What is 4-axis CNC Machining for Intricate Parts?
4-axis CNC machining refers to a manufacturing process where computer numerical control (CNC) machines operate along four different axes simultaneously to create complex and intricate parts. Unlike traditional 3-axis machines that move along the X, Y, and Z axes, 4-axis machines add a rotational axis (typically the A-axis), allowing the workpiece to be rotated during machining. This capability enables the production of highly detailed and geometrically complex components that would be difficult or impossible to achieve with fewer axes. Industries such as aerospace, automotive, and medical devices often rely on 4-axis CNC machining for precision parts like turbine blades, engine components, and surgical instruments.
Why Does 4-axis CNC Machining Enhance Precision in Intricate Parts?
4-axis CNC machining significantly improves precision in intricate parts by introducing an additional axis of movement. This rotational axis allows the machine to approach the workpiece from multiple angles without requiring manual repositioning. As a result, the tool can maintain consistent contact with the material, reducing errors and ensuring tighter tolerances. Additionally, the ability to rotate the workpiece enables the creation of undercuts, curved surfaces, and complex geometries with high accuracy. This level of precision is critical for industries where even the smallest deviation can lead to part failure, such as in aerospace or medical applications.
How Does 4-axis CNC Machining Work: A Step-by-Step Guide
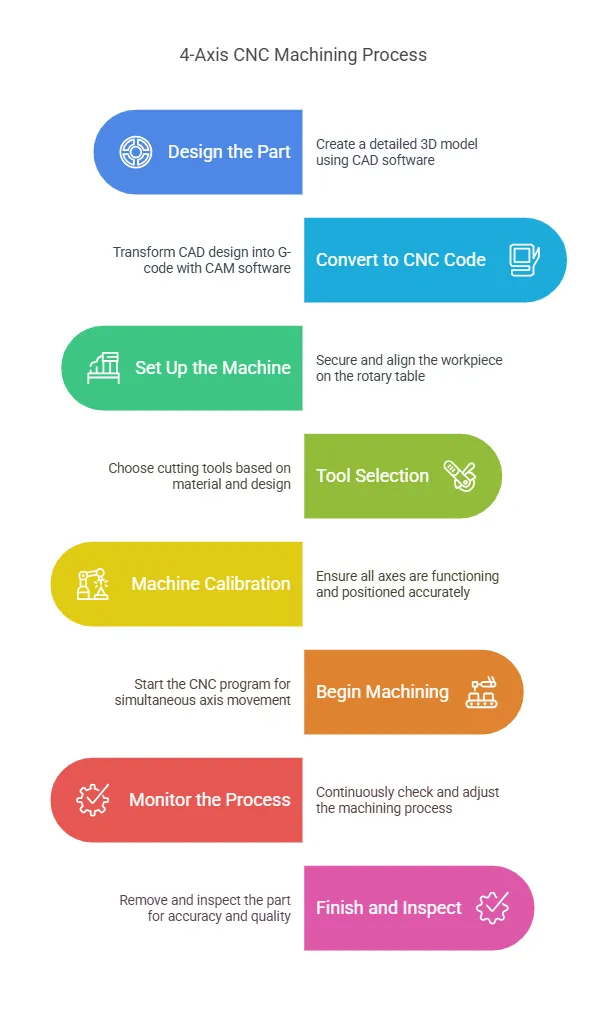
- Design the Part: Begin by creating a detailed 3D model of the part using CAD software. This model will serve as the blueprint for the machining process.
- Convert to CNC Code: Use CAM software to convert the CAD design into G-code, the language that CNC machines understand.
- Set Up the Machine: Secure the workpiece onto the 4-axis CNC machine’s rotary table, ensuring it is properly aligned.
- Tool Selection: Choose the appropriate cutting tools based on the material and design requirements.
- Machine Calibration: Calibrate the machine to ensure all axes are functioning correctly and the workpiece is positioned accurately.
- Begin Machining: Start the CNC program, allowing the machine to move along the X, Y, Z, and A axes simultaneously to shape the part.
- Monitor the Process: Continuously monitor the machining process to ensure precision and make adjustments if necessary.
- Finish and Inspect: Once machining is complete, remove the part and inspect it for accuracy and quality.
What Are the Applications of 4-axis CNC Machining in Complex Industries?
4-axis CNC machining is widely used in industries that require high precision and complex geometries. Some key applications include:
- Aerospace: Manufacturing turbine blades, engine components, and structural parts with intricate designs.
- Automotive: Producing custom engine parts, transmission components, and prototypes.
- Medical Devices: Creating surgical instruments, implants, and prosthetics with precise tolerances.
- Defense: Machining components for firearms, optics, and communication devices.
- Electronics: Fabricating housings, connectors, and heat sinks for electronic devices.
These industries benefit from the ability of 4-axis CNC machining to produce parts with complex shapes and high accuracy, ensuring optimal performance and reliability.
What Are the Advantages of 4-axis CNC Machining for Intricate and Detailed Parts?
4-axis CNC machining offers several advantages for producing intricate and detailed parts:
- Enhanced Precision: The additional rotational axis allows for more precise cuts and complex geometries.
- Reduced Setup Time: The ability to rotate the workpiece eliminates the need for manual repositioning, saving time and reducing errors.
- Improved Surface Finish: Continuous machining along multiple axes results in smoother surfaces and fewer imperfections.
- Versatility: Capable of handling a wide range of materials, including metals, plastics, and composites.
- Cost Efficiency: By reducing the need for multiple setups and minimizing material waste, 4-axis machining can lower production costs.
These benefits make 4-axis CNC machining an ideal choice for industries that demand high-quality, intricate parts.
What Are the Common Materials Used in 4-axis CNC Machining for Intricate Parts?
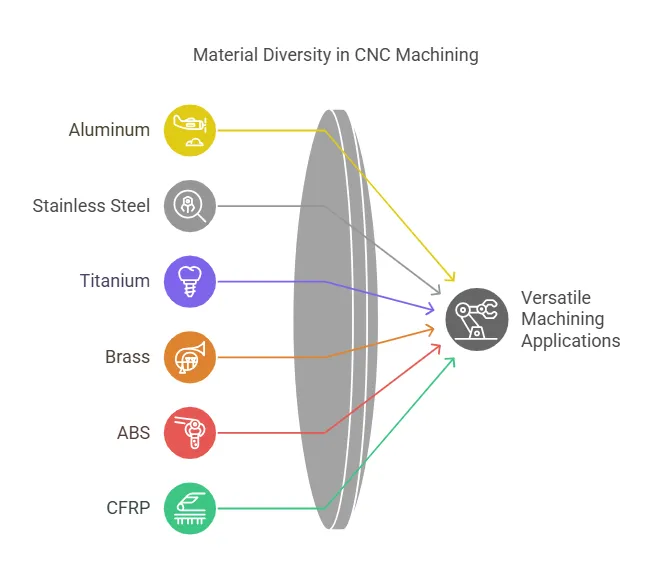
4-axis CNC machining is compatible with a wide range of materials, making it versatile for various industries. The choice of material depends on the part’s intended application, strength requirements, and environmental conditions. Common materials include:
-
Metals:
- Aluminum: Lightweight, corrosion-resistant, and easy to machine, ideal for aerospace and automotive parts.
- Stainless Steel: Durable and resistant to wear, often used in medical devices and food processing equipment.
- Titanium: High strength-to-weight ratio and biocompatibility, perfect for aerospace and medical implants.
- Brass: Excellent machinability and aesthetic appeal, commonly used for decorative components and fittings.
-
Plastics:
- ABS: Tough and impact-resistant, suitable for prototypes and consumer products.
- PEEK: High-temperature resistance and chemical stability, used in medical and aerospace applications.
- Polycarbonate: Transparent and durable, ideal for lenses and protective covers.
-
Composites:
- Carbon Fiber Reinforced Polymers (CFRP): Lightweight and strong, used in high-performance automotive and aerospace parts.
Each material has unique properties that influence the machining process, such as cutting speed, tool selection, and cooling requirements.
What Are the Key Factors Influencing the Performance of 4-axis CNC Machining?
The performance of 4-axis CNC machining depends on several critical factors:
- Machine Rigidity: A sturdy machine frame reduces vibrations, ensuring higher precision and better surface finishes.
- Tool Quality: High-quality cutting tools made from materials like carbide or diamond improve efficiency and reduce wear.
- Software Capabilities: Advanced CAM software optimizes toolpaths, minimizes errors, and enhances productivity.
- Operator Skill: Experienced operators can fine-tune machine settings and troubleshoot issues effectively.
- Coolant and Lubrication: Proper cooling and lubrication prevent overheating and extend tool life.
- Workpiece Fixturing: Secure and accurate fixturing ensures the workpiece remains stable during machining.
By addressing these factors, manufacturers can maximize the performance of their 4-axis CNC machines and achieve superior results.
What Are the Challenges in Machining Intricate Parts with 4-axis CNC?
While 4-axis CNC machining offers numerous advantages, it also presents several challenges:
- Complex Programming: Creating precise toolpaths for intricate designs requires advanced CAM software and skilled programmers.
- Tool Access: The additional axis can sometimes limit tool access to certain areas of the workpiece, requiring creative solutions.
- Material Deflection: Thin or delicate parts may bend or vibrate during machining, affecting accuracy.
- Heat Management: High-speed machining can generate heat, potentially damaging the workpiece or tools.
- Cost: The initial investment in 4-axis CNC machines and tooling can be high, especially for small-scale operations.
Overcoming these challenges often involves a combination of advanced technology, skilled personnel, and careful planning.
What Are the Product Design Considerations for 4-axis CNC Machining?
Designing parts for 4-axis CNC machining requires careful consideration to ensure manufacturability and efficiency. Key factors include:
- Geometric Complexity: Leverage the rotational axis to create undercuts, curved surfaces, and intricate details.
- Tool Accessibility: Ensure the design allows the cutting tool to reach all necessary areas without interference.
- Material Selection: Choose materials that balance performance requirements with machinability.
- Tolerances: Specify appropriate tolerances to avoid unnecessary precision that could increase costs.
- Surface Finish: Design for achievable surface finishes based on the material and machining process.
- Minimize Setup Changes: Optimize the design to reduce the need for multiple setups, saving time and reducing errors.
By incorporating these considerations, designers can create parts that are both functional and cost-effective to produce.
How to Choose the Right 4-axis CNC Machine for Your Intricate Parts
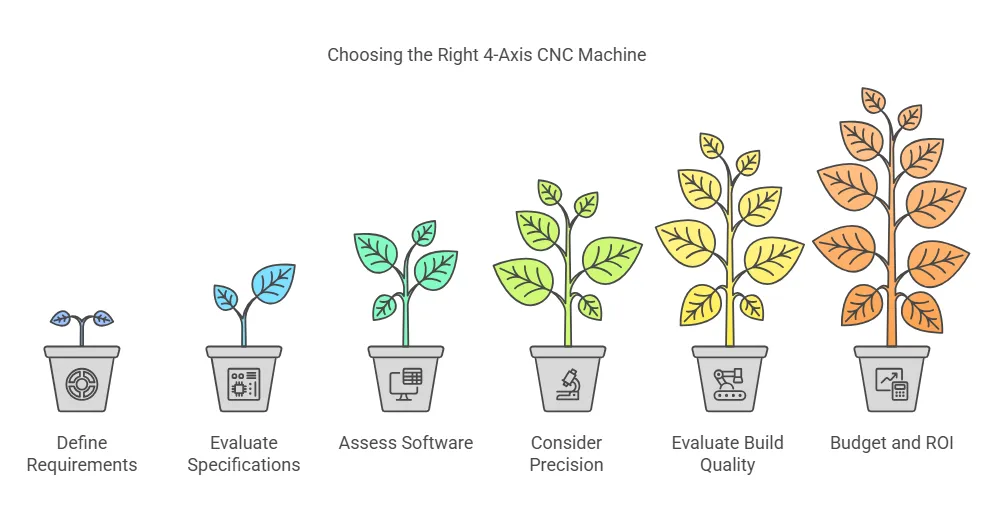
Selecting the right 4-axis CNC machine involves evaluating several factors to ensure it meets your specific needs. Follow these steps:
-
Define Your Requirements:
- Determine the size and complexity of the parts you will be machining.
- Identify the materials you will be working with.
-
Evaluate Machine Specifications:
- Check the machine’s working envelope to ensure it can accommodate your parts.
- Verify the spindle speed and power for compatibility with your materials.
-
Assess Software Compatibility:
- Ensure the machine supports the CAD/CAM software you use.
- Look for features like simulation and collision detection.
-
Consider Precision and Accuracy:
- Review the machine’s positional accuracy and repeatability.
- Check for features like automatic tool calibration and probing.
-
Evaluate Build Quality:
- Choose a machine with a rigid frame and high-quality components for durability.
- Look for reputable brands with good customer support.
-
Budget and ROI:
- Compare the initial cost with the expected return on investment.
- Factor in maintenance and operational costs.
By carefully considering these factors, you can select a 4-axis CNC machine that delivers optimal performance for your intricate parts.