Milling technology is a common machining process, it enables high-precision material removal and machining of complex geometries for the production of demanding, high-quality parts. For example, many critical components in the aerospace, medical device and automotive industries rely on milling technology to ensure accuracy and performance. To improve a country’s comprehensive national strength and status need to vigorously develop advanced manufacturing technology with CNC technology as the main core, CNC milling processing is one of the important links.
Custom CNC mill is to use computer numerical control (CNC) technology to perform precise milling operations tailored to specific customer requirements. Customization can include: Material Selection, Design Specifications,Tooling and Fixtures, Precision and Tolerance, Surface Finishing.
Aluminum is one of the most widely used materials in CNC milling due to its unique combination of properties that make it ideal for various applications.Aluminum’s lightweight characteristics make it popular even today. For example, in automotive engines, it helps to significantly reduce vehicle weight and save fuel, and in the aerospace industry, aluminum is often used in aerospace prototypes because of its ease of handling. Aluminum metal will always be regarded as the material that will “make the dream of flight come true”!
Definition and Importance of Custom Services
In the hardware industry, custom service refers to the process of customizing various parts according to the specific needs of customers through precision machining technology such as CNC milling. Custom service ensures that each part produced can meet specific dimensions, tolerances, materials, and functional requirements. Custom services can meet the specific needs of customers, respond to market changes, enhance product competitiveness, increase added value…
The Processing Advantages of Aluminum Material
- Light weight but high strength-to-weight ratio–Aluminum’s density is only about one-third that of steel, so machined parts are lighter in weight, making it suitable for aerospace, automotive, electronic equipment… Light weight helps improve equipment performance and reduce energy consumption and costs. But it has a high strength to density ratio, especially after alloying treatment.
- Accessibility–Aluminum has good accessibility, and its lower hardness and density make it easier to cut during CNC milling. Aluminum is both malleable and ductile.
- Excellent thermal performance–Aluminum has a high degree of thermal conductivity and can quickly dissipate the heat generated during processing.
- Corrosion resistance–Aluminum tends to form a dense film of aluminum oxide in air, providing good corrosion resistance.
- Better surface finish–Aluminum achieves a good surface finish after machining and is easily accessible for subsequent surface treatments. It is suitable for products that require an aesthetic appearance.
- Easier to recycle–Aluminum is a recyclable metal with high recycling value.
Physical Properties of Aluminum Material and Adaptability to CNC Milling
Aluminum’s physical properties, including Light weight but high strength-to-weight ratio, accessibility, excellent thermal performance, corrosion resistance, better surface finish, easier to recycle and so on, make it an ideal material for CNC milling. Aluminum’s softness and low hardness help to shorten cycle times and reduce the wear and tear on cutting tools. Aluminum’s thermal conductivity helps dissipate heat generated during milling, reducing the risk of thermal distortion and maintaining dimensional precision.
Diversified Applications of Aluminum Material in Modern Manufacturing
- Aerospace–The lightweight nature of aluminum makes it ideal for structural components such as fuselages, wings and landing gear. Aluminum alloys are used to make the housings and structural components of some engines, providing stable performance at high temperatures and pressures.
- Automotive industry–Aluminum is used in the manufacture of automobile bodies, doors, hoods, and other components to help reduce overall vehicle weight, increase fuel efficiency.
- Electronics–Aluminum is used to make heat sinks for electronic equipment, such as computer processor heat sinks and LED lamp heat sinks, which have good thermal conductivity and can efficiently dissipate heat.
- Building and infrastructure–Building envelope systems: Aluminum alloys are used to manufacture building envelope panels, window frames and door frames, providing corrosion resistance. Aluminum roof panels and guttering offer excellent weather and corrosion resistance, making them stable in a variety of climatic conditions.
- Packaging–Aluminum foil is widely used for packaging of food and pharmaceutical products. Due to its excellent airtightness, moisture barrier and corrosion resistance, it can effectively protect the quality of the products and extend the shelf life.
Process Flow of Custom CNC Mill
- Communicate with the customer to get the target drawings and specifications, including dimensions, tolerances, material properties and surface finish.
- Use computer-aided design (CAD) software to create a 3D model of the part.
- Use computer-aided manufacturing (CAM) software to convert CAD models into toolpaths.
- Select the appropriate aluminum alloy based on the specific application.
- Obtain and prepare aluminum stock material.
- Set CNC Machine, Install appropriate cutting tools
- Initial Roughing, use larger cutting tools and higher feed rates for this step to quickly shape the part. This may include slotting, grooving, and contouring to achieve intermediate dimensions.
- Perform finishing operations to achieve final dimensions, tolerances, and make surface finish like anodizing, painting, or polishing…
- Do quality Inspection to ensure that it meets design specifications and tolerances. Do Surface inspections to check for any imperfections, burrs or defects.
- Then do cleaning and make final adjustments.
- Packaging and Delivery.
Parameter Selection and Optimization in Aluminum Material Processing
In CNC milling machining of aluminum materials, the selection and optimization of machining parameters are critical to obtaining high-quality parts, maximizing tool life and ensuring efficient production. Key influences on the milling process include the selection of the CNC milling machine, the determination of the tools and materials to be machined, and the control of process parameters such as cutting speed, feed, and depth of cut.
Methods for Achieving High Precision Processing
Achieving high precision in CNC milling is a process of all-round improvement, starting from the initial design stage and extending to the final inspection. Through the use of advanced tools, optimization of each step of the process, careful selection of processing parameters, management of temperature and vibration, and the use of precision measurement technology, rigorous quality testing, it is possible to ensure product consistency and achieve high precision.
Technical Challenges and Solutions of Custom CNC Mill
Machining more complex geometric is a challenge.
Solution: machining capacity can be increased by using 5-axis or multi-axis linkage, using advanced CAM software to optimize tool paths.
Balancing Efficient Tool Selection and Material Removal Rate.
Solution: First of all, we must choose high-quality tool materials, improve from the source. For example, the choice of carbide tools, in aluminum processing, TiB2 coated tools can effectively reduce the problem of material sticking and reduce material waste. And also improve the monitoring system, real-time monitoring of tool status,control the life and wear degree of the tool.
Surface Quality Control and Post-processing.
Solution: The surface quality is one of the important indexes to measure the quality of parts. By optimizing the cutting parameters, the Vc, Fz and ap can be adjusted comprehensively to get a better surface finish. Post-processing after surface treatment is also very important, there are a lot of surface treatment methods, such as Anodizing, Polishing, Electroplating, Powder Coating, Painting, Nickel Plating, any Zinc Plating, Zinc Nickel plating, Dacromet, Chromate Conversion Coating, Heat Treatment. According to different materials, parts of different applications, choose the appropriate way.
CNC Industry Case Analysis
Application of Custom CNC Mill of Aluminum Materials in the Aerospace Field: The Boeing 787 uses a large number of aluminum alloys to manufacture fuselage frames, ribs and other structural components, and CNC milling machines can efficiently process complex geometric shapes, can process large-size parts, and can produce complex aerospace parts more accurately and efficiently.
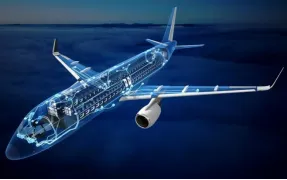
Advantages of Lightweight Aluminum Materials in the Automotive Industry: Lightweight Aluminum Materials have low density, high strength, good corrosion resistance, making it a clear advantage in the automotive industry. The high strength of aluminum makes many manufacturers use aluminum bodies to improve vehicle handling and driving experience, because aluminum has a better surface treatment, the body made of it also has a better appearance. For example, Audi A8 luxury sedan features an all-aluminum body structure (called Audi Space Frame), it is the world’s first mass-produced all-aluminum body sedan. The aluminum body makes the Audi A8 about 40% lighter than the traditional steel body, improves fuel efficiency, and significantly improves handling and acceleration.

Precision Processing Requirements in the Manufacturing of Electronic Products: High precision is the priority, the material should have electrical conductivity, high temperature resistance, corrosion resistance, due to the small size of the electronic components, the need for miniaturization, while welding and connection technology is very important, processing precision electronic products also need to ensure a dust-free environment.