What is HAAS Machining?
HAAS machining refers to the use of CNC (Computer Numerical Control) machines manufactured by HAAS Automation, Inc., a leading American machine tool builder. HAAS machines are renowned for their precision, reliability, and versatility in manufacturing processes. These machines are used to cut, shape, and fabricate materials such as metal, plastic, and wood with high accuracy. HAAS machining is widely adopted in industries like aerospace, automotive, and medical device manufacturing due to its ability to produce complex parts efficiently.
How Does the HAAS Machine Product Structure and Workflow Operate?
The product structure of a HAAS machine typically includes the following components
Control Panel: The interface where operators input commands and monitor the machining process.
Spindle: The rotating component that holds cutting tools and performs the actual machining.
Tool Changer: Automatically swaps tools during the machining process to enable multi-operation tasks.
Worktable: The surface where the material is secured for machining.
Coolant System: Maintains optimal temperature and removes debris during cutting.
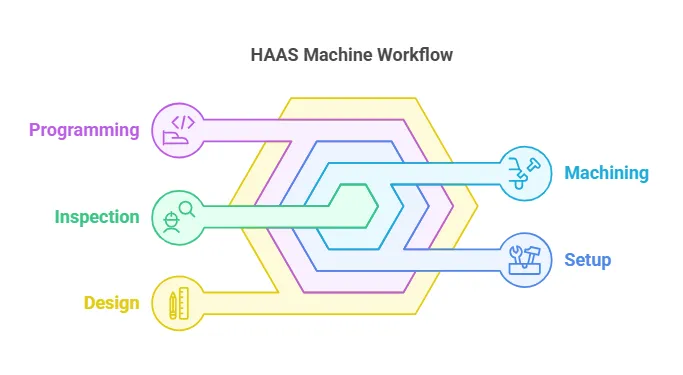
The workflow of a HAAS machine involves the following steps
Design: Create a CAD (Computer-Aided Design) model of the part to be machined.
Programming: Convert the CAD model into CNC code using CAM (Computer-Aided Manufacturing) software.
Setup: Load the material onto the worktable and install the required tools.
Machining: The machine follows the programmed instructions to cut and shape the material.
Inspection: Verify the finished part for accuracy and quality.
What is the Working Principle of HAAS Machines?
HAAS machines operate on the principle of CNC technology, which involves the following key processes:
Input: The operator uploads a CNC program containing instructions for the machining process.
Interpretation: The machine’s control unit interprets the program and converts it into electrical signals.
Movement: Servo motors drive the machine’s axes (X, Y, Z) to position the cutting tool accurately.
Cutting: The spindle rotates at high speeds, and the cutting tool removes material according to the programmed design.
Feedback: Sensors monitor the process and provide real-time feedback to ensure precision.
This automated process ensures consistent quality and reduces human error, making HAAS machines ideal for high-volume production.
What Are the Applications of HAAS CNC Machines?
HAAS CNC machines are versatile and used across various industries for different applications, including:
Aerospace: Manufacturing precision components like turbine blades and engine parts.
Automotive: Producing engine blocks, transmission parts, and custom fittings.
Medical: Creating surgical instruments, implants, and prosthetics with high accuracy.
Electronics: Machining enclosures, heat sinks, and connectors.
Prototyping: Developing prototypes for new products quickly and cost-effectively.
Their ability to handle complex geometries and tight tolerances makes HAAS machines indispensable in modern manufacturing.
How to Optimize the HAAS Machine Work Environment?
To ensure optimal performance and longevity of HAAS machines, the work environment should be carefully managed. Here’s how:
Temperature Control: Maintain a stable temperature to prevent thermal expansion and contraction of machine components.
Cleanliness: Regularly clean the machine and work area to avoid debris buildup, which can affect precision.
Vibration Reduction: Install the machine on a stable surface to minimize vibrations during operation.
Proper Ventilation: Ensure adequate airflow to prevent overheating of the machine and coolant system.
Regular Maintenance: Follow a maintenance schedule to inspect and replace worn-out parts.
How Does Product Testing and Quality Control Work in HAAS Machines?
Product testing and quality control are critical aspects of HAAS machining to ensure precision and reliability. HAAS machines undergo rigorous testing during production and before delivery to customers. Here’s how the process works:
Component Testing: Each part of the machine, such as the spindle, motors, and control panel, is tested individually for performance and durability.
Assembly Testing: After assembly, the machine is run through a series of operational tests to ensure all components work together seamlessly.
Accuracy Checks: Precision tests are conducted using laser measurement tools to verify the machine’s ability to meet tight tolerances.
Software Validation: The CNC software is tested to ensure it interprets and executes commands accurately.
Final Inspection: Before shipping, the machine undergoes a final inspection to confirm it meets HAAS’s quality standards.
This thorough testing process ensures that every HAAS machine delivers consistent performance and meets industry requirements.
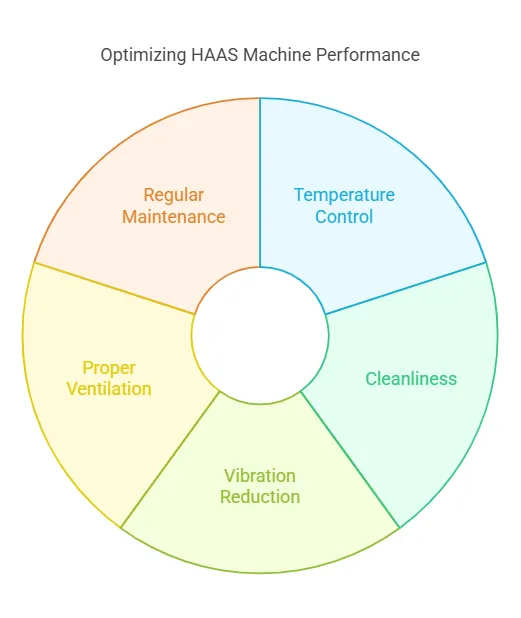
How to Maintain and Care for HAAS CNC Machines?
Proper maintenance and care are essential to keep HAAS CNC machines running efficiently and extend their lifespan. Follow these steps for effective maintenance:
Daily Maintenance:
Clean the machine and remove debris from the worktable and tool changer.
Check coolant levels and top up if necessary.
Inspect tools for wear and replace them as needed.
Weekly Maintenance:
Lubricate moving parts to reduce friction and prevent wear.
Inspect the spindle and belts for signs of damage or looseness.
Test the machine’s calibration using a dial indicator.
Monthly Maintenance:
Clean or replace filters in the coolant and lubrication systems.
Check electrical connections and ensure they are secure.
Perform a full system diagnostic to identify potential issues.
Annual Maintenance:
Schedule a professional inspection to assess the machine’s overall condition.
Replace worn-out components, such as seals and bearings.
Update the CNC software to the latest version for improved performance.
By following this maintenance routine, you can minimize downtime and ensure your HAAS machine operates at peak efficiency.
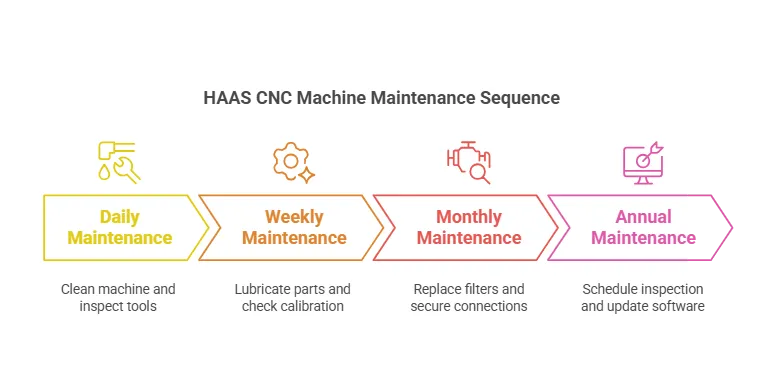
What Precautions Should Be Taken for Safe Use of HAAS Machines?
Safety is paramount when operating HAAS machines. Here are key precautions to follow:
Training: Ensure operators are fully trained in using the machine and understand safety protocols.
Personal Protective Equipment (PPE): Wear safety glasses, gloves, and ear protection to prevent injuries.
Machine Inspection: Check the machine for any visible damage or issues before starting.
Secure Workpieces: Properly clamp materials to the worktable to prevent movement during machining.
Emergency Stop: Familiarize yourself with the location and operation of the emergency stop button.
Avoid Loose Clothing: Ensure clothing and accessories do not get caught in moving parts.
Regular Maintenance: Keep the machine in good condition to avoid malfunctions that could lead to accidents.
Adhering to these precautions reduces the risk of accidents and ensures a safe working environment.
What Are the Benefits of HAAS Machines in Modern Manufacturing?
HAAS machines offer numerous advantages that make them a preferred choice in modern manufacturing:
Precision: HAAS machines deliver high accuracy, enabling the production of complex parts with tight tolerances.
Versatility: They can handle a wide range of materials, including metals, plastics, and composites.
Efficiency: Automated tool changers and advanced software reduce setup and machining time.
Reliability: HAAS machines are known for their durability and consistent performance.
Cost-Effectiveness: Their competitive pricing and low maintenance costs make them accessible to small and large manufacturers alike.
User-Friendly Interface: The intuitive control panel simplifies operation and reduces the learning curve for operators.
These benefits make HAAS machines a valuable asset in industries such as aerospace, automotive, and medical device manufacturing.
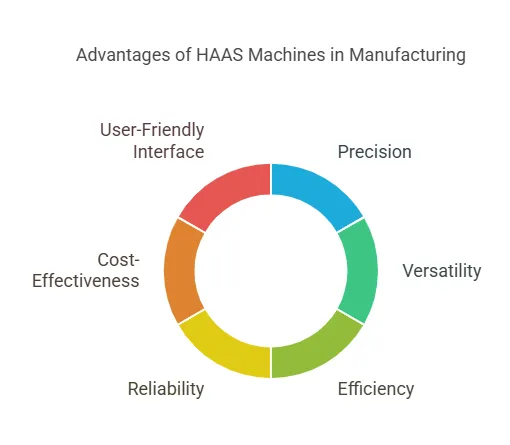
How Can HAAS Machines Be Upgraded and Customized for Specialized Needs?
HAAS machines can be upgraded and customized to meet specific manufacturing requirements. Here’s how:
Software Upgrades: Install the latest CNC software to access new features and improve performance.
Tooling Options: Add specialized tools, such as high-speed spindles or multi-axis heads, to expand machining capabilities.
Automation Integration: Connect the machine to robotic arms or conveyor systems for automated loading and unloading.
Coolant Systems: Upgrade to high-pressure coolant systems for better chip removal and tool life.
Custom Fixtures: Design and install custom workholding fixtures to accommodate unique part geometries.
Enhanced Sensors: Add advanced sensors for real-time monitoring and feedback during machining.