innovative part production.
By adopting these advanced techniques, manufacturers can tackle more complex projects and improve overall productivity.