5-axis CNC machining is a revolutionary manufacturing technology that enables the production of highly complex and precise components. This article explores the intricacies of complex 5-axis CNC machining and high-precision 5-axis CNC machining, explaining their applications, benefits, and how they work. Whether you’re in aerospace, medical, or automotive industries, this guide will help you understand why 5-axis CNC machining is a game-changer for modern manufacturing.
What is 5-Axis CNC Machining?
5-axis CNC machining refers to the use of computer numerical control (CNC) machines that can move a tool or workpiece along five different axes simultaneously. These axes include the three linear axes (X, Y, Z) and two rotational axes (A and B or C). This capability allows for the creation of highly complex geometries and precise components that are difficult or impossible to achieve with traditional 3-axis machining.
Key Features of 5-Axis CNC Machining:
Multi-directional machining: The tool can approach the workpiece from any angle.
Reduced setups: Complex parts can be completed in a single setup, saving time and reducing errors.
Enhanced precision: The ability to rotate the workpiece ensures tighter tolerances and better surface finishes.
Why Choose 5-Axis CNC Machining?
5-axis CNC machining offers unparalleled advantages for industries that demand high complexity and precision. Here’s why it’s a preferred choice:
1. Complex Geometry Capabilities
Ideal for parts with intricate designs, such as turbine blades, impellers, and medical implants.
Enables undercutting and deep cavity machining, which are challenging for 3-axis machines.
2. High Precision and Accuracy
Achieves tight tolerances (up to ±0.0001 inches) and superior surface finishes.
Reduces human error by automating complex machining processes.
3. Efficiency and Cost-Effectiveness
Fewer setups mean faster production times and lower labor costs.
Minimizes material waste by optimizing tool paths.
4. Versatility Across Industries
Used in aerospace, automotive, medical, energy, and defense sectors.
Suitable for machining a wide range of materials, including metals, plastics, and composites.
How Does 5-Axis CNC Machining Work?
Understanding the mechanics of 5-axis CNC machining is essential to appreciate its capabilities. Here’s a step-by-step breakdown:
Step 1: Designing the Part
Engineers create a 3D CAD model of the part using software like SolidWorks or AutoCAD.
The design includes all geometric details, tolerances, and surface finish requirements.
Step 2: Generating Tool Paths
CAM (Computer-Aided Manufacturing) software converts the CAD model into tool paths.
The software determines the optimal tool movements, cutting speeds, and feed rates.
Step 3: Setting Up the Machine
The workpiece is securely clamped onto the machine’s rotary table.
Tools are loaded into the machine’s spindle, and the program is uploaded.
Step 4: Machining the Part
The machine moves the tool and workpiece along five axes simultaneously.
Complex features like curves, angles, and undercuts are machined in a single setup.
Step 5: Quality Inspection
The finished part is inspected using CMM (Coordinate Measuring Machine) or other precision tools.
Measurements are compared against the design specifications to ensure accuracy.
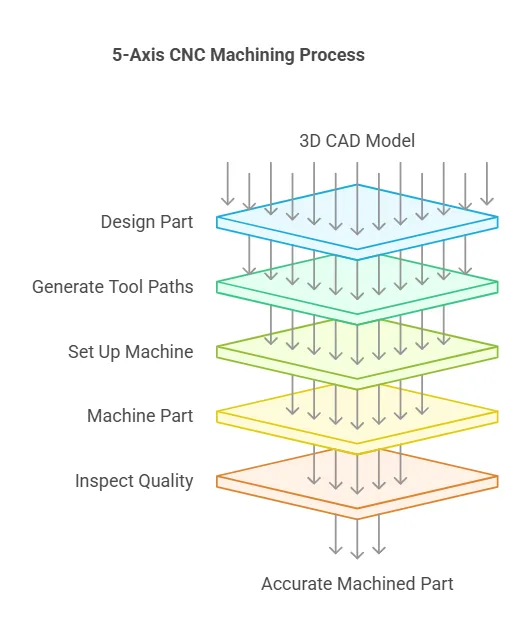
Can 5-Axis CNC Machining Handle Both Complexity and Precision?
Absolutely! 5-axis CNC machining is uniquely capable of combining complexity and precision. Here’s how:
Complex 5-Axis CNC Machining
Applications: Aerospace components (e.g., turbine blades), automotive prototypes, and artistic sculptures.
Challenges: Requires advanced programming and skilled operators to manage intricate tool paths.
High-Precision 5-Axis CNC Machining
Applications: Medical devices (e.g., implants), optical components, and micro-machined parts.
Challenges: Demands ultra-precise machines, high-quality tools, and controlled environments to minimize vibrations and thermal distortions.
Combining Complexity and Precision
Example: A turbine blade for a jet engine requires complex aerodynamic shapes and micron-level precision.
Solution: 5-axis CNC machines can achieve both by using advanced CAM software and high-performance cutting tools.
What is the Difference Between Complex 5-Axis CNC Machining and High-Precision 5-Axis CNC Machining?
While both complex and high-precision 5-axis CNC machining utilize the same 5-axis technology, their focus and applications differ significantly:
Complex 5-Axis CNC Machining:
Focuses on creating intricate geometries and shapes that are difficult to achieve with traditional machining methods.
Examples include turbine blades, impellers, and molds with deep cavities.
Prioritizes flexibility and the ability to machine from multiple angles.
High-Precision 5-Axis CNC Machining:
Focuses on achieving extremely tight tolerances and superior surface finishes.
Examples include medical implants, optical lenses, and aerospace components.
Prioritizes accuracy, repeatability, and minimizing errors.
In summary, complex 5-axis machining is about geometric complexity, while high-precision 5-axis machining is about dimensional accuracy.
Workflow Optimization in High-Precision 5-Axis CNC Machining
Optimizing the workflow in high-precision 5-axis CNC machining is crucial for achieving consistent results and maximizing efficiency. Here’s how to do it:
Advanced CAM Software:
Use software with simulation capabilities to detect collisions and optimize tool paths.
Ensure the software supports high-speed machining (HSM) for smoother finishes.
Tool Management:
Use high-quality, wear-resistant tools to maintain precision over long runs.
Implement automatic tool changers to reduce downtime.
Machine Calibration:
Regularly calibrate the machine to ensure accuracy.
Use laser calibration tools to verify positional accuracy.
Environmental Control:
Maintain a stable temperature and humidity level to prevent thermal expansion.
Isolate the machine from vibrations and external disturbances.
Operator Training:
Train operators to handle high-precision tasks and troubleshoot issues.
Encourage continuous learning to keep up with technological advancements.
The Working Principle Behind the Efficiency of Complex 5-Axis CNC Machining
The efficiency of complex 5-axis CNC machining lies in its ability to perform multiple operations in a single setup. Here’s how it works:
Simultaneous 5-Axis Movement:
The machine can move the tool and workpiece along five axes at the same time, reducing the need for repositioning.
Reduced Setups:
Complex parts can be machined in one go, eliminating errors caused by multiple setups.
Optimized Tool Paths:
Advanced CAM software calculates the most efficient tool paths, minimizing idle time and tool wear.
Versatile Tool Access:
The ability to tilt and rotate the tool allows for better access to hard-to-reach areas, such as deep cavities and undercuts.
Advanced Product Testing Methods for Complex 5-Axis CNC-Machined Parts
Ensuring the quality of complex 5-axis CNC-machined parts requires advanced testing methods. Here are some techniques:
Coordinate Measuring Machine (CMM):
Uses a probe to measure the physical dimensions of the part against the CAD model.
Laser Scanning:
Captures the surface geometry of the part for comparison with the design specifications.
Surface Roughness Testing:
Measures the surface finish to ensure it meets the required standards.
Non-Destructive Testing (NDT):
Techniques like ultrasonic testing and X-ray inspection detect internal defects without damaging the part.
Functional Testing:
Tests the part under real-world conditions to verify its performance.
Critical Usage Precautions for Complex 5-Axis CNC Machines
Using complex 5-axis CNC machines requires careful attention to safety and operational guidelines. Here are some precautions:
Proper Training:
Ensure operators are trained to handle the machines complexity.
Regular Maintenance:
Follow the manufacturers maintenance schedule to prevent breakdowns.
Tool Inspection:
Check tools for wear and damage before each operation.
Workpiece Securing:
Ensure the workpiece is securely clamped to prevent movement during machining.
Emergency Protocols:
Have clear procedures for handling emergencies, such as tool breakage or power failure.
Maintenance and Care Tips to Extend the Lifespan of High-Precision 5-Axis CNC Machining Equipment
Proper maintenance is essential for keeping high-precision 5-axis CNC machines in top condition. Here are some tips:
Daily Cleaning:
Remove chips and debris from the machine to prevent buildup.
Lubrication:
Regularly lubricate moving parts to reduce friction and wear.
Calibration:
Periodically calibrate the machine to maintain accuracy.
Software Updates:
Keep the machine’s software up to date to benefit from the latest features and bug fixes.
Professional Servicing:
Schedule regular servicing by qualified technicians to address potential issues early.
What Industries Benefit from 5-Axis CNC Machining?
5-axis CNC machining is a cornerstone of modern manufacturing. Here are some industries that rely on it:
1. Aerospace
Applications: Turbine blades, engine components, and structural parts.
Benefits: Lightweight designs, high strength, and tight tolerances.
2. Medical
Applications: Implants, surgical instruments, and prosthetics.
Benefits: Biocompatible materials, intricate designs, and high precision.
3. Automotive
Applications: Prototypes, engine blocks, and custom parts.
Benefits: Faster production, reduced weight, and improved performance.
4. Energy
Applications: Wind turbine components, oil and gas parts.
Benefits: Durability, efficiency, and resistance to extreme conditions.
5. Defense
Applications: Weapon systems, armored vehicles, and communication devices.
Benefits: High reliability, precision, and security.
How to Choose the Right 5-Axis CNC Machine?
Selecting the right 5-axis CNC machine depends on your specific needs. Here’s a checklist to help you decide:
1. Machine Type
Table/Table: The workpiece rotates on two axes, ideal for small parts.
Head/Head: The tool rotates on two axes, suitable for large parts.
Table/Head: A combination of both, offering maximum flexibility.
2. Accuracy and Repeatability
Look for machines with high positional accuracy (e.g., ±0.0001 inches).
Ensure the machine can maintain precision over long production runs.
3. Software Compatibility
Choose a machine that supports industry-standard CAD/CAM software.
Ensure the software can handle complex tool paths and simulations.
4. Material Compatibility
Check if the machine can handle the materials you work with (e.g., titanium, aluminum, composites).
Consider the machine’s power and rigidity for heavy-duty machining.
5. Budget and ROI
Balance the initial cost with long-term benefits like reduced labor and material savings.
Consider maintenance costs and the availability of technical support.
1. What is the difference between 3-axis and 5-axis CNC machining?
3-axis machines move along X, Y, and Z axes, while 5-axis machines add two rotational axes, enabling more complex and precise machining.
2. Can 5-axis CNC machines work with all materials?
Yes, 5-axis CNC machines can handle a wide range of materials, including metals, plastics, and composites, depending on the machine’s capabilities.
3. How does 5-axis CNC machining improve efficiency?
By reducing the number of setups, minimizing tool changes, and optimizing tool paths, 5-axis machining significantly speeds up production.
4. Is 5-axis CNC machining suitable for small businesses?
While the initial investment is high, small businesses can benefit from 5-axis machining if they produce complex or high-precision parts.
5. What are the challenges of 5-axis CNC machining?
Challenges include high costs, the need for skilled operators, and the complexity of programming and setup.