At Yumei Hardware, we utilize an advanced lineup of 3-axis, 4-axis, and 5-axis milling machines.Understanding which type of machine will manufacture your parts is essential for optimizing your design. The key difference between 3-axis, 4-axis, and 5-axis machining lies in the complexity of movement between the workpiece and cutting tool. The more complex this movement, the more intricate the final geometry of the machined part can be.
This guide will explore the key differences between these machines and offer practical advice on selecting the right one for your specific needs.
Key Differences
1. 3-Axis CNC Machining
A 3-axis CNC machine tool is a computer-controlled machining system that operates along three axes (X, Y and Z). These axes represent three-dimensional space, where X and Y control horizontal motion and Z controls vertical motion. In a 3-axis CNC, the cutting tool or workpiece can be moved in all three directions to perform various machining operations such as milling, drilling and cutting. This type of CNC machine is widely used in the manufacturing industry to produce a wide variety of parts ranging from simple to moderately complex geometries. 3-axis CNC machines may require repositioning of the workpiece or cutting tool when machining highly complex parts that require multiple approach angles, which can add to machining time and complexity. However, they are relatively inexpensive, simple to operate, and can handle a wide range of materials and part geometries. They are suitable for applications such as prototyping, general-purpose machining and production of moderately complex parts.
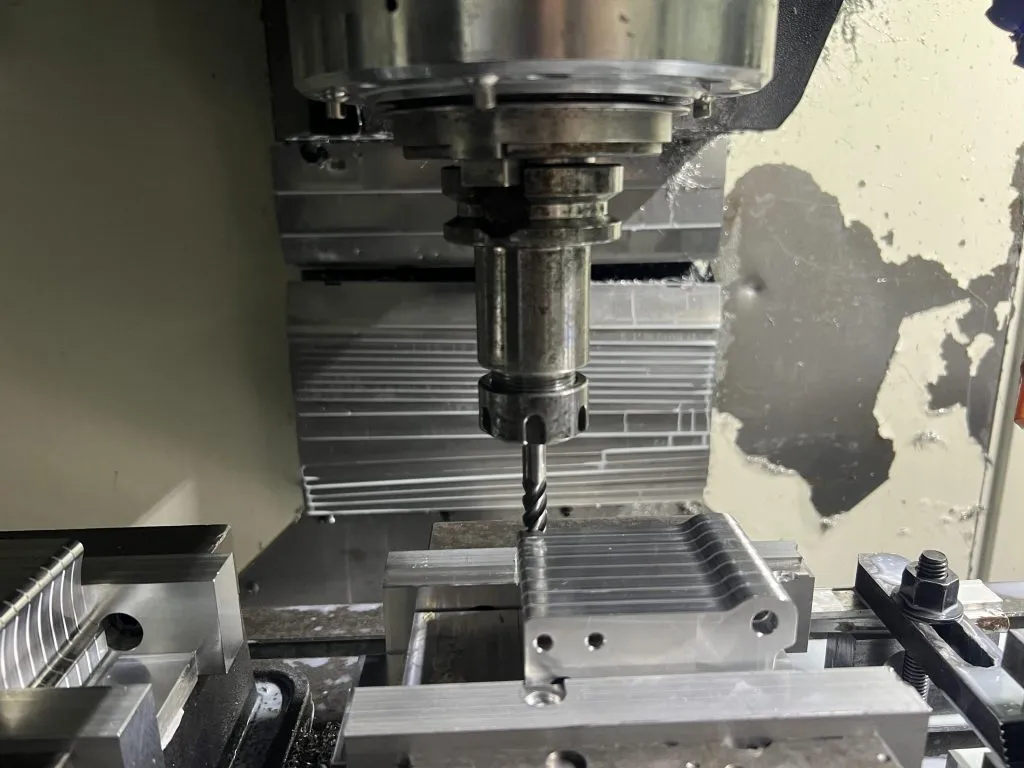
2. 4-Axis CNC Machining
A 4-axis CNC machine is a computer numerical control (CNC) machine with four motion control axes. Compared to a standard 3-axis CNC machine that moves along the X, Y, and Z axes, a 4-axis machine adds another axis of rotation, usually around the X, Y, or Z axis. This additional axis allows the machine to perform more complex machining operations and produce complex parts with greater efficiency and precision. The fourth axis of rotation allows the cutting tool to approach the workpiece from different angles, enabling operations such as indexing, contour milling and helical milling. This versatility is especially beneficial for machining cylindrical or prismatic parts with features that need to be machined from multiple angles.4 Axis CNC machine tool applications cover a wide range of industries, including aerospace, automotive, medical and mold making. They are commonly used for tasks such as engraving, carving, drilling holes at various angles and machining complex contours.
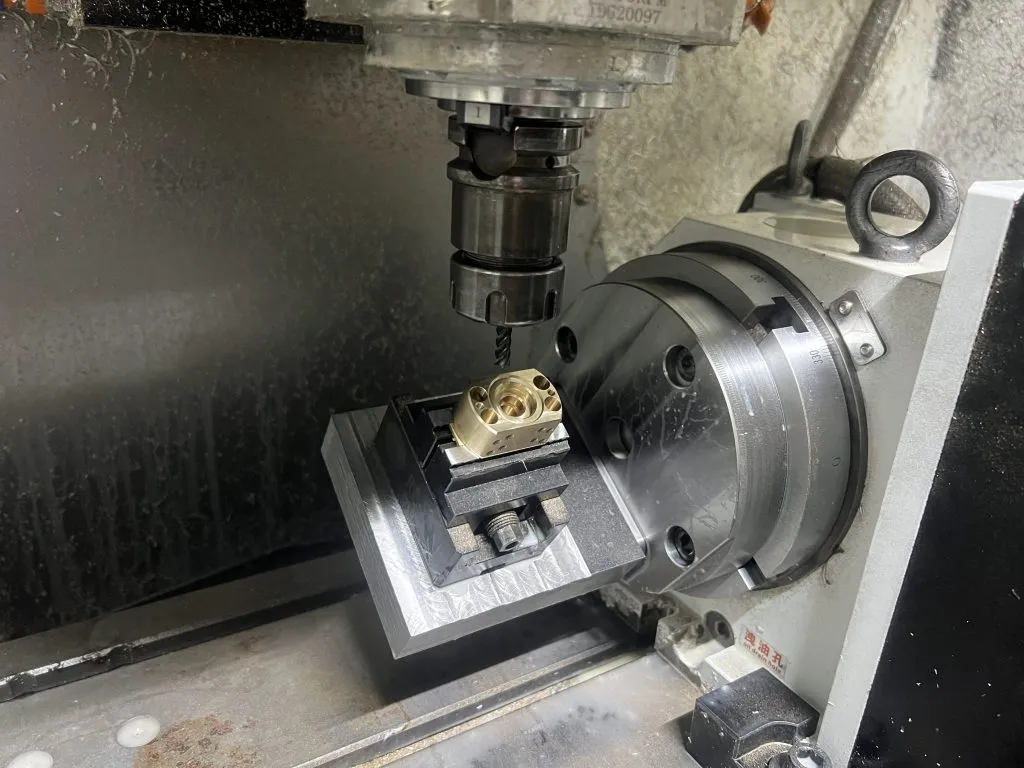
3. 5-Axis CNC Machining
5-axis CNC machines are capable of moving along five axes simultaneously: X, Y, Z and two additional rotary axes (commonly referred to as A and B). This additional freedom of movement allows cutting tools to approach the workpiece from multiple angles and directions, enabling highly complex machining operations. By tilting and rotating the workpiece or cutting tool, 5-axis CNC machines can accurately access hard-to-reach areas and execute complex tool paths. These machines are widely used in aerospace, automotive, medical device manufacturing and mold making. Examples of parts commonly produced on 5-Axis CNC machines include turbine blades, impellers, aerospace components, sculpted surfaces and complex molds.
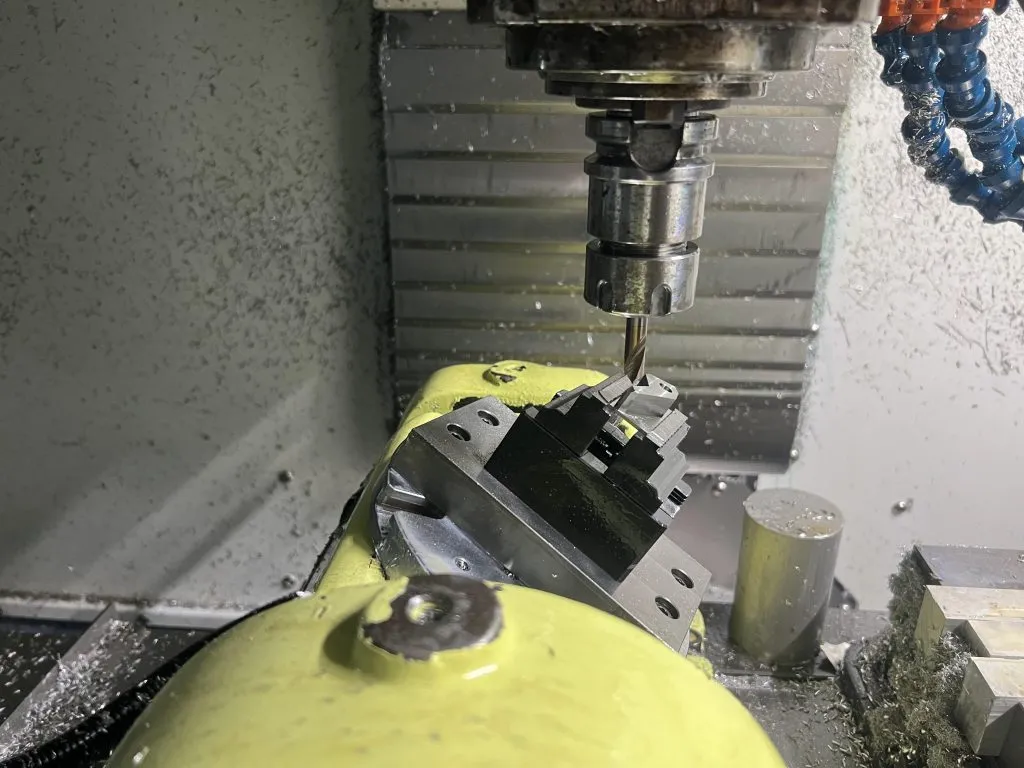
The versatility and flexibility offered by 5-axis machining translates into a number of benefits, including reduced setup times, improved surface finishes, increased accuracy, and increased productivity. In addition, 5-axis CNC machines can minimize the need to manually reposition workpieces, thereby streamlining production workflows and optimizing machining processes.
However, 5-axis machines are more costly and technically complex than 3-axis machines, and programming and operating these machines requires specialized skills and expertise, as well as potentially high initial investment and maintenance costs.
How to choose?
- Complexity of workpiece: 3-axis machining is sufficient for simple plane or small amount of surface machining; 4-axis or 5-axis machining can be considered for complex multi-angle machining.
- Accuracy requirements: 5-axis machining can complete all angles in one clamping, suitable for high precision requirements.
- Cost considerations: 3-axis machines are the least expensive and are suitable for mass production of simple parts; 4- and 5-axis machines are more expensive and are suitable for small quantities of highly complex parts.