According to the latest industry data, the global computer numerical control (CNC) machine tools market is estimated to be $84.6 billion in 2024 and is likely to grow at a CAGR of 8.4% from 2024-2030 to reach an estimated $137.3 billion by 2030. Integration of these technologies with CNC machine tools is bound to boost the market growth in the coming years.(Source: https://www.researchandmarkets.com/)
As precision manufacturing technologies continue to escalate, more and more industries are relying on CNC numerical control services to meet the demand for high accuracy and efficiency. But with a multitude of suppliers, how do you make the right choice? This article will help companies understand the key factors in choosing a supplier, taking into account the latest industry trends.
1. Assess their expertise and experience
A supplier’s experience extends beyond the number of years their business has been in operation to include their familiarity with specific industries, technical challenges and materials. Certain industries – such as aerospace, medical, automotive and electronics – have special needs that require suppliers to have unique manufacturing knowledge and exacting standards.See if the business has experience working with other companies in your industry.Prior clients from the same field can help providers offer more specialized services that address Prior clients from the same field can help providers offer more specialized services that address industry-specific problems. Experienced CNC machining partners have an in-depth understanding of a wide range of machining processes (such as milling, turning, and Swiss-turning) as well as materials (from metals to advanced composites and plastics). If you have complex parts with tight tolerances, find out if they have such precision machining capabilities and use advanced multi-axis CNC equipment for complex cutting and faster production. When choosing the right CNC service provider, it is important to examine whether their quality management system is sound. Certifications such as ISO 9001 for quality management and ISO 14001 for environmental management demonstrate their commitment to standardized practices and continuous quality management.
2. Advanced technology and equipment
The company must have the necessary services and capabilities to manufacture your product. Assess the specific equipment and machining processes required for your parts. For instance, if you need CNC turning but the provider only offers CNC milling, you won’t be able to meet your needs. Inquire about the range of CNC machining services they provide and their equipment specifications.
Additionally, consider whether they offer other machining methods and if they provide secondary operations, such as assembly or packaging. These added services can not only help you save costs by functioning as a one-stop shop, but they can also enhance the quality of your parts due to a streamlined process and a team that is familiar with the product.
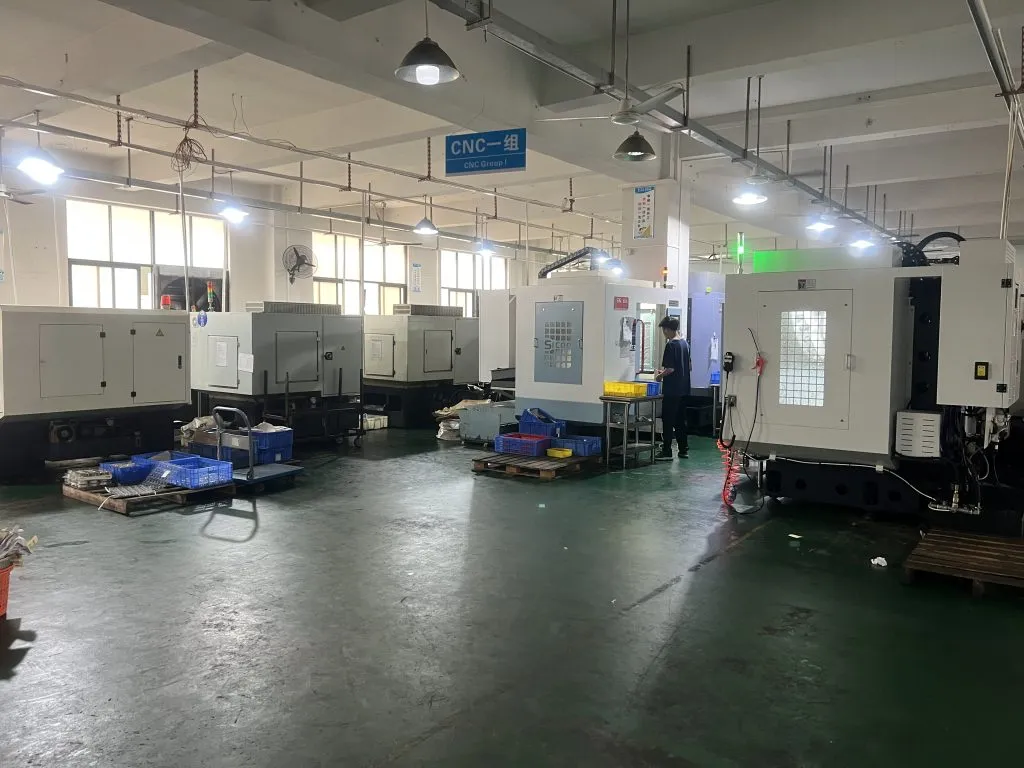
3. Diversity of materials
It is critical to understand the types of materials that a supplier can handle. Common materials include metals (such as aluminum, stainless steel, copper, and titanium), plastics (such as polycarbonate, nylon, and polypropylene), and composites. A good supplier will usually have the ability to handle a wide range of materials so you can meet the needs of different projects in one location. A supplier’s material selection, specification certification, sourcing channels, processing capabilities, and innovation will have a direct impact on the success of your project.
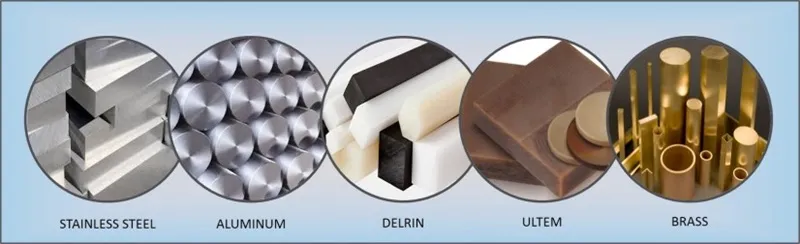
4. Lead times and service flexibility
In industries where demand fluctuates, fast delivery and flexibility to adjust are advantages that suppliers cannot afford to overlook. Choosing the best CNC machining service depends on finding a delivery cycle that fits your needs. Ask about their average turnaround time and make sure it matches your operational needs. Remember to factor in transportation time.
5. Review Customer Support and Communication
Even the best manufacturer won’t help you much if you can’t get in touch with them. Timely response is the foundation of good customer support. When you ask a vendor for a quote, project status, or technical details, the vendor’s responsiveness reflects their level of professionalism and customer focus. Evaluate the communication channels offered by suppliers. Modern CNC machining suppliers usually keep in touch with their customers in a variety of ways, such as email, phone calls, and various social media platforms. Make sure you can easily reach them through your preferred method. Find out if the supplier has a mechanism for collecting customer feedback. For example, regular customer satisfaction surveys, program evaluations, or callbacks can help them improve the quality of their services.
6. Quality inspection and accuracy assurance
Quality inspection and precision assurance are important factors that should not be overlooked when choosing a CNC machining service provider. By evaluating a supplier’s quality management system, inspection processes, testing equipment, employee skills, traceability, customer feedback mechanisms, and quality assurance protocols, you can better determine whether they can meet your quality requirements. Ensuring that you choose a supplier that emphasizes quality control will help improve the marketability of your products and customer satisfaction. This includes finding out if the supplier has implemented a comprehensive quality management system, evaluating the supplier’s quality inspection process, and assessing the availability of modern testing equipment and technology.
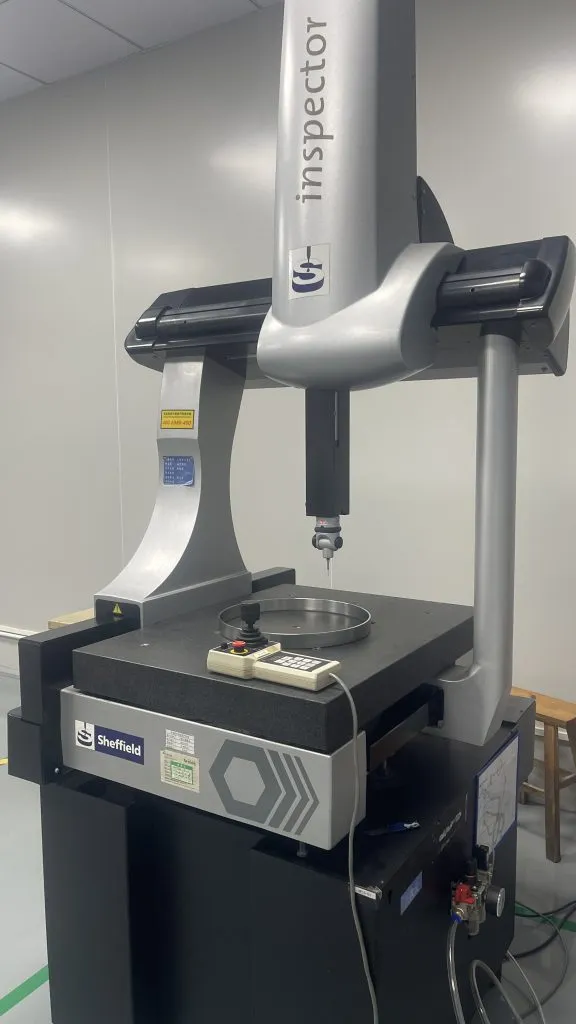
7. See How Yumei Hardware Does CNC Machining
Yumei Hardware has over 150 state-of-the-art CNC machines, including several high-precision machining machines with multi-axis control. With these machines, we are able to ensure that parts are accurate to the micron level, meeting or exceeding the complex needs of our customers.Yumei Hardware is ISO 9001:2015, ISO 14001:2015, and IATF 16949:2016 certified, and follows a strict standardized manufacturing process that ensures that every step of the process, from raw material to finished product, complies with industry standards. This rigorous quality system has enabled us to capture 25% and 30% market share in the European and North American markets. We support customized production with no minimum order quantities, and are flexible from small trial runs to large deliveries, providing maximum support for our customers’ production schedules. Customer satisfaction is always our No. 1 goal, and we support it by offering a wide selection of materials and sophisticated equipment. Our expertise spans many industries, including Automotive, Medical Device, electronics, aerospace…As your one-stop shop, we’re proud to create new, custom parts, hard-to-find replacements and other components your business might need.